Rotary friction welding (RFW) one of the methods of
friction welding
Friction welding (FRW) is a solid-state welding process that generates heat through mechanical friction between workpieces in relative motion to one another, with the addition of a lateral force called "upset" to plastically displace and fuse the m ...
, the classic way of which uses the
work of friction to create a not separable
weld. Typically one welded element is rotated to the other and forge (pressed down by axial force). The heating of the material is caused by friction work and creates a permanent connection. In this method can be welded the same, dissimilar, or composite
and non-metallic materials. The friction welding methods of are often considered as solid-state welding.
History

Some applications and patents connected with friction welding were dated back to the turn of the 20th century,
and rotary friction welding is the oldest of these methods.
W. Richter patented the method of linear friction welding (LFW) process in 1924 in
England
England is a country that is part of the United Kingdom. It shares land borders with Wales to its west and Scotland to its north. The Irish Sea lies northwest and the Celtic Sea to the southwest. It is separated from continental Europe b ...
and 1929 in
Germany
Germany,, officially the Federal Republic of Germany, is a country in Central Europe. It is the second most populous country in Europe after Russia, and the most populous member state of the European Union. Germany is situated betwe ...
; however, the description of the process was vague
and H.Klopstock patented the same process in the USSR 1924.
But first description and experiments related to rotary friction welding took place in the
Soviet Union
The Soviet Union,. officially the Union of Soviet Socialist Republics. (USSR),. was a transcontinental country that spanned much of Eurasia from 1922 to 1991. A flagship communist state, it was nominally a federal union of fifteen national ...
in 1956,
machinist named A. J. Chdikov (А. И. Чудиков
) has realized scientific studies and suggested the use of this welding method as a commercial process
at first he discovered the method by accident in Elbrussky mine where he worked, he did not pay enough attention and not lubricate the lathe chuck inside and then it turned out that he had welded the workpiece to the lathe.
He wondered if this accident can be used for joining and came to conclusion that it was necessary to work at high rotation speeds (in these times about 1000 turnover per second), immediately brake and press down welded components.
He decided to write a letter to the
Ministry of Metallurgy and received the answer that this welding was inappropriate, but small note about the method was published in the newspaper and aroused interest with Yu. Ya. Terentyeva who was manager in Scientific Research Institute of Electrical Welding Equipment, and with time his method was disseminated.
The process was introduced to the
USA
The United States of America (U.S.A. or USA), commonly known as the United States (U.S. or US) or America, is a country Continental United States, primarily located in North America. It consists of 50 U.S. state, states, a Washington, D.C., ...
in 1960.
The American companies
Caterpillar Tractor Company (
Caterpillar - CAT),
Rockwell International
Rockwell International was a major American manufacturing conglomerate involved in aircraft, the space industry, defense and commercial electronics, components in the automotive industry, printing presses, avionics and industrial products. R ...
, and
American Manufacturing Foundry all developed machines for this process. Patents were also issued throughout
Europe
Europe is a large peninsula conventionally considered a continent in its own right because of its great physical size and the weight of its history and traditions. Europe is also considered a Continent#Subcontinents, subcontinent of Eurasia ...
and the former Soviet Union. The first studies of friction welding in England were carried out by the Welding Institute in 1961.
The US with
Caterpillar Tractor Company and MTI developed an inertia process in 1962.
Europe with
KUKA AG and Thompson launches rotary friction welding for industrial applications in 1966, developed a direct-drive process and in 1974 builds rRS6 the double spindle machine for heavy truck axles.
In 1997, international patent application was filed entitled "Method of Friction Welding Tubular Members", A. Graham was presented welding pipes with a diameter of 152.4 mm a method that uses radial friction welding with an intermediate ring for connect long pipes,
but some attempts occurred earlier in 1975 through methods called radial friction welding (RF),
and even earlier, for example specialists from Leningrad mention about possibility of use ring to connect long components and it was written before the 1960s in newspaper.
Another method was invented and experimentally proven at
The Welding Institute
The Welding Institute (TWI Ltd) is a research and technology organisation, with a specialty in welding. It has had headquarters near Cambridge, England, since 1946, and has other facilities across the UK and around the world. TWI works across a ...
(TWI) in the
UK and patented in 1991
Friction stir welding
Friction stir welding (FSW) is a solid-state joining process that uses a non-consumable tool to join two facing workpieces without melting the workpiece material. Heat is generated by friction between the rotating tool and the workpiece material ...
(FSW) process.
In 2008
KUKA AG developed the rotary friction welding machine SRS 1000 with a forged force of 1000 tons.
An improved modification is also Low Force Friction Welding, hybrid technology developed by EWI an
Manufacturing Technology Inc. (MTI) the process can apply to both linear and rotary friction welding.
Based on information from 2020 year only
KUKA
KUKA is a German manufacturer of industrial robots and systems for factory automation. It has been predominantly owned by the Chinese company Midea Group since 2016.
The KUKA Robotics Corporation has 25 subsidiaries, mostly sales and servic ...
has been operating in 44 country and has initiated more than 1200 systems
also for subcontract facility however there are more companies in the world and for example
The Welding Institute
The Welding Institute (TWI Ltd) is a research and technology organisation, with a specialty in welding. It has had headquarters near Cambridge, England, since 1946, and has other facilities across the UK and around the world. TWI works across a ...
TWI have more than 50 years expertise and insight inherent to process development. However, there are more companies not every is promoted but today, friction welding is conducted worldwide with various materials both in scientific studies and industrial applications.
Applications
Rotary friction welding is widely implemented across the manufacturing sector and has been used for numerous applications,
including:
* Parts in gas turbine such as: turbine shafts, turbine discs, compressor drums,
*Automotive parts including steel truck axles and casings, hollow valve, motor hollow pistons, passenger car wheel rims, converter for passenger car automatic gears,
*Turbine for aircraft engine,
* Monel to steel marine fittings,
*
Piston rod
In a piston engine, a piston rod joins a piston to the crosshead and thus to the connecting rod that drives the crankshaft or (for steam locomotives) the driving wheels.
Internal combustion engines, and in particular all current automobile engin ...
s,
*
Copper
Copper is a chemical element with the symbol Cu (from la, cuprum) and atomic number 29. It is a soft, malleable, and ductile metal with very high thermal and electrical conductivity. A freshly exposed surface of pure copper has a pinkis ...
-
aluminium
Aluminium (aluminum in American and Canadian English) is a chemical element with the symbol Al and atomic number 13. Aluminium has a density lower than those of other common metals, at approximately one third that of steel. I ...
electrical connections,
*Heat exchangers,
* Cutting tools,
*Drill pipes,
*Reactor pressure vassels nozzles,
*Tubular transition joints combining dissimilar metals (
Aluminium
Aluminium (aluminum in American and Canadian English) is a chemical element with the symbol Al and atomic number 13. Aluminium has a density lower than those of other common metals, at approximately one third that of steel. I ...
-
Titanium
Titanium is a chemical element with the symbol Ti and atomic number 22. Found in nature only as an oxide, it can be reduced to produce a lustrous transition metal with a silver color, low density, and high strength, resistant to corrosion in ...
and Aluminium -
Stainless steel
Stainless steel is an alloy of iron that is resistant to rusting and corrosion. It contains at least 11% chromium and may contain elements such as carbon, other nonmetals and metals to obtain other desired properties. Stainless steel's corros ...
),
*Potential for medical applications,
*For learning students at technical universities.
Connections geometry

Rotary Friction Welding can join a wide range of part geometries Typically:
Tube to Tube, Tube to Plate, Tube to Bar, Tube to Disk, Bar to Bar, Bar to Plate and in addition, to this a rotating ring is used to connect long components.

Geometry of the component surface not is not always
flat
Flat or flats may refer to:
Architecture
* Flat (housing), an apartment in the United Kingdom, Ireland, Australia and other Commonwealth countries
Arts and entertainment
* Flat (music), a symbol () which denotes a lower pitch
* Flat (soldier), ...
for example it can be
conical
A cone is a three-dimensional geometric shape that tapers smoothly from a flat base (frequently, though not necessarily, circular) to a point called the apex or vertex.
