Thick-film technology is used to produce electronic devices/modules such as
surface mount devices modules,
hybrid integrated circuit
A hybrid integrated circuit (HIC), hybrid microcircuit, hybrid circuit or simply hybrid is a miniaturized electronic circuit constructed of individual devices, such as semiconductor devices (e.g. transistors, diodes or monolithic ICs) and p ...
s,
heating element
A heating element converts electrical energy into heat through the process of Joule heating. Electric current through the element encounters resistance, resulting in heating of the element. Unlike the Peltier effect, this process is independe ...
s,
integrated passive devices
Integrated passive devices (IPDs), also known as integrated passive components (IPCs) or embedded passive components (EPC), are electronic components where resistors (R), capacitors (C), inductors (L)/coils/chokes, microstriplines, impedance matchi ...
and
sensors. Main manufacturing technique is screen printing (
stencil
Stencilling produces an image or pattern on a surface, by applying pigment to a surface through an intermediate object, with designed holes in the intermediate object, to create a pattern or image on a surface, by allowing the pigment to reach ...
ing), which in addition to use in manufacturing electronic devices can also be used for various graphic reproduction targets. It became one of the key manufacturing/miniaturisation techniques of electronic devices/modules during 1950s. Typical film thickness – manufactured with thick film manufacturing processes for electronic devices – is 0.0001 to 0.1 mm.
Thick-film circuits/modules are widely used in the automotive industry, both in sensors, e.g. mixture of fuel/air, pressure sensors, engine and gearbox controls, sensor for releasing airbags, ignitors to airbags; common is that high reliability is required, often extended temperature range also along massive thermocycling of circuits without failure. Other application areas are space electronics, consumer electronics, and various measurement systems where low cost and/or high reliability is needed.
The simplest form to utilise a thick film technology is a module substrate/board, where wiring is manufactured using thick film process. Additionally resistors and large tolerance capacitors can be manufactured with thick film methods. Thick film wiring can be made compatible with
surface-mount technology
Surface-mount technology (SMT), originally called planar mounting, is a method in which the electrical components are mounted directly onto the surface of a printed circuit board (PCB). An electrical component mounted in this manner is referred ...
(SMT), and if needed (due to tolerances and/or size requirements) surface-mountable parts (resistors, capacitors, ICs, etc.) can be assembled on a thick film substrate.
