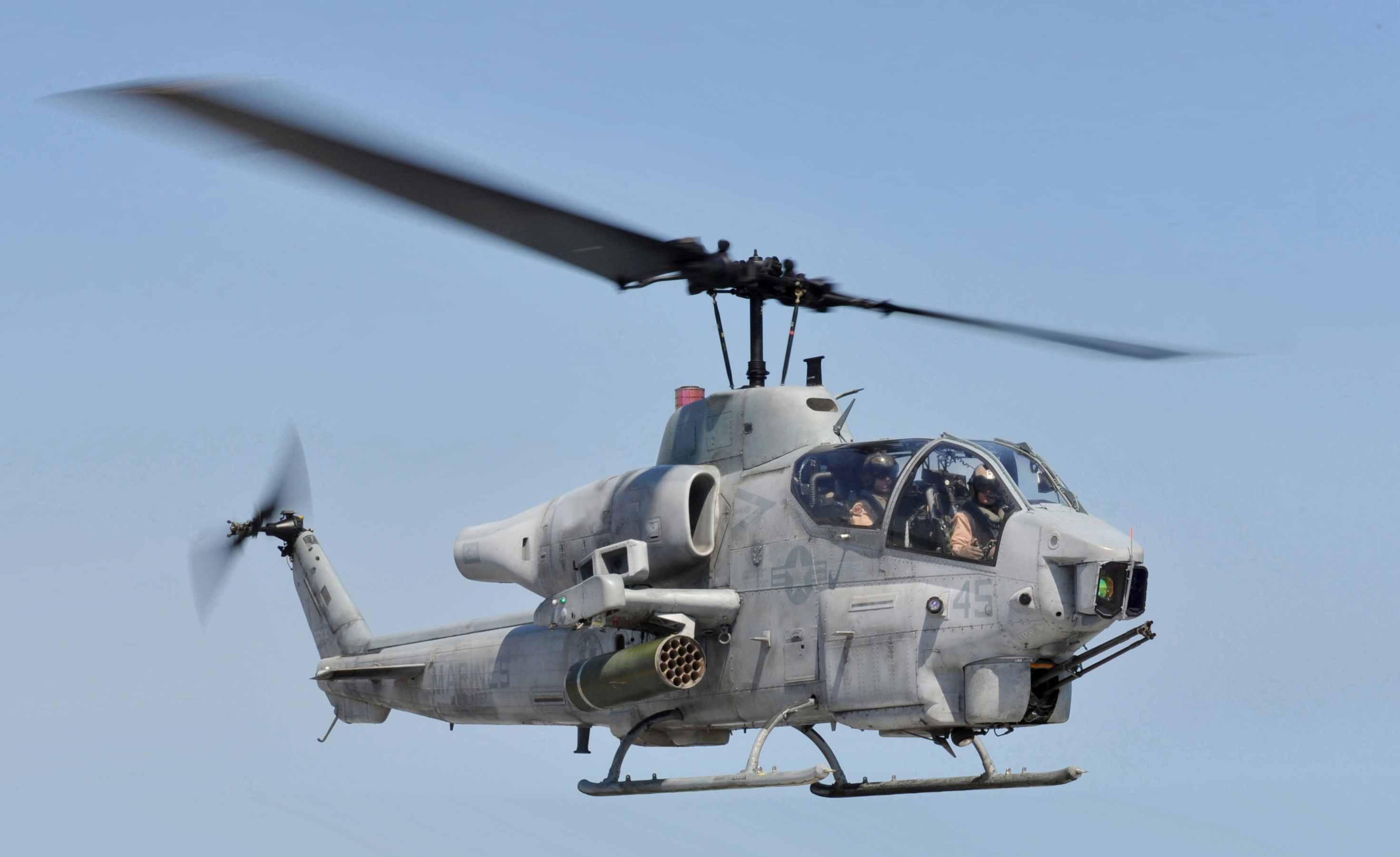
A helicopter main rotor or rotor system is the combination of several rotary wings (rotor blades) with a control system, that generates the aerodynamic
lift force that supports the weight of the
helicopter
A helicopter is a type of rotorcraft in which lift and thrust are supplied by horizontally spinning rotors. This allows the helicopter to take off and land vertically, to hover, and to fly forward, backward and laterally. These attribut ...
, and the
thrust
Thrust is a reaction force
In physics, a force is an influence that can change the motion of an object. A force can cause an object with mass to change its velocity (e.g. moving from a state of rest), i.e., to accelerate. Force can al ...
that counteracts
aerodynamic drag in forward flight. Each main rotor is mounted on a vertical mast over the top of the helicopter, as opposed to a helicopter
tail rotor, which connects through a combination of
drive shaft(s) and
gearbox
Propulsion transmission is the mode of transmitting and controlling propulsion power of a machine. The term ''transmission'' properly refers to the whole drivetrain, including clutch, gearbox, prop shaft (for rear-wheel drive vehicles), diffe ...
es along the tail boom. The
blade pitch
Blade pitch or simply pitch refers to the angle of a blade in a fluid. The term has applications in aeronautics, shipping, and other fields.