A cone is formed by a set of line segments, half-lines, or lines conn ...
surface and not only.
Types of materials to be welded
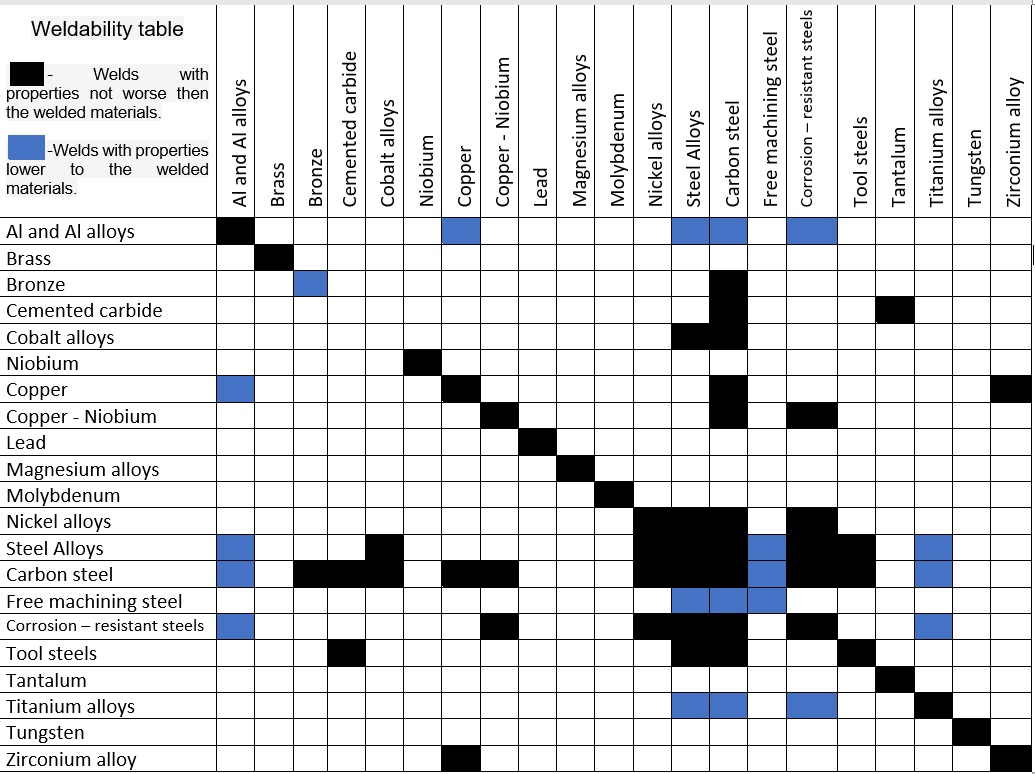
In rotary friction welding enables to weld various materials.
Metal
A metal (from Greek μέταλλον ''métallon'', "mine, quarry, metal") is a material that, when freshly prepared, polished, or fractured, shows a lustrous appearance, and conducts electricity and heat relatively well. Metals are typicall ...
lic materials of the same name or dissimilar either
composite
Composite or compositing may refer to:
Materials
* Composite material, a material that is made from several different substances
** Metal matrix composite, composed of metal and other parts
** Cermet, a composite of ceramic and metallic materials
...
,
superalloy
A superalloy, or high-performance alloy, is an alloy with the ability to operate at a high fraction of its melting point. Several key characteristics of a superalloy are excellent mechanical strength, resistance to thermal creep deformation, g ...
s
and non-metallic e.g.
thermoplastic
A thermoplastic, or thermosoft plastic, is any plastic polymer material that becomes pliable or moldable at a certain elevated temperature and solidifies upon cooling.
Most thermoplastics have a high molecular weight. The polymer chains associate ...
polymers
can be welded and even welding of wood is investigated, however welding a wood is not a good idea.
Weldability The weldability, also known as joinability,. of a material refers to its ability to be welded. Many metals and thermoplastics can be welded, but some are easier to weld than others (see Rheological weldability). A material's weldability is used to ...
tables of metallic alloy can be found on th
Internetand in books.
Sometimes an interlayer is used to connect non-compatible materials.
Rotary friction welding for plastics
Friction welding is also used to join
thermoplastic
A thermoplastic, or thermosoft plastic, is any plastic polymer material that becomes pliable or moldable at a certain elevated temperature and solidifies upon cooling.
Most thermoplastics have a high molecular weight. The polymer chains associate ...
components.
Division due to drive motor
In ''direct-drive friction welding'' (also called continuous drive friction welding) the drive motor and chuck are connected. The drive motor is continually driving the chuck during the heating stages. Usually, a clutch is used to disconnect the drive motor from the chuck, and a brake is then used to stop the chuck.
In ''inertia friction welding'' the drive motor is disengaged, and the workpieces are forced together by a friction welding force. The kinetic energy stored in the rotating flywheel is dissipated as heat at the weld interface as the flywheel speed decreases. Before welding, one of the workpieces is attached to the rotary chuck along with a
flywheel
A flywheel is a mechanical device which uses the conservation of angular momentum to store rotational energy; a form of kinetic energy proportional to the product of its moment of inertia and the square of its rotational speed. In particular, ass ...
of a given weight. The piece is then spun up to a high rate of rotation to store the required energy in the flywheel. Once spinning at the proper speed, the motor is removed and the pieces forced together under pressure. The force is kept on the pieces after the spinning stops to allow the weld to "set".
[Rotary Friction Welding](_blank)
video and schematic diagram
Stages of process

*Step 1 and 2, friction stage: one of the component is set in rotation, and then pressed to the other stationary one in axial of rotation,
* Step 3, braking stage: the rotating component is stopped in braking time,
* Step 4, upsetting stage: the welded elements are still forging by forge pressure (pressed down),
*Step 5: in standard RFW welding (standard parameters), a flash will be created. Flash can be cut off on the welder.
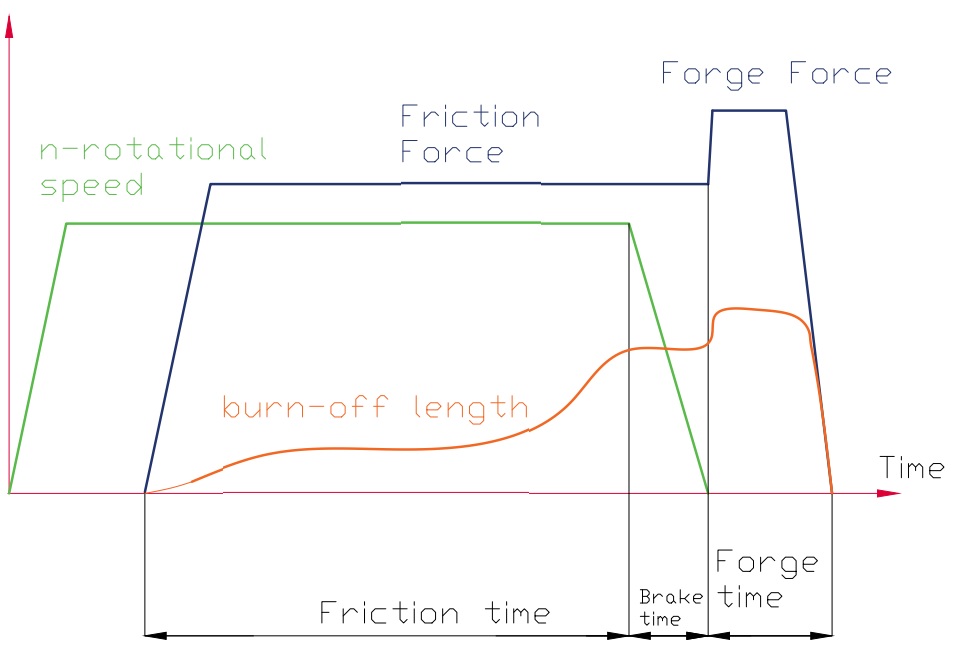
However, referring to the stages chart:
* modifications of the process exist,
*may depend on the version of the process: direct-drive, inertia friction welding, hybryd welding,
* there are many versions of welding machines,
* many materials can are welded with not the same properties, with various geometries,
* the real life process does not have to match to the ideal settings on the welding machine.