The manufacturing of thick film devices/modules is an additive process involving deposition of several (typically max 6–8) successive layers of conductive, resistive and dielectric layers onto an electrically insulating substrate using a
screen-printing
Screen printing is a printing technique where a mesh is used to transfer ink (or dye) onto a substrate, except in areas made impermeable to the ink by a blocking stencil. A blade or squeegee is moved across the screen to fill the open mes ...
process.
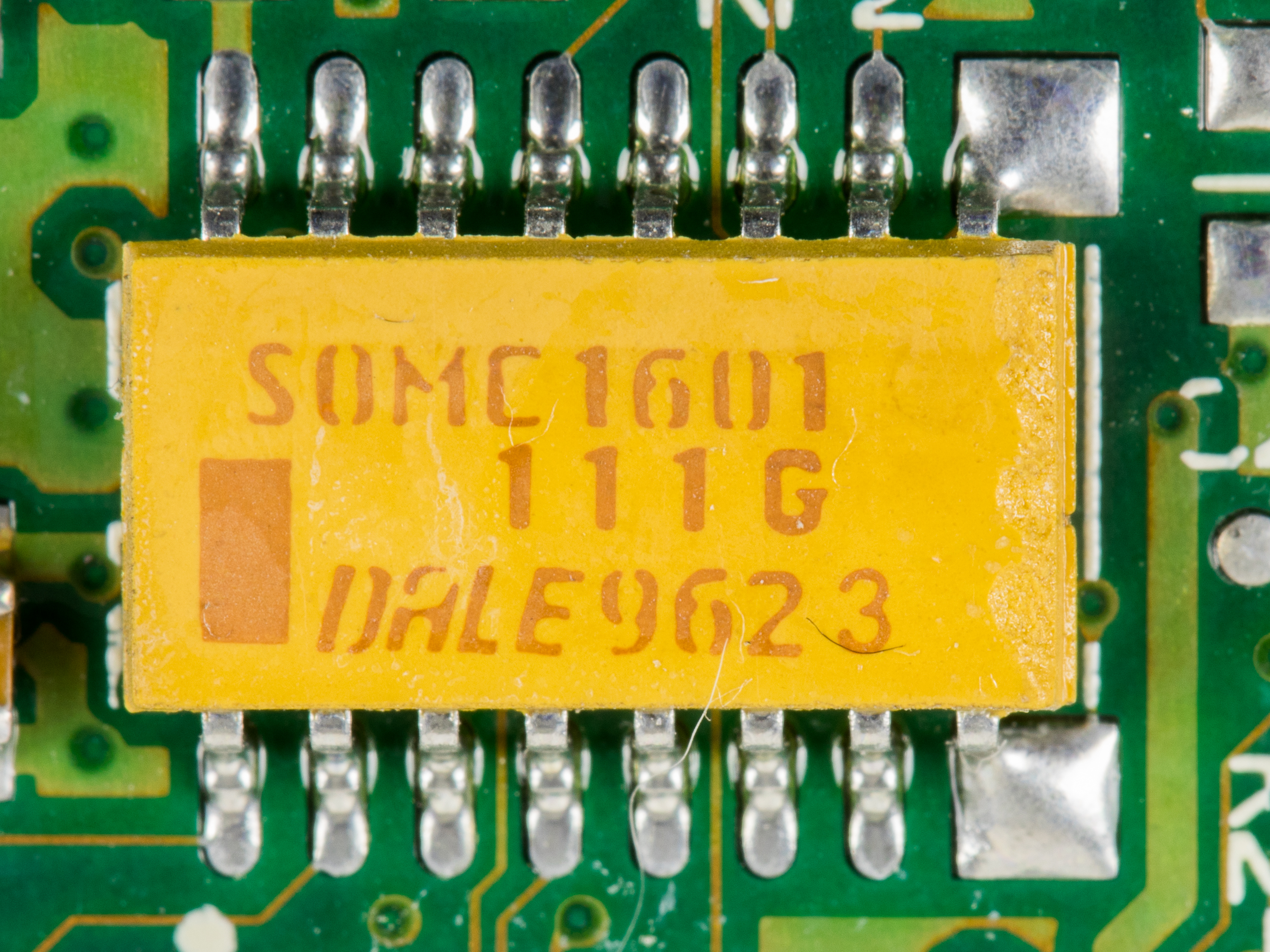
As a low cost manufacturing method it is applicable to produce large volumes of discrete passive devices like
resistor
A resistor is a passive two-terminal electrical component that implements electrical resistance as a circuit element. In electronic circuits, resistors are used to reduce current flow, adjust signal levels, to divide voltages, bias activ ...
s,
thermistor
A thermistor is a type of resistor whose resistance is strongly dependent on temperature, more so than in standard resistors. The word thermistor is a portmanteau of ''thermal'' and ''resistor''.
Thermistors are divided based on their conduction ...
s,
varistor
A varistor is an electronic component with an electrical resistance that varies with the applied voltage. Also known as a voltage-dependent resistor (VDR), it has a nonlinear, non- ohmic current–voltage characteristic that is similar to that ...
s and
integrated passive devices
Integrated passive devices (IPDs), also known as integrated passive components (IPCs) or embedded passive components (EPC), are electronic components where resistors (R), capacitors (C), inductors (L)/coils/chokes, microstriplines, impedance matchi ...
.
Thick film technology is also one of the alternatives to be used in
hybrid integrated circuit
A hybrid integrated circuit (HIC), hybrid microcircuit, hybrid circuit or simply hybrid is a miniaturized electronic circuit constructed of individual devices, such as semiconductor devices (e.g. transistors, diodes or monolithic ICs) and p ...
s and competes and complements typically in electronics
miniaturization
Miniaturization ( Br.Eng.: ''Miniaturisation'') is the trend to manufacture ever smaller mechanical, optical and electronic products and devices. Examples include miniaturization of mobile phones, computers and vehicle engine downsizing. In e ...
(parts or elements/area or volume) with SMT based on PCB (
printed circuit board
A printed circuit board (PCB; also printed wiring board or PWB) is a medium used in electrical and electronic engineering to connect electronic components to one another in a controlled manner. It takes the form of a laminated sandwich str ...