Aeronautics
In aeronautics, blade pitch refers to the angle of the blades of an aircraft propeller o ...
is typically controlled by the pilot using the
helicopter flight controls. Helicopters are one example of rotary-wing aircraft (
rotorcraft
A rotorcraft or rotary-wing aircraft is a heavier-than-air aircraft with rotary wings or rotor blades, which generate lift by rotating around a vertical mast. Several rotor blades mounted on a single mast are referred to as a rotor. The Inter ...
). The name is derived from the Greek words ''helix'', helik-, meaning spiral; and ''pteron'' meaning wing.
Design principles
Overview
The helicopter rotor is powered by the engine, through the transmission, to the rotating mast. The mast is a cylindrical metal shaft that extends upward from—and is driven by—the transmission. At the top of the mast is the attachment point (colloquially called a
Jesus nut
''Jesus nut'' is a slang term for the main rotor retaining nut or mast nut, which holds the main rotor to the mast of some helicopters. The related slang term Jesus pin refers to the lock pin used to secure the retaining nut. More generally, ''Je ...
) for the rotor blades called the hub. The rotor blades are then attached to the hub, and the hub can have 10-20 times the drag of the blade. Main rotor systems are classified according to how the main rotor blades are attached and move relative to the main rotor hub. There are three basic classifications: rigid, semirigid, and fully articulated, although some modern rotor systems use a combination of these classifications. A rotor is a finely tuned rotating mass, and different subtle adjustments reduce vibrations at different airspeeds.
The rotors are designed to operate at a fixed
RPM[Croucher, Phil]
Professional helicopter pilot studies
page 2-11. . Quote: otor speed"is constant in a helicopter". (within a narrow range of a few percent),
but a few experimental aircraft used
variable speed rotors.
[Datta, Anubhav et al. ]
Experimental Investigation and Fundamental Understanding of a Slowed UH-60A Rotor at High Advance Ratios
' page 2. ''NASA
The National Aeronautics and Space Administration (NASA ) is an independent agency of the US federal government responsible for the civil space program, aeronautics research, and space research.
NASA was established in 1958, succeedi ...
'' ARC-E-DAA-TN3233, 2011
Header
Accessed: May 2014. Size: 26 pages in 2MB
Unlike the small diameter fans used in
turbofan
The turbofan or fanjet is a type of airbreathing jet engine that is widely used in aircraft propulsion. The word "turbofan" is a portmanteau of "turbine" and "fan": the ''turbo'' portion refers to a gas turbine engine which achieves mechanical ...
jet engines, the main rotor on a helicopter has a large diameter that lets it accelerate a large volume of air. This permits a lower downwash velocity for a given amount of thrust. As it is more efficient at low speeds to accelerate a large amount of air by a small degree than a small amount of air by a large degree,
Paul Bevilaqua
Paul Bevilaqua is an aeronautics engineer at Lockheed Martin in California. In 1990, he invented the lift fan for the Joint Strike Fighter F-35B along with fellow Skunk Works engineer Paul Shumpert.
In 2005, Bevilaqua was elected as a member ...
The shaft driven Lift Fan propulsion system for the Joint Strike Fighter
page 3. Presented May 1, 1997. DTIC.MIL Word document, 5.5 MB. Accessed: 25 February 2012.[ a low disc loading (thrust per disc area) greatly increases the aircraft's energy efficiency, and this reduces the fuel use and permits reasonable range.][Johnson, Wayne]
Helicopter theory
pp3+32, ''Courier Dover Publications'', 1980. Accessed: 25 February 2012. [Wieslaw Zenon Stepniewski, C. N. Keys]
Rotary-wing aerodynamics
p3, ''Courier Dover Publications'', 1979. Accessed: 25 February 2012. The hover efficiency ("figure of merit")[Jackson, Dave.]
''Unicopter'', 16 December 2011. Retrieved: 22 May 2015
on 26 November 2013. of a typical helicopter is around 60%. The inner third length of a rotor blade contributes very little to lift due to its low airspeed.[ Bensen, Igor.]
How they fly - Bensen explains all
''Gyrocopters UK''. Accessed: 10 April 2014.
Blades
The blades of a helicopter are long, narrow airfoil
An airfoil (American English) or aerofoil (British English) is the cross-sectional shape of an object whose motion through a gas is capable of generating significant lift, such as a wing, a sail, or the blades of propeller, rotor, or tur ...
s with a high aspect ratio, a shape that minimizes drag from tip vortices (see the wings of a glider for comparison). They generally contain a degree of washout that reduces the lift generated at the tips, where the airflow is fastest and vortex
In fluid dynamics, a vortex ( : vortices or vortexes) is a region in a fluid in which the flow revolves around an axis line, which may be straight or curved. Vortices form in stirred fluids, and may be observed in smoke rings, whirlpools in t ...
generation would be a significant problem. Rotor blades are made out of various materials, including aluminium, composite structure, and steel or titanium
Titanium is a chemical element with the Symbol (chemistry), symbol Ti and atomic number 22. Found in nature only as an oxide, it can be reduced to produce a lustrous transition metal with a silver color, low density, and high strength, resista ...
, with abrasion shields along the leading edge.