RFW Friction work on cylindrical rods workpieces
Friction work create weld and can believe that is calculated for cylindrical workpieces from math:
Work:
(1)
Moment of force ''M'' general formula:
(2)
The force F will be the frictional force ''T (F=T)'' so substituting for the formula (2):
(3)
The friction force ''T'' will be the pressure ''F'' times by the friction coefficient µ:
(4)
So moment of force ''M'':
(5)
The alpha angle that each point will move with the axis of rotating cylindrical workpieces will be:
(6)
So friction work:
(7)
verification_needed''.html" ;"title="wikipedia:Verifiability">verification needed''">wikipedia:Verifiability">verification needed''/sup>
For variable value μ over friction time:
(8)
This requires verification but from equation it appears that turnover and force (or pressure
Pressure (symbol: ''p'' or ''P'') is the force applied perpendicular to the surface of an object per unit area over which that force is distributed. Gauge pressure (also spelled ''gage'' pressure)The preferred spelling varies by country and e ...
no surface ) is linear to friction work (W) so for example if pressure increase 2 times then friction work also increase 2 times, if turnover increase 2 times then friction work also increase 2 times and referring to rules conservation of energy
In physics and chemistry, the law of conservation of energy states that the total energy of an isolated system remains constant; it is said to be ''conserved'' over time. This law, first proposed and tested by Émilie du Châtelet, means th ...
this can heat 2 times more the material to the same temperature or the temperature may increase 2 times. However pressure has the same effect over the entire surface but rotation have more impact away from the axis of rotation because it is a rotary motion. Referring to thermal conductivity the friction time affects to the flash size when shorter time was used then friction work is more concentrated in a smaller area.
or variable values μ, n, F over friction time:
(9)
* t s.html"_;"title="Second.html"_;"title="nowiki/>Second">s">Second.html"_;"title="nowiki/>Second">s_time_of_friction_(when_piece_rotary),
*μ_-_ s.html"_;"title="Second.html"_;"title="nowiki/>Second">s">Second.html"_;"title="nowiki/>Second">s_time_of_friction_(when_piece_rotary),
*μ_-_coefficient_of_friction">Second">s.html"_;"title="Second.html"_;"title="nowiki/>Second">s">Second.html"_;"title="nowiki/>Second">s_time_of_friction_(when_piece_rotary),
*μ_-_ s.html"_;"title="Second.html"_;"title="nowiki/>Second">s">Second.html"_;"title="nowiki/>Second">s_time_of_friction_(when_piece_rotary),
*μ_-_coefficient_of_friction">Second">s.html"_;"title="Second.html"_;"title="nowiki/>Second">s">Second.html"_;"title="nowiki/>Second">s_time_of_friction_(when_piece_rotary),
*μ_-_coefficient_of_friction,
*_Force">F_[Newton_(unit).html" ;"title="coefficient_of_friction,
*_Force.html" ;"title="coefficient_of_friction.html" ;"title="Second">s.html" ;"title="Second.html" ;"title="nowiki/>Second">s">Second.html" ;"title="nowiki/>Second">s time of friction (when piece rotary),
*μ - coefficient of friction">Second">s.html" ;"title="Second.html" ;"title="nowiki/>Second">s">Second.html" ;"title="nowiki/>Second">s time of friction (when piece rotary),
*μ - coefficient of friction,
* Force">F [Newton (unit)">N]- pressure force,
* Radius, r [ m]- radius of workpiece,
* n [1/s] - turnover per second,
* Work (physics), W [Joule, J] - friction work.
Therefore, the calculation in this way is not reliable in real is complicated. An example article considering the variable depends on the temperature coefficient of friction steel - aluminum Al60611 - Alumina is described by authors from Malaysia in for exampl
this paper "Evaluation of Properties and FEM Model of the Friction Welded Mild Steel-Al6061-Alumina
and based on this position someone created no step by step but whatever a
instructional simulation video
in abaqus
Abaqus FEA (formerly ABAQUS) is a software suite for finite element analysis and computer-aided engineering, originally released in 1978. The name and logo of this software are based on the abacus calculation tool.
The Abaqus product suite consis ...
software and i
this paper
is possible to find the selection of the mesh type in the simulation described by the authors and there are some instructions such as use the Johnson-Cook material model choice, and not only, there is dissipation coefficient value, friction welding condition, the article included too the physical formulas related to rotary friction welding described by the authors such as: heat transfer equation and convection in rods, equations related to deformation processes. Article included information on the parameters of authors research, but it is not a step by step and simple instruction such as als
the video
and good add that it is not the only one position in literature. The conclusion include information that: ''"Even though the FE model proposed in this study cannot replace a more accurate analysis, it does provide guidance in weld parameter development and enhances understanding of the friction welding process, thus reducing costly and time consuming experimental approaches."''
The coefficient of friction changes with temperature and there are a number of factors internal friction (viscosity
The viscosity of a fluid is a measure of its resistance to deformation at a given rate. For liquids, it corresponds to the informal concept of "thickness": for example, syrup has a higher viscosity than water.
Viscosity quantifies the inte ...
- e.g. Dynamic viscosity according to Carreau's fluid law), forge, properties of the material during welding are variable, also there is plastic deformation.
Carreau's fluid law:
Generalized Newtonian fluid A generalized Newtonian fluid is an idealized fluid for which the shear stress is a function of shear rate at the particular time, but not dependent upon the history of deformation. Although this type of fluid is non-Newtonian (i.e. non-linear) in n ...
where viscosity, , depends upon the shear rate
In physics, shear rate is the rate at which a progressive shearing deformation is applied to some material.
Simple shear
The shear rate for a fluid flowing between two parallel plates, one moving at a constant speed and the other one stationary ...
, , by the following equation:
(10)
Where:
* , , and are material coefficients.
* = viscosity at zero shear rate (Pa.s)
* = viscosity at infinite shear rate (Pa.s)
* = relaxation time (s)
* = power index
Modelling of the frictional heat generated within the RFW process can be realized as a function of conducted frictional work and its dissipation coefficient, incremental frictional work of a node 𝑖 on the contacting surface can be described as a function of its axial distance from the rotation centre, current frictional shear stress
Shear stress, often denoted by (Greek: tau), is the component of stress coplanar with a material cross section. It arises from the shear force, the component of force vector parallel to the material cross section. ''Normal stress'', on the ot ...
, rotational speed and incremental time. The dissipation coefficient 𝛽FR is often set to 0.9 meaning that 90% of frictional work is dissipated into heat.
(11) 𝑑𝑞FR(𝑖) = 𝛽FR ∙ 𝑑𝑊FR(𝑖) = 𝛽FR ∙ 𝜏𝑅(𝑖) ∙ 𝜔 ∙ 𝑟𝑖 ∙ 𝑑𝑡 on contacting surface of node 𝑖
*𝛽FR - dissipation coefficient,
* 𝑊FR - frictional work,
* 𝑟𝑖 - distance from the rotation centre,
* dt - time increment,
* 𝜏𝑅(𝑖) - current frictional shear stress,
* 𝜔 - rotational speed.
Friction work can also calculate from power
Power most often refers to:
* Power (physics), meaning "rate of doing work"
** Engine power, the power put out by an engine
** Electric power
* Power (social and political), the ability to influence people or events
** Abusive power
Power may a ...
of used for welding and friction time (will not be greater than the friction time multiply to the power of the welder - engine of the welder) referring to rules conservation of energy
In physics and chemistry, the law of conservation of energy states that the total energy of an isolated system remains constant; it is said to be ''conserved'' over time. This law, first proposed and tested by Émilie du Châtelet, means th ...
. This calculation looks the simplest.
(12) ''E'' = Px ''t'' or for not constant power
* E - energy,
* P - power,
* t - power runtime.
However, in this case, energy can be also stored in the flywheel
A flywheel is a mechanical device which uses the conservation of angular momentum to store rotational energy; a form of kinetic energy proportional to the product of its moment of inertia and the square of its rotational speed. In particular, ass ...
if is used depending on the welder construction.
General flywheel energy formula:
(13)
where:
* is the stored kinetic energy
In physics, the kinetic energy of an object is the energy that it possesses due to its motion.