)/PWB (printed wiring board) and
thin film
A thin film is a layer of material ranging from fractions of a nanometer ( monolayer) to several micrometers in thickness. The controlled synthesis of materials as thin films (a process referred to as deposition) is a fundamental step in many a ...
technology.
Steps
A typical thick-film process would consist of the following stages:
Lasering of substrates
Typically thick film circuit substrates are Al
2O
3/
alumina,
beryllium oxide
Beryllium oxide (BeO), also known as beryllia, is an inorganic compound with the formula BeO. This colourless solid is a notable electrical insulator with a higher thermal conductivity than any other non-metal except diamond, and exceeds that of ...
(BeO),
aluminum nitride (AlN),
stainless steel, sometimes even some polymers and in rare cases even
silicon
Silicon is a chemical element with the symbol Si and atomic number 14. It is a hard, brittle crystalline solid with a blue-grey metallic luster, and is a tetravalent metalloid and semiconductor. It is a member of group 14 in the periodic ...
(Si) coated with silicon dioxide (SiO
2)., Commonly used substrates for thick-film processes are 94 or 96% alumina. Alumina is very hard and lasering of the material is the most efficient way to machine it. The thick-film process is also a means of miniaturization, where one substrate normally contains many units (final circuits). With lasering it is possible to scribe, profile and drill holes. Scribing is a process where a line of laser pulses is fired into the material and 30–50% of the material is removed; this weakens the substrate, and after all other processes are completed the substrate can easily be divided into single units.
Profiling is, for example, used a lot in sensor fabrication, where a circuit needs to fit round tubes or other different complex shapes.
Drilling of holes can provide a "via" (conductive link) between the two sides of the substrate, normally hole sizes are in the range 0.15–0.2 mm.
Lasering before processing the substrates has a cost advantage to lasering or dicing using a diamond saw after processing.
Ink preparation
Inks for electrodes, terminals, resistors, dielectric layers etc. are commonly prepared by mixing the metal or ceramic powders required with a solvent (ceramic thick film pastes) or polymer pastes to produce a paste for screen-printing. To achieve a homogeneous ink the mixed components of the ink may be passed through a three-roll mill. Alternatively, ready-made inks may be obtained from several companies offering products for the thick-film technologist.
Screen-printing and its improvements
Screen-printing is the process of transferring an ink through a patterned woven mesh screen or stencil using a
squeegee
A squeegee or squilgee is a tool with a flat, smooth rubber blade, used to remove or control the flow of liquid on a flat surface. It is used for cleaning and in printing.
The earliest written references to squeegees date from the mid-19th cent ...
.
For improving accuracy, increasing integration density and improving line and space accuracy of traditional screen-printing
photoimageable thick-film technology has been developed. Use of these materials however changes typically the process flow and needs different manufacturing tools.
Drying/Curing
After allowing time after printing for settling of the ink, each layer of ink that is deposited is usually dried at a moderately high temperature of to evaporate the liquid component of the ink and fix the layer temporarily in position on the substrate so that it can be handled or stored before final processing. For inks based on polymers and some solder pastes that cure at these temperatures, this may be the final step that is required. Some inks also require
curing
A cure is a completely effective treatment for a disease.
Cure, or similar, may also refer to:
Places
* Cure (river), a river in France
* Cures, Sabinum, an ancient Italian town
* Cures, Sarthe, a commune in western France
People
* Curate or ...
by exposure to
UV light.
Firing
For many of the metal, ceramic and glass inks used in thick film processes a high temperature (usually greater than 300 °C) firing is required to fix the layers in position permanently on the substrate.
Abrasive Trimming of resistors
After firing the resistors can be trimmed using a precision abrasive cutting method first developed by S.S. White. The method involves a fine abrasive media, usually 0.027 mm aluminum oxide. The abrasive cutting is fed through a carbide nozzle tip that can be of different sizes. The nozzle is advanced through the fired resistor while the resistor element is monitored with probe contacts and when final value is reached the abrasive blast is shut off and the nozzle retracts to the zero start position. The abrasive technique can achieve very high tolerances with no heat and no cracking of the glass frit used in the ink formulation.