Rotorcraft blades are traditionally passive; however, some helicopters include active components on their blades. The Kaman K-MAX
The Kaman K-MAX (company designation K-1200) is an American helicopter with intermeshing rotors (synchropter) by Kaman Aircraft. It is optimized for external cargo load operations, and is able to lift a payload of over , which is more than the ...
uses trailing edge flaps for blade pitch control and the Hiller YH-32 Hornet was powered by ramjets mounted on the blade ends. , research into active blade control through trailing edge flaps is underway.[Mangeot et al]
New actuators for aerospace
''Noliac''. Retrieved: 28 September 2010. Tips of some helicopter blades can be specially designed to reduce turbulence and noise and to provide more efficient flying. An example of such tips are the tips of the BERP rotors created during the British Experimental Rotor Programme.
Hub
The simple rotor of a Robinson R22 showing (from the top):
* The following are driven by the link rods from the rotating part of the swashplate.
** Pitch hinges, allowing the blades to twist about the axis extending from blade root to blade tip.
* Teeter hinge, allowing one blade to rise vertically while the other falls vertically. This motion occurs whenever translational relative wind is present, or in response to a cyclic control input.
* Scissor link and counterweight, carries the main shaft rotation down to the upper swashplate
* Rubber covers protect moving and stationary shafts
* Swashplates, transmitting cyclic and collective pitch to the blades (the top one rotates)
* Three non-rotating control rods transmit pitch information to the lower swashplate
* Main mast leading down to main gearbox
Propulsion transmission is the mode of transmitting and controlling propulsion power of a machine. The term ''transmission'' properly refers to the whole drivetrain, including clutch, gearbox, prop shaft (for rear-wheel drive vehicles), diffe ...
Fully articulated
Juan de la Cierva developed the fully articulating rotor for the autogyro
An autogyro (from Greek and , "self-turning"), also known as a ''gyroplane'', is a type of rotorcraft that uses an unpowered rotor in free autorotation to develop lift. Forward thrust is provided independently, by an engine-driven propeller. ...
. The basis of his design permitted successful helicopter development. In a fully articulated rotor system, each rotor blade is attached to the rotor hub through a series of hinges that let the blade move independently of the others. These rotor systems usually have three or more blades. The blades are allowed to flap, feather, and lead or lag independently of each other. The horizontal hinge, called the flapping hinge, allows the blade to move up and down. This movement is called flapping and is designed to compensate for dissymmetry of lift. The flapping hinge may be located at varying distances from the rotor hub, and there may be more than one hinge. The vertical hinge, called the lead-lag hinge or drag hinge, allows the blade to move back and forth. This movement is called lead-lag, dragging, or hunting. Dampers are usually used to prevent excess back and forth movement around the drag hinge. The purpose of the drag hinge and dampers is to compensate for acceleration and deceleration caused by the difference in drag experienced by the advancing and retreating blades. Later models have switched from using traditional bearings to elastomeric bearings. Elastomeric bearings are naturally fail-safe and their wear is gradual and visible. The metal-to-metal contact of older bearings and the need for lubrication is eliminated in this design. The third hinge in the fully articulated system is called the feathering hinge about the feathering axis. This hinge is responsible for the change in pitch of rotor blades excited via pilot input to the collective or cyclic.
A variation of the fully articulated system is the ''soft-in-plane'' rotor system. This type of rotor can be found on several aircraft produced by Bell Helicopter, such as the OH-58D Kiowa Warrior. This system is similar to the fully articulated type in that each blade has the ability to lead/lag and hunt independently of the other blades. The difference between a fully articulated system and soft-in-plane system is that the soft-in-plane system utilises a composite yoke. This yoke is attached to the mast and runs through the blade grips between the blades and the shear bearing inside the grip. This yoke does transfer some movement of one blade to another, usually opposing blades. While this is not fully articulated, the flight characteristics are very similar and maintenance time and cost are reduced.
Rigid
The term ''rigid rotor'' usually refers to a hingeless rotor system with blades flexibly attached to the hub. Irv Culver of Lockheed developed one of the first rigid rotors, which was tested and developed on a series of helicopters in the 1960s and 1970s. In a rigid rotor system, each blade flaps and drags about flexible sections of the root. A rigid rotor system is mechanically simpler than a fully articulated rotor system. The aerodynamic and mechanical loads from flapping and lead/lag forces are accommodated through rotor blades flexing, rather than through hinges. By flexing, the blades themselves compensate for the forces that previously required rugged hinges. The result is a rotor system that has less lag in control response because of the large hub moment typically generated.[Connor, R]
Lockheed CL-475"
Smithsonian National Air & Space Museum. Revised on 15 August 2002. Accessed at archive.org on 3 September 2007
. The rigid rotor system thus eliminates the danger of mast bumping inherent in semirigid rotors.[Cox, Taylor]
"Blades and Lift"
Helis.com. Retrieved: 10 March 2007.
Semirigid
The semirigid rotor can also be referred to as a teetering or seesaw rotor. This system is normally composed of two blades that meet just under a common flapping or teetering hinge at the rotor shaft. This allows the blades to flap together in opposite motions like a seesaw. This underslinging of the blades below the teetering hinge, combined with an adequate dihedral or coning angle on the blades, minimizes variations in the radius of each blade's center of mass from the axis of rotation as the rotor turns, which in turn reduces the stress on the blades from lead and lag forces caused by the Coriolis effect. Secondary flapping hinges may also be used to provide sufficient flexibility to minimize bouncing. Feathering is accomplished by the feathering hinge at the blade root, which allows changes to the pitch angle of the blade.