It is defined as the work needed to accelerate a body of a given mass from rest to its stated velocity. Having gained this energy during its accele ...
,
* ω is the angular velocity
In physics, angular velocity or rotational velocity ( or ), also known as angular frequency vector,(UP1) is a pseudovector representation of how fast the angular position or orientation of an object changes with time (i.e. how quickly an objec ...
, and
* is the moment of inertia
The moment of inertia, otherwise known as the mass moment of inertia, angular mass, second moment of mass, or most accurately, rotational inertia, of a rigid body is a quantity that determines the torque needed for a desired angular acceler ...
of the flywheel about its axis of symmetry.
Sample calculations not by computer simulation also exist in the literature for example related to power input and temperature distribution can be found in the script from 1974:
K. K. Wang and Wen Lin from Cornell University
Cornell University is a private statutory land-grant research university based in Ithaca, New York. It is a member of the Ivy League. Founded in 1865 by Ezra Cornell and Andrew Dickson White, Cornell was founded with the intention to teach an ...
in
Flywheel friction welding research
manually calculates welding process and even at this time the weld structure was analysed.
However, generally: The calculations can be complicated.
Weld Zone Descriprion
Weld photo gallery
Heat and mechanical affected zones
Friction work is converted into rise of temperature in the welding zone area, and as a result of this the weld structure is changed. In typical rotary friction welding process rise of temperature at the beginning of process should be more extensively away from the axis of rotation because points away axis have greater linear velocity and in time of weld the temperature disperses according to thermal conductivity
The thermal conductivity of a material is a measure of its ability to conduct heat. It is commonly denoted by k, \lambda, or \kappa.
Heat transfer occurs at a lower rate in materials of low thermal conductivity than in materials of high thermal ...
welded parts.
''"Technically the WCZ and the TMAZ are both "thermo-mechanically affected zones" but due to the vastly different microstructures they possess they are often considered separately. The WCZ experiences significant dynamic recrystallisation (DRX), the TMAZ does not. The material in HAZ is not deformed mechanically but is affected by the heat. The region from one TMAZ/HAZ boundary to the other is often referred to as the "TMAZ thickness" or the plastically affected zone (PAZ). For the remainder of this article this region will be referred to as the PAZ."''
Zones:
* WCZ– weld center zone,
* HAZ – heat affected zone
In fusion welding, the heat-affected zone (HAZ) is the area of base material, either a metal or a thermoplastic, which is not melted but has had its microstructure and properties altered by welding or heat intensive cutting operations. The heat ...
,
* TMAZ – Thermo-Mechanically Affected Zone,
* BM – base material, parent material,
* Flash.
Furthermore, in the literature, there is also a subdivided according to the type of grain.
Similar terms exist in welding
Welding is a fabrication (metal), fabrication process that joins materials, usually metals or thermoplastics, by using high heat to melt the parts together and allowing them to cool, causing Fusion welding, fusion. Welding is distinct from lower ...
.
During typical welding initially, the outer region heats up more, due to the higher linear velocity
Velocity is the directional speed of an object in motion as an indication of its rate of change in position as observed from a particular frame of reference and as measured by a particular standard of time (e.g. northbound). Velocity is a ...
.
Next, the heat spreads, and the material is pushed outside, thus creating a flash which can be cut off on the welding machine.
Heat flow, heat flux in rods
It can create a hypothesis
A hypothesis (plural hypotheses) is a proposed explanation for a phenomenon. For a hypothesis to be a scientific hypothesis, the scientific method requires that one can test it. Scientists generally base scientific hypotheses on previous obse ...
that heat flows in welding time like in a cylindrical rod it makes possible to suppose to calculate a temperature in individual places and times from the knowing of the issues of heat flow
Heat transfer is a discipline of thermal engineering that concerns the generation, use, conversion, and exchange of thermal energy (heat) between physical systems. Heat transfer is classified into various mechanisms, such as thermal conduction, ...
and heat flux
Heat flux or thermal flux, sometimes also referred to as ''heat flux density'', heat-flow density or ''heat flow rate intensity'' is a flow of energy per unit area per unit time. In SI its units are watts per square metre (W/m2). It has both a ...
in rods for example, temperature can be read by using thermocouple
A thermocouple, also known as a "thermoelectrical thermometer", is an electrical device consisting of two dissimilar electrical conductors forming an electrical junction. A thermocouple produces a temperature-dependent voltage as a result of the ...
s and compare with computer simulation.
File:Heat flow rod for RFW variant 2.jpg, Heat flow in Rod, and variant 1 placement of thermocouple
A thermocouple, also known as a "thermoelectrical thermometer", is an electrical device consisting of two dissimilar electrical conductors forming an electrical junction. A thermocouple produces a temperature-dependent voltage as a result of the ...
.
File:Heat flow in Rod, and variant 1 placement of thermocouples..jpg, Heat flow in Rod, and variant 2 placement of thermocouple
A thermocouple, also known as a "thermoelectrical thermometer", is an electrical device consisting of two dissimilar electrical conductors forming an electrical junction. A thermocouple produces a temperature-dependent voltage as a result of the ...
s.
Weld measuring system
To provide knowledge about the process, monitoring systems are often used and this are carried out in several ways which affects the accuracy and the list of measured parameters.
The list of measured and calculated parameters can looks like this:
* axial force and pressure
Pressure (symbol: ''p'' or ''P'') is the force applied perpendicular to the surface of an object per unit area over which that force is distributed. Gauge pressure (also spelled ''gage'' pressure)The preferred spelling varies by country and e ...
,
* angular - rotation speed
Rotational frequency (also known as rotational speed or rate of rotation) of an object rotating around an axis is the frequency of rotation of the object. Its unit is revolution per minute (rpm), cycle per second (cps), etc.
The symbol for ...
,
* spindle centre,
* velocity
Velocity is the directional speed of an object in motion as an indication of its rate of change in position as observed from a particular frame of reference and as measured by a particular standard of time (e.g. northbound). Velocity is a ...
,
* vibration
Vibration is a mechanical phenomenon whereby oscillations occur about an equilibrium point. The word comes from Latin ''vibrationem'' ("shaking, brandishing"). The oscillations may be periodic function, periodic, such as the motion of a pendulum ...
,
* length (burn off rate),
* temperature
Temperature is a physical quantity that expresses quantitatively the perceptions of hotness and coldness. Temperature is measured with a thermometer.
Thermometers are calibrated in various temperature scales that historically have relied o ...
.
Temperature measuring systems
Examples of weld measurements. In the literature, can be found measurements of the thermal weld area with thermocouple
A thermocouple, also known as a "thermoelectrical thermometer", is an electrical device consisting of two dissimilar electrical conductors forming an electrical junction. A thermocouple produces a temperature-dependent voltage as a result of the ...
s and not only the non-contact thermographic
Infrared thermography (IRT), thermal video and/or thermal imaging, is a process where a thermal camera captures and creates an image of an object by using infrared radiation emitted from the object in a process, which are examples of infrared ...
method is also used.
However, it also depends on the specific case for a very small area of the weld and HAZ there are cans by difficulties in thermal measuring in real time it can be calculated later after friction time there is heat flow.
Sample source code for temperature measurement made on arduino, this is far away from the topic, however there are missing full open friction welding codes. Exists the free open source software for simulation ( List of finite element software) but there is no welding open codes and detailed instructions to this software.
Research, temperature, parameters in the rotary friction welding process
Quality requirements of welded joints depend on the form of application, e.g. in the space or fly industry weld errors are not allowed. Science try to gets good quality welds, also some people have been interested in many years in welding knowledge, so there are many scientific articles describing the methods of joining. They are performed weld tests which give knowledge about mechanical properties
A materials property is an intensive property of a material, i.e., a physical property that does not depend on the amount of the material. These quantitative properties may be used as a metric by which the benefits of one material versus another ca ...
of material in welded zone e.g. hardness tests
In materials science, hardness (antonym: softness) is a measure of the resistance to localized plastic deformation induced by either mechanical indentation or abrasion. In general, different materials differ in their hardness; for example hard ...