Laser trimming of resistors
After firing, the substrate resistors are trimmed to the correct value. This process is named
laser trimming. Many chip resistors are made using thick-film technology. Large substrates are printed with resistors fired, divided into small chips and these are then terminated, so they can be soldered on the PCB board. With laser trimming two modes are used; either passive trimming, where each resistor is trimmed to a specific value and tolerance, or active trimming, where the feedback is used to adjust to a specific voltage, frequency or response by laser trimming the resistors on the circuit while powered up.
Mounting of capacitors and semiconductors
The development of the SMT process actually evolves from the thick film process. Also mounting of naked dies (the actual silicon chip without encapsulation) and wire bonding is a standard process, this provides the basis for miniaturization of the circuits as all the extra encapsulation is not necessary.
Separation of elements
This step is often necessary because many components are produced on one substrate at the same time. Thus, some means of separating the components from each other is required. This step may be achieved by
wafer dicing
In the context of manufacturing integrated circuits, wafer dicing is the process by which die are separated from a wafer of semiconductor following the processing of the wafer. The dicing process can involve scribing and breaking, mechanical s ...
.
Integration of devices
At this stage, the devices may require integrating with other electronic components, usually in the form of a printed circuit board. This may be achieved by
wire bonding
Wire bonding is the method of making interconnections between an integrated circuit (IC) or other semiconductor device and its integrated circuit packaging, packaging during Fabrication (semiconductor), semiconductor device fabrication. Altho ...
or
soldering
Soldering (; ) is a process in which two or more items are joined by melting and putting a filler metal ( solder) into the joint, the filler metal having a lower melting point than the adjoining metal. Unlike welding, soldering does not in ...
.
Process control of thick film manufacturing
There are numerous steps in the thick film manufacturing, which need careful control like roughness of the substrate, curing temperatures and times of pastes, selected stencil thickness vs. paste type etc.,
Therefore number of used pastes and process steps define the complexity of the process and cost of the final product.
Designing circuits based on thick-film technology
Same or similar
electronic design automation
Electronic design automation (EDA), also referred to as electronic computer-aided design (ECAD), is a category of software tools for designing electronic systems such as integrated circuits and printed circuit boards. The tools work together ...
tools which are used for designing
printed circuit board
A printed circuit board (PCB; also printed wiring board or PWB) is a medium used in electrical and electronic engineering to connect electronic components to one another in a controlled manner. It takes the form of a laminated sandwich str ...
s can be used for designing thick film circuits. However, the compatibility of tooling formats with stencil manufacturing/manufacturer needs attention as well as the availability of the geometrical, electrical and thermal design rules for simulation and layout design from the final manufacturer.
See also
*
Thin film
A thin film is a layer of material ranging from fractions of a nanometer ( monolayer) to several micrometers in thickness. The controlled synthesis of materials as thin films (a process referred to as deposition) is a fundamental step in many a ...
*
Integrated passive devices
Integrated passive devices (IPDs), also known as integrated passive components (IPCs) or embedded passive components (EPC), are electronic components where resistors (R), capacitors (C), inductors (L)/coils/chokes, microstriplines, impedance matchi ...
*
Thermistor
A thermistor is a type of resistor whose resistance is strongly dependent on temperature, more so than in standard resistors. The word thermistor is a portmanteau of ''thermal'' and ''resistor''.
Thermistors are divided based on their conduction ...
*
Surface-mount technology
Surface-mount technology (SMT), originally called planar mounting, is a method in which the electrical components are mounted directly onto the surface of a printed circuit board (PCB). An electrical component mounted in this manner is referred ...
*
Hybrid integrated circuit
A hybrid integrated circuit (HIC), hybrid microcircuit, hybrid circuit or simply hybrid is a miniaturized electronic circuit constructed of individual devices, such as semiconductor devices (e.g. transistors, diodes or monolithic ICs) and p ...
References
External links
A course developed by Budapest University of Technology and Economics (BTE), Dept. of Electronics Technology concerning Technology of electronics products, chapter "Thick Film"A blog under EDN comparing thick and thin film resistorsA presentation describing the usage of the thick film technology for radio frequenciesThick-film components for industrial applications
{{DEFAULTSORT:Thick Film Technology
Electronics manufacturing