Combination
Modern rotor systems may use the combined principles of the rotor systems mentioned above. Some rotor hubs incorporate a flexible hub, which allows for blade bending (flexing) without the need for bearings or hinges. These systems, called ''flexures'',[FAA Flight Standards Service 2001] are usually constructed from composite material. Elastomeric bearings may also be used in place of conventional roller bearings. Elastomeric bearings are constructed from a rubber type material and provide limited movement that is perfectly suited for helicopter applications. Flexures and elastomeric bearings require no lubrication and, therefore, require less maintenance. They also absorb vibration, which means less fatigue and longer service life for the helicopter components.
Swash plate
Controls vary the pitch of the main rotor blades cyclically throughout rotation. The pilot uses this to control the direction of the rotor thrust vector, which defines the part of the rotor disc where the maximum thrust develops. Collective pitch varies the magnitude of rotor thrust by increasing or decreasing thrust over the whole rotor disc at the same time. These blade pitch variations are controlled by tilting, raising, or lowering the swash plate with the flight controls. The vast majority of helicopters maintain a constant rotor speed (RPM) during flight, leaving the angle of attack of the blades as the sole means of adjusting thrust from the rotor.
The swash plate is two concentric disks or plates. One plate rotates with the mast, connected by idle links, while the other does not rotate. The rotating plate is also connected to the individual blades through pitch links and pitch horns. The non-rotating plate is connected to links that are manipulated by pilot controls—specifically, the collective and cyclic controls. The swash plate can shift vertically and tilt. Through shifting and tilting, the non-rotating plate controls the rotating plate, which in turn controls the individual blade pitch.
Flybar (stabilizer bar)
A number of engineers, among them Arthur M. Young in the U.S. and radio-control aeromodeler Dieter Schlüter in Germany, found that flight stability for helicopters could be achieved with a stabilizer bar, or flybar. The flybar has a weight or paddle (or both for added stability on smaller helicopters) at each end to maintain a constant plane of rotation. Through mechanical linkages, the stable rotation of the bar mixes with the swashplate movement to damp internal (steering) as well as external (wind) forces on the rotor. This makes it easier for the pilot to maintain control of the aircraft. Stanley Hiller
Stanley Hiller Jr. (November 15, 1924 – April 20, 2006), was an American pioneering developer of the helicopter.
Biography
Stanley Hiller was born November 15, 1924, in San Francisco, California, to Stanley Hiller, Sr. and Opal Perkins. The fam ...
arrived at a similar method to improve stability by adding short stubby airfoils, or paddles, at each end. However, Hiller's "Rotormatic" system also delivered cyclic control inputs to the main rotor as a sort of control rotor, and the paddles provided the added stability by damping the effects of external forces on the rotor.
The Lockheed rotor system used a control gyro, similar in principle to that of the Bell stabilizer bar, but designed for both hands-off stability and rapid control response of the hingeless rotor system.
In fly-by-wire helicopters or Remote Control (RC) models, a microcontroller with gyroscope sensors and a Venturi sensor can replace the stabilizer. This ''flybar-less'' design has the advantage of easy reconfiguration and fewer mechanical parts.
Slowed rotor
Most helicopter rotors spin at constant speed. However slowing the rotor in some situations can bring benefits.
As forward speed increases, the advancing rotor tip speed soon approaches the speed of sound
The speed of sound is the distance travelled per unit of time by a sound wave as it propagates through an elastic medium. At , the speed of sound in air is about , or one kilometre in or one mile in . It depends strongly on temperature as ...
. To reduce the problem, the speed of rotation may be slowed, allowing the helicopter to fly faster.
To adjust the rotor lift at slower speeds, in a conventional design the rotor blades' angle of attack is reduced via a collective pitch control. Slowing the rotor instead can reduce drag during this phase of flight and thus improve fuel economy.
Rotor configurations
Most helicopters have a single main rotor but require a separate rotor to overcome torque. This is accomplished through a variable-pitch antitorque rotor or tail rotor. This is the design that Igor Sikorsky
Igor Ivanovich Sikorsky (russian: И́горь Ива́нович Сико́рский, p=ˈiɡərʲ ɪˈvanəvitʃ sʲɪˈkorskʲɪj, a=Ru-Igor Sikorsky.ogg, tr. ''Ígor' Ivánovich Sikórskiy''; May 25, 1889 – October 26, 1972)Fortie ...
settled on for his VS-300 helicopter, and it has become the recognized convention for helicopter design, although designs do vary. When viewed from above, most American helicopter rotors turn counter-clockwise; French and Russian helicopters turn clockwise.
Single main rotor
With a single main rotor helicopter, the creation of torque
In physics and mechanics, torque is the rotational equivalent of linear force. It is also referred to as the moment of force (also abbreviated to moment). It represents the capability of a force to produce change in the rotational motion of t ...
as the engine turns the rotor creates a torque effect that causes the body of the helicopter to turn in the opposite direction of the rotor. To eliminate this effect, some sort of antitorque control must be used with a sufficient margin of power available to allow the helicopter to maintain its heading and provide yaw control. The three most common controls used today are the tail rotor, Eurocopter's '' Fenestron'' (also called a ''fantail''), and MD Helicopters' '' NOTAR''.