, and tensile tests are performed. Based on the tensile tests the stretch curve are created which can give directly knowledge about ultimate tensile strength
Ultimate tensile strength (UTS), often shortened to tensile strength (TS), ultimate strength, or F_\text within equations, is the maximum stress that a material can withstand while being stretched or pulled before breaking. In brittle materials t ...
, breaking strength
Fracture is the separation of an object or material into two or more pieces under the action of stress. The fracture of a solid usually occurs due to the development of certain displacement discontinuity surfaces within the solid. If a displa ...
, maximum elongation and reduction in area and from these measurements the Young's modulus
Young's modulus E, the Young modulus, or the modulus of elasticity in tension or compression (i.e., negative tension), is a mechanical property that measures the tensile or compressive stiffness of a solid material when the force is applied leng ...
, Poisson's ratio
In materials science and solid mechanics, Poisson's ratio \nu ( nu) is a measure of the Poisson effect, the deformation (expansion or contraction) of a material in directions perpendicular to the specific direction of loading. The value of Pois ...
, yield strength
In materials science and engineering, the yield point is the point on a stress-strain curve that indicates the limit of elastic behavior and the beginning of plastic behavior. Below the yield point, a material will deform elastically and wi ...
, and strain-hardening
In materials science, work hardening, also known as strain hardening, is the strengthening of a metal or polymer by plastic deformation. Work hardening may be desirable, undesirable, or inconsequential, depending on the context.
This strengt ...
characteristics is created.
Where, the articles often contain only data related to tensile tests such as:
* Yield Strength
In materials science and engineering, the yield point is the point on a stress-strain curve that indicates the limit of elastic behavior and the beginning of plastic behavior. Below the yield point, a material will deform elastically and wi ...
in MPa
MPA or mPa may refer to:
Academia
Academic degrees
* Master of Performing Arts
* Master of Professional Accountancy
* Master of Public Administration
* Master of Public Affairs
Schools
* Mesa Preparatory Academy
* Morgan Park Academy
* Mound ...
* Ultimate Tensile Strength
Ultimate tensile strength (UTS), often shortened to tensile strength (TS), ultimate strength, or F_\text within equations, is the maximum stress that a material can withstand while being stretched or pulled before breaking. In brittle materials t ...
in MPa
MPA or mPa may refer to:
Academia
Academic degrees
* Master of Performing Arts
* Master of Professional Accountancy
* Master of Public Administration
* Master of Public Affairs
Schools
* Mesa Preparatory Academy
* Morgan Park Academy
* Mound ...
* Elongation in % percentage
In mathematics, a percentage (from la, per centum, "by a hundred") is a number or ratio expressed as a fraction of 100. It is often denoted using the percent sign, "%", although the abbreviations "pct.", "pct" and sometimes "pc" are also us ...
Where the units of SI are: K, kg, N, m, s and then Pa and this knowledge about this is needed for introducing data, material properties and not do errors in simulation programs.
Research articles also often contain information about:
* chemical composition of connected components
and inclusion process parameters is obvious such as:
* Friction Pressure (MPa)
* Friction Time (s)
* Welding Speed (rpm)
* Upset Pressure (MPa)
* Upset Time (s)
Is also possible to find descriptions in research literature about: mechanical properties
A materials property is an intensive property of a material, i.e., a physical property that does not depend on the amount of the material. These quantitative properties may be used as a metric by which the benefits of one material versus another ca ...
, microstructure
Microstructure is the very small scale structure of a material, defined as the structure of a prepared surface of material as revealed by an optical microscope above 25× magnification. The microstructure of a material (such as metals, polymers ...
, corrosion
Corrosion is a natural process that converts a refined metal into a more chemically stable oxide. It is the gradual deterioration of materials (usually a metal) by chemical or electrochemical reaction with their environment. Corrosion engine ...
and wear resistance
Wear is the damaging, gradual removal or deformation of material at solid surfaces. Causes of wear can be mechanical (e.g., erosion) or chemical (e.g., corrosion). The study of wear and related processes is referred to as tribology.
Wear in m ...
, and even cytotoxicity
Cytotoxicity is the quality of being toxic to cells. Examples of toxic agents are an immune cell or some types of venom, e.g. from the puff adder (''Bitis arietans'') or brown recluse spider (''Loxosceles reclusa'').
Cell physiology
Treating cells ...
welded material.
There are several methods to determine the quality of a weld and for example the weld microstructure
Microstructure is the very small scale structure of a material, defined as the structure of a prepared surface of material as revealed by an optical microscope above 25× magnification. The microstructure of a material (such as metals, polymers ...
is examined by optical microscopy
Optics is the branch of physics that studies the behaviour and properties of light, including its interactions with matter and the construction of instruments that use or detect it. Optics usually describes the behaviour of visible, ultraviole ...
and scanning electron microscopy.
The computer finite element method
The finite element method (FEM) is a popular method for numerically solving differential equations arising in engineering and mathematical modeling. Typical problem areas of interest include the traditional fields of structural analysis, heat ...
(FEM) is used to predict the shape of the flash and interface, not only for rotary friction welding (RFW), but also for friction stir welding
Friction stir welding (FSW) is a solid-state joining process that uses a non-consumable tool to join two facing workpieces without melting the workpiece material. Heat is generated by friction between the rotating tool and the workpiece material ...
(FSW), linear friction welding (LFW), FRIEX.
In addition to the weld testing, the weld head affected zones are described. Knowledge of the maximum temperatures in the welding process make it possible to define the area structural changes. Process are analisis e.g. temperature measurements are also carried out for scientific purposes research
Research is "creativity, creative and systematic work undertaken to increase the stock of knowledge". It involves the collection, organization and analysis of evidence to increase understanding of a topic, characterized by a particular att ...
materials, journals, by use contact thermocouple
A thermocouple, also known as a "thermoelectrical thermometer", is an electrical device consisting of two dissimilar electrical conductors forming an electrical junction. A thermocouple produces a temperature-dependent voltage as a result of the ...
s or sometimes no contact thermography
Infrared thermography (IRT), thermal video and/or thermal imaging, is a process where a Thermographic camera, thermal camera captures and creates an image of an object by using infrared radiation emitted from the object in a process, which are ...
methods. For example, an ultra fine grain
A grain is a small, hard, dry fruit (caryopsis) – with or without an attached hull layer – harvested for human or animal consumption. A grain crop is a grain-producing plant. The two main types of commercial grain crops are cereals and legum ...
structure of alloy or metal which is obtained by techniques such as severe plastic deformation
Severe plastic deformation (SPD) is a generic term describing a group of metalworking techniques involving very large strains typically involving a complex stress state or high shear, resulting in a high defect density and equiaxed "ultrafine" gr ...
or Powder metallurgy
Powder metallurgy (PM) is a term covering a wide range of ways in which materials or components are made from metal powders. PM processes can reduce or eliminate the need for subtractive processes in manufacturing, lowering material losses and ...
is desirable, and not changed by the high temperature, a large heat affected zone
In fusion welding, the heat-affected zone (HAZ) is the area of base material, either a metal or a thermoplastic, which is not melted but has had its microstructure and properties altered by welding or heat intensive cutting operations. The heat ...
is unnecessary. Temperature may reduce material properties because dynamic recrystallization
Dynamic recrystallization (DRX) is a type of recrystallization process, found within the fields of metallurgy and geology. In dynamic recrystallization, as opposed to static recrystallization, the nucleation and growth of new grains occurs during ...
will occur, there maybe changes in grain size and phase transformations structures of welded materials. In steel between austenite
Austenite, also known as gamma-phase iron (γ-Fe), is a metallic, non-magnetic allotrope of iron or a solid solution of iron with an alloying element. In plain-carbon steel, austenite exists above the critical eutectoid temperature of 1000 K ...
, ferrite, pearlite
Pearlite is a two-phased, lamellar (or layered) structure composed of alternating layers of ferrite (87.5 wt%) and cementite (12.5 wt%) that occurs in some steels and cast irons. During slow cooling of an iron-carbon alloy, pearlite forms ...
, bainite
Bainite is a plate-like microstructure that forms in steels at temperatures of 125–550 °C (depending on alloy content). First described by E. S. Davenport and Edgar Bain, it is one of the products that may form when austenite (the face- ...