Tail rotor
The tail rotor is a smaller rotor mounted so that it rotates vertically or near-vertically at the end of the tail of a traditional single-rotor helicopter. The tail rotor's position and distance from the center of gravity
In physics, the center of mass of a distribution of mass in space (sometimes referred to as the balance point) is the unique point where the weighted relative position of the distributed mass sums to zero. This is the point to which a force may ...
allow it to develop thrust in a direction opposite of the main rotor's rotation to counter the torque effect created by the main rotor. Tail rotors are simpler than main rotors since they require only collective changes in pitch to vary thrust. The pitch of the tail rotor blades is adjustable by the pilot via the anti-torque pedals, which also provide directional control by allowing the pilot to rotate the helicopter around its vertical axis, thereby changing the direction the craft is pointed.
Ducted fan
Fenestron and FANTAIL are trademarks
A trademark (also written trade mark or trade-mark) is a type of intellectual property consisting of a recognizable sign, design, or expression that identifies products or services from a particular source and distinguishes them from ot ...
for a ducted fan mounted at the end of the tail boom of the helicopter and used in place of a tail rotor. Ducted fans have between eight and eighteen blades arranged with irregular spacing so that the noise is distributed over different frequencies. The housing is integral with the aircraft skin and allows a high rotational speed; therefore, a ducted fan can have a smaller size than a conventional tail rotor.
The Fenestron was used for the first time at the end of the 1960s on the second experimental model of Sud Aviation's SA 340 and produced on the later model Aérospatiale
Aérospatiale (), sometimes styled Aerospatiale, was a French state-owned aerospace manufacturer that built both civilian and military aircraft, rockets and satellites. It was originally known as Société nationale industrielle aérospatiale ( ...
SA 341 Gazelle. Besides Eurocopter
Airbus Helicopters SAS (formerly Eurocopter Group) is the helicopter manufacturing division of Airbus. It is the largest in the industry in terms of revenues and turbine helicopter deliveries. Its head office is located at Marseille Provence A ...
and its predecessors, a ducted fan tail rotor was also used on the canceled military helicopter project, the United States Army
The United States Army (USA) is the land warfare, land military branch, service branch of the United States Armed Forces. It is one of the eight Uniformed services of the United States, U.S. uniformed services, and is designated as the Army o ...
's RAH-66 Comanche, as the FANTAIL.
NOTAR
NOTAR, an acronym for ''no tail rotor'', is a helicopter anti-torque system that eliminates the use of the tail rotor on a helicopter. Although the concept took some time to refine, the NOTAR system is simple in theory and provides antitorque the same way a wing develops lift by using the Coandă effect.[Frawley 2003, p. 151.] A variable pitch fan is enclosed in the aft fuselage section immediately forward of the tail boom and is driven by the main rotor transmission. To provide the sideways force to counteract the clockwise torque produced by a counterclockwise-spinning main rotor (as seen from above the main rotor), the variable-pitch fan forces low pressure air through two slots on the right side of the tailboom, causing the downwash from the main rotor to hug the tailboom, producing lift and thus a measure of antitorque proportional to the amount of airflow from the rotorwash. This is augmented by a direct jet thruster which also provides directional yaw control, with the presence of a fixed-surface empennage near the end of the tail, incorporating vertical stabilizers.
Development of the NOTAR system dates back to 1975 when engineers at Hughes Helicopters began concept development work. In December 1981, Hughes flew an OH-6A fitted with NOTAR for the first time. A more heavily modified prototype demonstrator first flew in March 1986 and successfully completed an advanced flight-test program, validating the system for future application in helicopter design.["The Boeing Logbook: 1983-1987"](_blank)
Boeing.com. Retrieved: 25 February 2007. There are currently three production helicopters that incorporate the NOTAR design, all produced by MD Helicopters. This antitorque design also improves safety by eliminating the possibility of personnel walking into the tail rotor.
A predecessor (of sorts) to this system existed in the form of Great Britain's Cierva W.9 helicopter, a late 1940s aircraft using the cooling fan from its piston engine to push air through a nozzle built into the tailboom to counteract rotor-torque.
Tip jets
The main rotor may be driven by tip jets. Such a system may be powered by high pressure air provided by a compressor. The air may or may not be mixed with fuel and burnt in ram-jets, pulse-jets, or rockets. Though this method is simple and eliminates torque reaction, prototypes that have been built are less fuel efficient than conventional helicopters. Except for tip jets driven by unburnt compressed air, very high noise levels is the single most important reason why tip jet powered rotors have not gained wide acceptance. However, research into noise suppression is ongoing and may help make this system viable.
There are several examples of tip jet powered rotorcraft. The Percival P.74 was under-powered and could not fly. The Hiller YH-32 Hornet had good lifting capability but performed poorly otherwise. Other aircraft used auxiliary thrust for translational flight so that the tip jets could be shut down while the rotor autorotated. The experimental Fairey Jet Gyrodyne, 48-seat Fairey Rotodyne passenger prototypes and McDonnell XV-1 compound gyroplanes flew well using this method. Perhaps the most unusual design of this type was the Rotary Rocket Roton ATV, which was originally envisioned to take off using a rocket-tipped rotor. The French Sud-Ouest Djinn used unburnt compressed air to drive the rotor, which minimized noise and helped it become the only tip jet driven rotor helicopter to enter production. The Hughes XH-17 had a tip jet-driven rotor, which remains the largest rotor ever fitted to a helicopter.
Twin rotors
Twin rotors turn in opposite directions to counteract the torque effect on the aircraft without relying on an antitorque tail rotor. This lets the aircraft apply the power that would have driven a tail rotor to the main rotors, increasing lifting capacity. Primarily, three common configurations use the counterrotating effect on rotorcraft. ''Tandem rotors'' are two rotors—one mounted behind the other. ''Coaxial rotors'' are two rotors mounted one above the other on the same axis. ''Intermeshing rotors'' are two rotors mounted close to each other at a sufficient angle to let the rotors intermesh over the top of the aircraft. Another configuration—found on tiltrotors and some early helicopters—is called transverse rotors, where a pair of rotors are mounted at each end of a wing-type structure or outrigger.
Tandem
Tandem rotors are two horizontal main rotor assemblies mounted one behind the other. Tandem rotors achieve pitch attitude
Attitude may refer to:
Philosophy and psychology
* Attitude (psychology), an individual's predisposed state of mind regarding a value
* Metaphysics of presence
* Propositional attitude, a relational mental state connecting a person to a prop ...
changes to accelerate and decelerate the helicopter through a process called cyclic pitch. To pitch forward and accelerate, both rotors increase the pitch at the rear and reduce the pitch at the front (cyclic) keeping torque the same on both rotors, flying sideways is achieved by increasing the pitch on one side and reducing pitch on the other. Yaw control develops through opposing cyclic pitch in each rotor. To pivot right, the front rotor tilts right and the rear rotor tilts left. To pivot left, the front rotor tilts left and the rear rotor tilts right. All rotor power contributes to lift, and it is simpler to handle changes in the center of gravity fore-aft. However, it requires the expense of two large rotors rather than the more common one large main rotor and a much smaller tail rotor. The Boeing CH-47 Chinook is the most common tandem rotor helicopter.
Coaxial
Coaxial rotors are a pair of rotors mounted one above the other on the same shaft and turning in opposite directions. The advantage of the coaxial rotor is that, in forward flight, the lift provided by the advancing halves of each rotor compensates for the retreating half of the other, eliminating one of the key effects of dissymmetry of lift: retreating blade stall. However, other design considerations plague coaxial rotors. There is an increased mechanical complexity of the rotor system because it requires linkages and swashplates for two rotor systems. Also, because the rotors must rotate in opposite directions, the mast is more complex, and control linkages for pitch changes to the upper rotor system must pass through the lower rotor system.
Intermeshing
Intermeshing rotors on a helicopter are a set of two rotors turning in opposite directions with each rotor mast mounted on the helicopter with a slight angle to the other so that the blades intermesh without colliding. This configuration is sometimes referred to as a synchropter. Intermeshing rotors have high stability and powerful lifting capability. The arrangement was pioneered in Nazi Germany
Nazi Germany (lit. "National Socialist State"), ' (lit. "Nazi State") for short; also ' (lit. "National Socialist Germany") (officially known as the German Reich from 1933 until 1943, and the Greater German Reich from 1943 to 1945) was ...
in 1939 with Anton Flettner's successful Flettner Fl 265 design, and later placed in limited production as the successful Flettner Fl 282 Kolibri
The Flettner Fl 282 ''Kolibri'' ("Hummingbird") is a single-seat intermeshing rotor helicopter, or ''synchropter'', produced by Anton Flettner of Germany. According to Yves Le Bec, the Flettner Fl 282 was the world's first series production hel ...
, used by the German ''Kriegsmarine
The (, ) was the navy of Germany from 1935 to 1945. It superseded the Imperial German Navy of the German Empire (1871–1918) and the inter-war (1919–1935) of the Weimar Republic. The was one of three official branches, along with th ...
'' in small numbers (24 airframes produced) as an experimental light anti-submarine warfare
Anti-submarine warfare (ASW, or in older form A/S) is a branch of underwater warfare that uses surface warships, aircraft, submarines, or other platforms, to find, track, and deter, damage, or destroy enemy submarines. Such operations are typi ...
helicopter. During the Cold War, an American company, Kaman Aircraft
Kaman Corporation is an American aerospace company, with headquarters in Bloomfield, Connecticut. It was founded in 1945 by Charles Kaman. During the first ten years the company operated exclusively as a designer and manufacturer of several he ...
, produced the HH-43 Huskie for USAF
The United States Air Force (USAF) is the Aerial warfare, air military branch, service branch of the United States Armed Forces, and is one of the eight uniformed services of the United States. Originally created on 1 August 1907, as a part ...
firefighting and rescue missions. The latest Kaman model, the Kaman K-MAX
The Kaman K-MAX (company designation K-1200) is an American helicopter with intermeshing rotors (synchropter) by Kaman Aircraft. It is optimized for external cargo load operations, and is able to lift a payload of over , which is more than the ...
, is a dedicated sky crane design.
Transverse
Transverse rotors are mounted on the end of wings or outriggers perpendicular to the body of the aircraft. Similar to tandem rotors and intermeshing rotors, the transverse rotor also uses differential collective pitch. But like the intermeshing rotors, the transverse rotors use the concept for changes in the roll attitude of the rotorcraft. This configuration is found on two of the first viable helicopters, the Focke-Wulf Fw 61 and the Focke-Achgelis Fa 223, as well as the world's largest helicopter ever built, the Mil Mi-12. It is also the configuration found on tiltrotor
A tiltrotor is an aircraft which generates lift and propulsion by way of one or more powered rotors (sometimes called ''proprotors'') mounted on rotating shafts or nacelles usually at the ends of a fixed wing. Almost all tiltrotors use a t ...
s such as the Bell-Boeing V-22 Osprey and the AgustaWestland AW609.