, cementite
Cementite (or iron carbide) is a compound of iron and carbon, more precisely an intermediate transition metal carbide with the formula Fe3C. By weight, it is 6.67% carbon and 93.3% iron. It has an orthorhombic crystal structure. It is a hard, brit ...
, martensite
Martensite is a very hard form of steel crystalline structure. It is named after German metallurgist Adolf Martens. By analogy the term can also refer to any crystal structure that is formed by diffusionless transformation.
Properties
Mart ...
.
Various parameters of welding are tested. The setting of the completely different parameters can obtain different weld for example the structure changes will not be the same width. It is possible to obtain a smaller heat-affected zone
In fusion welding, the heat-affected zone (HAZ) is the area of base material, either a metal or a thermoplastic, which is not melted but has had its microstructure and properties altered by welding or heat intensive cutting operations. The heat ...
(HAZ) and a plastically affected zone (PAZ). The width of the weld is smaller. The results are for example not the same in welds made for the European Space Agency
, owners =
, headquarters = Paris, Île-de-France, France
, coordinates =
, spaceport = Guiana Space Centre
, seal = File:ESA emblem seal.png
, seal_size = 130px
, image = Views in the Main Control Room (1205 ...
with a high turnover ω = 14000 rpm o
another example
from Warsaw technical university
The Warsaw University of Technology ( pl, Politechnika Warszawska, lit=Varsovian Polytechnic) is one of the leading institutes of technology in Poland and one of the largest in Central Europe. It employs 2,453 teaching faculty, with 357 professor ...
12000 rpm and no typical very short friction time only 60 millisecond
A millisecond (from '' milli-'' and second; symbol: ms) is a unit of time in the International System of Units (SI) equal to one thousandth (0.001 or 10−3 or 1/1000) of a second and to 1000 microseconds.
A unit of 10 milliseconds may be called ...
s instead of using an standard parameters, in addition, in this case, ultra fine grain alloy was welded, but for this example the welded rod workpiece was only 6mm in diameter so it is small rod friction welding another close to this examples with short friction time only e.g. 40 ms also exist in literature but also for small diameter. The rotations in the research literature for small diameters can be more as standard even e.g. 25000 rpm. Unfortunately the diameter of the workpiece can be a limitation to the use of high speeds of rotation.
The key points to understand is that: Fine grain of the welded metal material according to Hall-Petch relation should have better strength and for the description of one technique for obtaining this material Percy Williams Bridgman
Percy Williams Bridgman (April 21, 1882 – August 20, 1961) was an American physicist who received the 1946 Nobel Prize in Physics for his work on the physics of high pressures. He also wrote extensively on the scientific method and on other as ...
won the Nobel Prize in Physics
)
, image = Nobel Prize.png
, alt = A golden medallion with an embossed image of a bearded man facing left in profile. To the left of the man is the text "ALFR•" then "NOBEL", and on the right, the text (smaller) "NAT•" then " ...
in 1946 referring to the achievements related to High Pressure Torsion (HPT),. However, by High Pressure Torsion is obtained only thin film thickness material.
There is also research into the introduction of interlayers. Even though dissimilar material joining is often more difficult the introduction for example nickel
Nickel is a chemical element with symbol Ni and atomic number 28. It is a silvery-white lustrous metal with a slight golden tinge. Nickel is a hard and ductile transition metal. Pure nickel is chemically reactive but large pieces are slow to ...
interlayer by an experimental electrodeposition deposition technique to increase the connection quality has been investigated by the Indian Institute of Metals
Indian Institute of Metals (IIM) was formed in Kolkata in 1946 under the leadership of Dr. Dara P. Antia, who was then Chief Metallurgist of Indian Aluminum Co. The IIM is over 60 years old premier professional Metallurgical Institute set up to ...
, however in this case nickel interlayer thickness was of 70 m (micrometre ) and only small rods of 12mm diameter were welded.
Some scientists describe material research. Group of known materials is large includes: Ni nickel based superalloy
A superalloy, or high-performance alloy, is an alloy with the ability to operate at a high fraction of its melting point. Several key characteristics of a superalloy are excellent mechanical strength, resistance to thermal creep deformation, g ...
s such as Inconel
Inconel is a registered trademark of Special Metals Corporation for a family of austenitic nickel-chromium-based superalloys.
Inconel alloys are oxidation-corrosion-resistant materials well suited for service in extreme environments subjected t ...
, ultra-fine grain materials such as ultra-fine grain aluminum, low carbon steel e.g. Ultra Low Carbon Bainitic Steel (ULCBS). Friction welding is used for connection many materials including superalloy
A superalloy, or high-performance alloy, is an alloy with the ability to operate at a high fraction of its melting point. Several key characteristics of a superalloy are excellent mechanical strength, resistance to thermal creep deformation, g ...
s for example nickel
Nickel is a chemical element with symbol Ni and atomic number 28. It is a silvery-white lustrous metal with a slight golden tinge. Nickel is a hard and ductile transition metal. Pure nickel is chemically reactive but large pieces are slow to ...
-based Inconel
Inconel is a registered trademark of Special Metals Corporation for a family of austenitic nickel-chromium-based superalloys.
Inconel alloys are oxidation-corrosion-resistant materials well suited for service in extreme environments subjected t ...
, scientists describe connecting various materials and on the internet is possible finding articles about this and same part of the research relates to joining superalloy
A superalloy, or high-performance alloy, is an alloy with the ability to operate at a high fraction of its melting point. Several key characteristics of a superalloy are excellent mechanical strength, resistance to thermal creep deformation, g ...
s materials or materials with improved properties. Nickel based superalloys exhibit excellent high temperature strength, high temperature corrosion and oxidation resistance and creep resistance. However, referring to this research good add that nickel is not the most common and cheapest material: Prices list of chemical elements.
Parameters
* Turnover: Typically turnover is selected depending on the type of material and dimensions of welded parts have different values: 400 - 1450 rpm, sometimes max 10000 rpm. Not typically, in research literature turnover is to 25000 rmp.
* Friction time: typically 1 - to a several dozen seconds. Not typically, in research literature friction time can be in tends of millisecond
A millisecond (from '' milli-'' and second; symbol: ms) is a unit of time in the International System of Units (SI) equal to one thousandth (0.001 or 10−3 or 1/1000) of a second and to 1000 microseconds.
A unit of 10 milliseconds may be called ...
s, however when time is very short and parameters are not typical process can require a lot of preliminary preparation and testing to the positive result.
*Forge time: Up to a few seconds.
However, the parameters will be different as elements of different sizes can be welded. For example, can be produced ranging from the smallest component with a diameter of 3 mm to turbine
A turbine ( or ) (from the Greek , ''tyrbē'', or Latin ''turbo'', meaning vortex) is a rotary mechanical device that extracts energy from a fluid flow and converts it into useful work. The work produced by a turbine can be used for generating e ...
components with a diameter in excess of 400 mm.
By combining methods of connecting long elementss perhaps future science may study the friction welding of rails for example for the high speeds railway industry and use the preheat Low force linear friction welding or modified Linear friction welding (LFW) method and vibrating insert (just like the rotating insert in FRIEX method) for do this if the machine are developed and also good add that most of attention are directed to safety of travelers, user safety should be preserved at the first place.
Preliminary research involving similar welds and geometry has shown improved tensile strength and increased performance in the fatigue tests.
Controversies in research
# As of August 2022, there are no step-by-step reviewed instructions on how to simulate the temperature of weldet components. There are no shared source files for programs where simulation of welding is possible. On the other hand, some of the knowledge is difficult for example in 08.2022 an article: Hamed, Maien Mohamed Osman the
Numerical simulation of friction welding processes: An arbitrary Lagrangian-Eulerian approach
was shared on google scholar but it is difficult to understand.
# Problem with open article reviews or revies no exist.
# Correct use of grants, and repeating of knowledge for example the structure of a lot of articles is similar and sometimes generally only the next material is welded so there is nothing new but some of research is granted.
# It is only friction welding, generally nothing difficult, on the other hand there are many complicated descriptions, but the practical result of this articles is missing: The expectation is to create something new, unknown so far.
# Correct use of grants, time of articles, who is first, announcing about the desire to create something new an innovative device by the university but this is not done:
#* Poland
Google scholar finds 246 articles in response to the "friction welding" phrase in 8.2022, this is only part of all available research, and for some of them financial grants are given. However, for example in 201
The Institute of Electronic Materials Technology in Poland
published
he article in Polish language about welding Al/Al2O3 Composites
after then two years later the Warsaw University of Technology
The Warsaw University of Technology ( pl, Politechnika Warszawska, lit=Varsovian Polytechnic) is one of the leading institutes of technology in Poland and one of the largest in Central Europe. It employs 2,453 teaching faculty, with 357 professor ...
publishes an article in Polish language about friction welding ultrafine grained 316L steel in 2018, although the materials was different, but the process parameters suggest that the welding machine is the same, so in this case The Institute of Electronic Materials Technology was published the data first, and summarizing in this case: in 2018 only the new material, which was steel, was welded and tested, the machine was not new but for this
grant was obtained
(843 920 PLN = ~$177476 USD). It has not been written into the articles since the two institutes had a machine and since studies with short friction times were carried out.
Students were informed about the willingness to create by the university a new innovative friction welder, but to 08.2022 there is no information about this, there are new research articles, but the device is still old.
Low Force Friction Welding
A improved modification of the standard friction welding is Low Force Friction Welding, hybrid technology developed by EWI and Manufacturing Technology Inc. (MTI), "''uses an external energy source to raise the interface temperature of the two parts being joined, thereby reducing the process forces required to make a solid-state weld compared to traditional friction welding''". The process applies to both linear and rotary friction welding.
Low force friction advantages:
* Little or no flash,
* Joining of components previously limited by friction welding,
* Reduced machine footprint,
* Reduced weld cycle time,
* Higher orientation precision,
* Part repeatability.
Following the informations from th
Manufacturing Technology blog and website
the technology is promising.
However, in 2021 the number of scientific articles for example on Google Scholar about Low force friction is smaller compared to description of the standard method about friction welding where an external energy source to raise the interface temperature is not used.
Construction of the welding machine
Depending on the construction, but a standard welding machine may include the following systems:
* Control system
A control system manages, commands, directs, or regulates the behavior of other devices or systems using control loops. It can range from a single home heating controller using a thermostat controlling a domestic boiler to large industrial c ...
* Motor
An engine or motor is a machine designed to convert one or more forms of energy into mechanical energy.
Available energy sources include potential energy (e.g. energy of the Earth's gravitational field as exploited in hydroelectric power gen ...
or motors in e.g. direct-drive welder
* Pneumatic
Pneumatics (from Greek ‘wind, breath’) is a branch of engineering that makes use of gas or pressurized air.
Pneumatic systems used in Industrial sector, industry are commonly powered by compressed air or compressed inert gases. A central ...
or hydraulic
Hydraulics (from Greek: Υδραυλική) is a technology and applied science using engineering, chemistry, and other sciences involving the mechanical properties and use of liquids. At a very basic level, hydraulics is the liquid counter ...
pressure system
* Handle
* Non rotating vice
A vice is a practice, behaviour, or habit generally considered immoral, sinful, criminal, rude, taboo, depraved, degrading, deviant or perverted in the associated society. In more minor usage, vice can refer to a fault, a negative character tra ...
* Clutch
A clutch is a mechanical device that engages and disengages power transmission, especially from a drive shaft to a driven shaft. In the simplest application, clutches connect and disconnect two rotating shafts (drive shafts or line shafts). ...
in direct-drive friction welder
* Spindle
Spindle may refer to:
Textiles and manufacturing
* Spindle (textiles), a straight spike to spin fibers into yarn
* Spindle (tool), a rotating axis of a machine tool
Biology
* Common spindle and other species of shrubs and trees in genus ''Euony ...
* Flywheel
A flywheel is a mechanical device which uses the conservation of angular momentum to store rotational energy; a form of kinetic energy proportional to the product of its moment of inertia and the square of its rotational speed. In particular, ass ...
in inertia friction welder
* Housing
* Measuring systems
Producers present solutions and welding machines can include:
* Measurement and control dimensional systems: Active Travel Control, burn off rate measurement,
* Automation solutions, Defined angle positioning, Component lifter, Automatic door operations, Weld data export, Ready for industrial solutions, Automatic temperature control of the headstock, Monitoring of the cooling unit, servo motor control,
* Have solutions for clean environment with no arcs, sparks, smoke or flames,
*Have ergonomic workspace, nice design,
*No special foundations or power supplies are required,
* Process control and documentation systems: All process data is documented numerically and graphically, have program management, Calculated parameters - Smart machine
* HMI touchscreen panels,
* Flash cut off device systems on the welder, flash removal and facing, chip conveyor,
* Completely integrated solution in the specific production workflow using state of the art 3D process simulation,
* Service assistance: Remote Service, Alarm conditions,
* Have certificates,
*Advanced Measurement systems,
* Ready for robot automation for handling components.
*Include innovative solutions: for example hybrid technology Low Force Friction Welding, and the system associated with this technology,
However, there is not one manufacturer on the market and no one welder machine model and in addition, not always the same material and diameters is welded and a good presentation, technology description, design, may or not may determine the best solutions. There are also exist advertising presentations related to welding.
Workpiece handles
The type of chuck depends on the technology used, their construction sometimes may be similar to a lathe
A lathe () is a machine tool that rotates a workpiece about an axis of rotation to perform various operations such as cutting, sanding, knurling, drilling, deformation, facing, and turning, with tools that are applied to the workpiece to c ...
and milling machine
Milling is the process of machining using rotary cutters to remove material by advancing a cutter into a workpiece. This may be done by varying direction on one or several axes, cutter head speed, and pressure. Milling covers a wide variety of d ...
.
Errors during welding
* Components not in the same line of symmetry, non ideal interaction between the workpieces
*problem with fixing items
* Incomplete welding
*Bad parameters reducing properties of welded components
Safety during friction welding
*Before starting the work, even if the short and basic safety regulations should be knowned.
*Compliance with occupational safety and health
Occupational safety and health (OSH), also commonly referred to as occupational health and safety (OHS), occupational health, or occupational safety, is a multidisciplinary field concerned with the safety, health, and welfare of people at wor ...
regulations
* Following the manufacturer's recommendations
* Set up the machine in a safe place: not blocking the entrance door, electric wires away from water, free movement of the users
* Recommended security systems for example: Emergency stop button, possibility of a quick stop of the machine
* Caution with hot and sharp things for example the hot welded components, chips if they are cut off on the welding machine
* Fresh air, for example do not smoke on the production hall near the machine.
* Covering moving components
The description of the security rules depends on the joining method and situation - access to fresh air, electrical ground, wearing protective clothing, protect the eyes is required.
Other techniques of friction welding
* Forge welding
Forge welding (FOW), also called fire welding, is a solid-state welding process that joins two pieces of metal by heating them to a high temperature and then hammering them together. It may also consist of heating and forcing the metals together ...
* Friction stir welding
Friction stir welding (FSW) is a solid-state joining process that uses a non-consumable tool to join two facing workpieces without melting the workpiece material. Heat is generated by friction between the rotating tool and the workpiece material ...
(FSW)
* Friction stir spot welding (FSSW)
* Linear friction welding (LFW)
* Research on friction welding of pipeline girth welds (FRIEX)
* Friction hydro pillar overlap processing (FHPPOW)
* Friction hydro pillar processing (FHHP)
Terms and definitions, name shortcuts
Welding
Welding is a fabrication (metal), fabrication process that joins materials, usually metals or thermoplastics, by using high heat to melt the parts together and allowing them to cool, causing Fusion welding, fusion. Welding is distinct from lower ...
vs joining - Definitions depend on the author. Welding in Cambridge English dictionary means: "the activity of joining metal parts together" in Collins dictionary "the activity of uniting metal or plastic by softening with heat and hammering, or by fusion", which means that welding is related to connect. Join or joining has a similar meaning that welding and can mean the same in English dictionary means "to connect or fasten things together" but joining otherwise has many meanings for example "If roads or rivers join, they meet at a particular point". Joining opposed to welding, is a general term and there are several methods available for joining metals, including riveting, soldering
Soldering (; ) is a process in which two or more items are joined by melting and putting a filler metal (solder) into the joint, the filler metal having a lower melting point than the adjoining metal. Unlike welding, soldering does not involv ...