Quad rotor
Etienne Oehmichen, Paris, France, 192
Source
A quad rotor or quadrotor
A quadcopter or quadrotor is a type of helicopter with four rotors.
Although quadrotor helicopters and convertiplanes have long been flown experimentally, the configuration remained a curiosity until the arrival of the modern UAV or drone. ...
comprises four rotors in an "X" configuration. Rotors to the left and right are in a transverse configuration while those in the front and to the rear are in a tandem configuration.
An advantage of quad rotors on small aircraft such as drones is the opportunity for mechanical simplicity. A quadcopter using electric motors and fixed-pitch rotors has only four moving parts. Pitch, yaw and roll can be controlled by changing the relative lift of different rotor pairs without changing total lift.
The two families of airfoils are
* symmetrical airfoils
* asymmetrical airfoils
Symmetrical blades are very stable, which helps keep
blade twisting and flight control loads to a minimum.
This stability is achieved by keeping the
center of pressure virtually unchanged as the angle of
attack changes. Center of pressure is the imaginary
point on the chord line where the resultant of all aerodynamic
forces are considered to be concentrated.
Today, designers use thinner airfoils and obtain the
required rigidity by using composite materials.
Some airfoils are asymmetrical in design, meaning the
upper and lower surfaces do not have the same camber.
Normally these airfoils would not be as stable, but this
can be corrected by bending the trailing edge to produce
the same characteristics as symmetrical airfoils. This is
called "reflexing." Using this type of rotor blade allows
the rotor system to operate at higher forward speeds.
One of the reasons an asymmetrical rotor blade is not
as stable is that the center of pressure changes with
changes in angle of attack. When the center of pressure
lifting force is behind the pivot point on a rotor blade, it
tends to cause the rotor disc to pitch up. As the angle of
attack increases, the center of pressure moves forward.
If it moves ahead of the pivot point, the pitch of the
rotor disc decreases. Since the angle of attack of the
rotor blades is constantly changing during each cycle
of rotation, the blades tend to flap, feather, lead, and
lag to a greater degree.
Limitations and hazards
Helicopter
A helicopter is a type of rotorcraft in which lift and thrust are supplied by horizontally spinning rotors. This allows the helicopter to take off and land vertically, to hover, and to fly forward, backward and laterally. These attribut ...
s with teetering rotors—for example the two-blade system on the Bell
A bell is a directly struck idiophone percussion instrument. Most bells have the shape of a hollow cup that when struck vibrates in a single strong strike tone, with its sides forming an efficient resonator. The strike may be made by an inte ...
, Robinson and others—must not be subjected to a low-g condition because such rotor systems do not control the fuselage attitude. This can result in the fuselage assuming an attitude controlled by momentum and tail rotor thrust that causes the tail boom to intersect the main rotor tip-path plane or result in the blade roots contacting the main rotor drive shaft, causing the blades to separate from the hub (mast bumping).
Abrasion in sandy environments
When operating in sandy environments, sand hitting the moving rotor blades erodes their surface. This can damage the rotors and presents serious and costly maintenance problems.
Abrasion strips on helicopter rotor blades are made of metal, often titanium
Titanium is a chemical element with the Symbol (chemistry), symbol Ti and atomic number 22. Found in nature only as an oxide, it can be reduced to produce a lustrous transition metal with a silver color, low density, and high strength, resista ...
or nickel
Nickel is a chemical element with symbol Ni and atomic number 28. It is a silvery-white lustrous metal with a slight golden tinge. Nickel is a hard and ductile transition metal. Pure nickel is chemically reactive but large pieces are slow ...
, which are very hard, but less hard than sand. When a helicopter flies low to the ground in desert environments, sand striking the rotor blade can cause erosion. At night, sand hitting the metal abrasion strip causes a visible corona or halo around the rotor blades. The effect is caused by the pyrophoric
A substance is pyrophoric (from grc-gre, πυροφόρος, , 'fire-bearing') if it ignites spontaneously in air at or below (for gases) or within 5 minutes after coming into contact with air (for liquids and solids). Examples are organolith ...
oxidation of eroded particles, and by triboluminescence whereby impact with the sand particles produces photoluminesce.
The combat photographer and journalist Michael Yon observed the effect while accompanying U.S. soldiers in Afghanistan. When he discovered that the effect had no name he coined the name Kopp–Etchells effect
The Kopp–Etchells effect is a sparkling ring or disk that is sometimes produced by rotary-wing aircraft when operating in sandy conditions, particularly near the ground at night. The name was coined by photographer Michael Yon to honor two sold ...
after two soldiers who had died in the war, one American and one British.