, adhesive
Adhesive, also known as glue, cement, mucilage, or paste, is any non-metallic substance applied to one or both surfaces of two separate items that binds them together and resists their separation.
The use of adhesives offers certain advant ...
, brazing
Brazing is a metal-joining process in which two or more metal items are joined together by melting and flowing a filler metal into the joint, with the filler metal having a lower melting point than the adjoining metal.
Brazing differs from we ...
, coupling, fastening
A fastener (US English) or fastening (UK English) is a hardware device that mechanically joins or affixes two or more objects together. In general, fasteners are used to create non-permanent joints; that is, joints that can be removed or disman ...
, press fit. Welding is only one type of joining process.
Solid-state weld - connect below the melting point,
welder - welding machine, but also mean a person who welds metal.
weld - the place of connection where the materials are mixed.
weldability - a measure of the ease of making a weld without errors.
interlayer - an indirect component, indirect material.
To quote ISO ( the International Organization for Standardization, unfortunately the all ISO text is not free and open shared)
ISO 15620:2019(en) Welding — Friction welding of metallic materials
"axial force - force in axial direction between components to be welded,
burn-off length - loss of length during the friction phase,
burn-off rate - rate of shortening of the components during the friction welding process,
component - single item before welding,
component induced braking - reduction in rotational speed resulting from friction between the interfaces,
external braking - braking located externally reducing the rotational speed,
faying surface - surface of one component that is to be in contact with a surface of another component to form a joint,
forge force - force applied normal to the faying surfaces at the time when relative movement between the components is ceasing or has ceased,
forge burn-off length - amount by which the overall length of the components is reduced during the application of the forge force,
forge phase - interval time in the friction welding cycle between the start and finish of application of the forge force,
forge pressure - pressure (force per unit area) on the faying surfaces resulting from the axial forge force,
forge time - time for which the forge force is applied to the components,
friction force - force applied perpendicularly to the faying surfaces during the time that there is relative movement between the components,
friction phase - interval time in the friction welding cycle in which the heat necessary for making a weld is generated by relative motion and the friction forces between the components i.e. from contact of components to the start of deceleration,
friction pressure - pressure (force per unit area) on the faying surfaces resulting from the axial friction force,
friction time - time during which relative movement between the components takes place at rotational speed and under application of the friction forces,
interface - contact area developed between the faying surfaces after completion of the welding operation,
rotational speed - number of revolutions per minute of rotating component,
stick-out - distance a component sticks out from the fixture, or chuck in the direction of the mating component,
deceleration phase - interval in the friction welding cycle in which the relative motion of the components is decelerated to zero,
deceleration time - time required by the moving component to decelerate from friction speed to zero speed,
total length loss (upset) - loss of length that occurs as a result of friction welding, i.e. the sum of the burn-off length and the forge burn-off length,
total weld time - time elapsed between component contact and end of forging phase,
welding cycle - succession of operations carried out by the machine to make a weldment and return to the initial position, excluding component - handling operations,
weldment - two or more components joined by welding."
And more than that:
* RFW - Rotary friction welding,
* LFW - Linear friction welding,
* FSSW - Friction stir spot welding,
* FRIEX - Research on friction welding of pipeline girth welds,
* FHPPOW - Friction hydro pillar overlap processing,
* FHHP - Friction hydro pillar processing,
* LFFW - Low Force Friction Welding,
* FSW - Friction stir welding,
* BM - Base material,
* HAZ - Heat affected zone,
* PAZ - Plastically affected zone,
* DRX - Dynamic recrystallization,
* TMAZ - Thermo-Mechanically Affected Zone,
* UFG - Ultra fine grain,
* SPD - Serve plastic deformation,
* HPT - High Pressure Torsion,
* FEM - Finite element method,
* SEM - Scanning electron microscopy,
* ADC - Analog to digital converter.
See also
*Welding
Welding is a fabrication (metal), fabrication process that joins materials, usually metals or thermoplastics, by using high heat to melt the parts together and allowing them to cool, causing Fusion welding, fusion. Welding is distinct from lower ...
*Friction
Friction is the force resisting the relative motion of solid surfaces, fluid layers, and material elements sliding against each other. There are several types of friction:
*Dry friction is a force that opposes the relative lateral motion of t ...
*Friction welding
Friction welding (FRW) is a solid-state welding process that generates heat through mechanical friction between workpieces in relative motion to one another, with the addition of a lateral force called "upset" to plastically displace and fuse the m ...
*Friction stir welding
Friction stir welding (FSW) is a solid-state joining process that uses a non-consumable tool to join two facing workpieces without melting the workpiece material. Heat is generated by friction between the rotating tool and the workpiece material ...
*Temperature
Temperature is a physical quantity that expresses quantitatively the perceptions of hotness and coldness. Temperature is measured with a thermometer.
Thermometers are calibrated in various temperature scales that historically have relied o ...
*Heat-affected zone
In fusion welding, the heat-affected zone (HAZ) is the area of base material, either a metal or a thermoplastic, which is not melted but has had its microstructure and properties altered by welding or heat intensive cutting operations. The heat ...
*Dynamic recrystallization
Dynamic recrystallization (DRX) is a type of recrystallization process, found within the fields of metallurgy and geology. In dynamic recrystallization, as opposed to static recrystallization, the nucleation and growth of new grains occurs during ...
*Grain boundary strengthening
In materials science, grain-boundary strengthening (or Hall–Petch strengthening) is a method of strengthening materials by changing their average crystallite (grain) size. It is based on the observation that grain boundaries are insurmountabl ...
*Severe plastic deformation
Severe plastic deformation (SPD) is a generic term describing a group of metalworking techniques involving very large strains typically involving a complex stress state or high shear, resulting in a high defect density and equiaxed "ultrafine" gr ...
Curiosities
* Frictional welding (μ FSW) was also performed using a CNC machine
Numerical control (also computer numerical control, and commonly called CNC) is the automated control of machining tools (such as drills, lathes, mills, grinders, routers and 3D printers) by means of a computer. A CNC machine processes a ...
. which does not mean that it is safe and recommended for the milling machine.
* Scientists even describe measurements of acoustic emission Acoustic emission (AE) is the phenomenon of radiation of acoustic (elastic) waves in solids that occurs when a material undergoes irreversible changes in its internal structure, for example as a result of crack formation or plastic deformation due t ...
s during joining.
References
External links
Rotary Friction Welding at google scholar
- scientific search engine also to many articles about rotary friction welding.
Rotary Friction Welding at TWI
an
search-results at TWI
Rotary Friction Welding at KUKA
Modifications Rotary friction welding
Low Force Friction Welding
Other techniques
Friction stir welding at TWI
Simulation of the rotary welding process on YouTube
Rotary Friction Welding with movie 1
but the author did not select the rotation value; also mesh C3D10 is selected, but i
Evaluation of Properties and FEM Model of the Friction Welded Mild Steel-Al6061-Alumina
is written about mesh C3D8RT. No source files. Source requires verification.
Rotary Friction Welding with movie 2
but no source files and not fully understood so the source requires verification.
History of the rotary welding process in news paper (in Russian)
History the rotary welding process in news paper from 1958 (in Russian Техника - молодёжи 1958-02, страница 32, сварка трением)
Measuring system
* Nice described measuring system:''
Development of a novel monitoring system for the in-process characterisation of the machine and tooling effects in Inertia Friction Welding (IFW)
* High Performance Thermal camera example link: According to data from and in 2022, exampl
High Performance Flir thermal camera X8580 link and specification.
However it is not the only manufacturer, and high-performance devices are also generally expensive. Also, the parameters of the thermal camera not match to the classical not thermal camers, for example 1280 × 1024 it is only ~1,3 MPx and nowadays cell phone cameras can have this value several times higher.
Scientific movie about the rotary friction welding
NMIS-AFRC with Rolls-Royce on the rotary friction revolution
often scientific knowledge is available through universities, books, libraries, journals, but in this link is explained through the movie.
{{Metalworking navbox/weld
Welding