History
The use of a rotor for vertical flight
Flight or flying is the process by which an object moves through a space without contacting any planetary surface, either within an atmosphere (i.e. air flight or aviation) or through the vacuum of outer space (i.e. spaceflight). This can b ...
has existed since 400 BC in the form of the bamboo-copter, an ancient Chinese toy.[Leishman, J. Gordon. ''Principles of Helicopter Aerodynamics''. Cambridge aerospace series, 18. Cambridge: ]Cambridge University Press
Cambridge University Press is the university press of the University of Cambridge. Granted letters patent by Henry VIII of England, King Henry VIII in 1534, it is the oldest university press in the world. It is also the King's Printer.
Cambr ...
, 2006. . pp. 7-9
Web extract
The bamboo-copter is spun by rolling a stick attached to a rotor. The spinning creates lift, and the toy flies when released. The philosopher Ge Hong
Ge Hong (; b. 283 – d. 343 or 364), courtesy name Zhichuan (稚川), was a Chinese linguist, Taoist practitioner, philosopher, physician, politician, and writer during the Eastern Jin dynasty. He was the author of '' Essays on Chinese Charact ...
's book the ''Baopuzi
The ''Baopuzi'' () is a literary work written by Ge Hong (also transliterated as Ko Hung) (), 283–343, a scholar during the turbulent Jin dynasty. ''Baopuzi'' is divided into two main sections, the esoteric ''Neipian'' () "Inner Chapters" an ...
'' (Master Who Embraces Simplicity), written around 317, describes the apocryphal use of a possible rotor in aircraft: "Some have made flying cars eiche 飛車 Eiche can refer to:
Places
* Eiche (Potsdam), a locality (''Ortsteil'') of Potsdam, Germany
* Eiche (Barnim), a locality (''Ortsteil'') of Ahrensfelde, Germany
* Eiche or Eichbach (Hahle), a short river in Eichsfeld district, Germany
Historica ...
with wood from the inner part of the jujube tree, using ox-leather (straps) fastened to returning blades so as to set the machine in motion." Leonardo da Vinci
Leonardo di ser Piero da Vinci (15 April 14522 May 1519) was an Italian polymath of the High Renaissance who was active as a painter, Drawing, draughtsman, engineer, scientist, theorist, sculptor, and architect. While his fame initially re ...
designed a machine known as an "aerial screw" with a rotor based on a water screw. The Russian polymath Mikhail Lomonosov developed a rotor based on the Chinese toy. The French naturalist Christian de Launoy constructed his rotor out of turkey feathers. Sir George Cayley
Sir George Cayley, 6th Baronet (27 December 1773 – 15 December 1857) was an English engineer, inventor, and aviator. He is one of the most important people in the history of aeronautics. Many consider him to be the first true scientific aer ...
, inspired by the Chinese toy in his childhood, created multiple vertical flight machines with rotors made of tin sheets. Alphonse Pénaud would later develop the coaxial rotor model helicopter toys in 1870, powered by rubber bands. One of these toys, given as a gift by their father, would inspire the Wright brothers to pursue the dream of flight.
Before development of powered helicopters in the mid 20th century, autogyro
An autogyro (from Greek and , "self-turning"), also known as a ''gyroplane'', is a type of rotorcraft that uses an unpowered rotor in free autorotation to develop lift. Forward thrust is provided independently, by an engine-driven propeller. ...
pioneer Juan de la Cierva researched and developed many of the fundamentals of the rotor. De la Cierva is credited with successful development of multi-bladed, fully articulated rotor systems. These systems, in their various modified forms, are the basis of most modern multi-bladed helicopter rotor systems.
The first successful attempt at a single-lift rotor helicopter design used a four-blade main rotor, as designed by Soviet aeronautical engineers Boris N. Yuriev and Alexei M. Cheremukhin, both working at the '' Tsentralniy Aerogidrodinamicheskiy Institut'' (TsAGI, the Central Aerohydrodynamic Institute) near Moscow
Moscow ( , US chiefly ; rus, links=no, Москва, r=Moskva, p=mɐskˈva, a=Москва.ogg) is the capital and largest city of Russia. The city stands on the Moskva River in Central Russia, with a population estimated at 13.0 million ...
in the early 1930s. Their TsAGI 1-EA helicopter was able to fly in low altitude testing in 1931–32, with Cheremukhin flying it as high as 605 meters (1,985 ft) by mid-August 1932.[Savine, Alexandre]
"TsAGI 1-EA."
''ctrl-c.liu.se,'' 24 March 1997. Retrieved 12 December 2010.
In the 1930s, Arthur Young improved the stability of two-bladed rotor systems with the introduction of a stabilizer bar. This system was used in several Bell
A bell is a directly struck idiophone percussion instrument. Most bells have the shape of a hollow cup that when struck vibrates in a single strong strike tone, with its sides forming an efficient resonator. The strike may be made by an inte ...
and Hiller helicopter models. The Hiller system variant using airfoiled paddles at the flybar's ends has been used in many of the earliest designs of remote control model helicopters, from their 1970s origins onwards to the very early 21st century.
In the late 1940s, the making of helicopter rotor blades was a job that inspired John T. Parsons to be a pioneer of numerical control (NC). NC and CNC (computerized numerical control) turned out to be an important new technology that later affected all machining industries.
References
External links
Rotor Analysis - Blade Element Momentum Theory
"Helicopter Aircraft"
US Patent 2,368,698, for flybar invention, by Arthur Young
{{DEFAULTSORT:Helicopter Rotor
Rotor
Rotor
Chinese inventions
Leonardo da Vinci projects