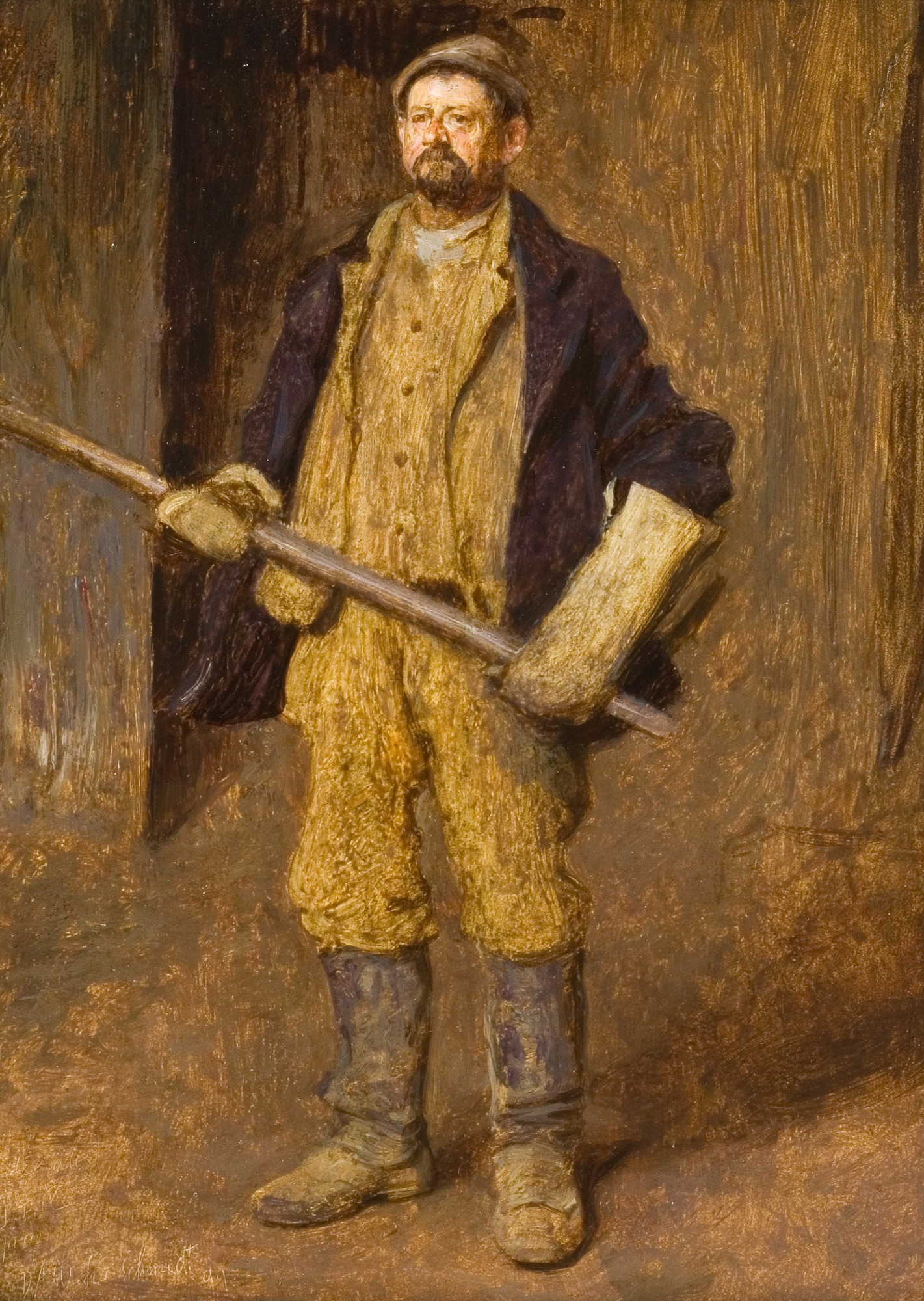
A foundry is a
factory
A factory, manufacturing plant or a production plant is an industrial facility, often a complex consisting of several buildings filled with machinery, where workers manufacture items or operate machines which process each item into another. T ...
that produces
metal
A metal (from Greek μέταλλον ''métallon'', "mine, quarry, metal") is a material that, when freshly prepared, polished, or fractured, shows a lustrous appearance, and conducts electricity and heat relatively well. Metals are typicall ...
casting
Casting is a manufacturing process in which a liquid material is usually poured into a mold, which contains a hollow cavity of the desired shape, and then allowed to solidify. The solidified part is also known as a ''casting'', which is ejected ...
s. Metals are cast into shapes by melting them into a liquid, pouring the metal into a mold, and removing the mold material after the metal has solidified as it cools. The most common metals processed are
aluminum
Aluminium (aluminum in American and Canadian English) is a chemical element with the symbol Al and atomic number 13. Aluminium has a density lower than those of other common metals, at approximately one third that of steel. It has ...
and
cast iron
Cast iron is a class of iron–carbon alloys with a carbon content more than 2%. Its usefulness derives from its relatively low melting temperature. The alloy constituents affect its color when fractured: white cast iron has carbide impuriti ...
. However, other metals, such as
bronze
Bronze is an alloy consisting primarily of copper, commonly with about 12–12.5% tin and often with the addition of other metals (including aluminium, manganese, nickel, or zinc) and sometimes non-metals, such as phosphorus, or metalloids such ...
,
brass
Brass is an alloy of copper (Cu) and zinc (Zn), in proportions which can be varied to achieve different mechanical, electrical, and chemical properties. It is a substitutional alloy: atoms of the two constituents may replace each other with ...
,
steel
Steel is an alloy made up of iron with added carbon to improve its strength and fracture resistance compared to other forms of iron. Many other elements may be present or added. Stainless steels that are corrosion- and oxidation-resistant ty ...
,
magnesium
Magnesium is a chemical element with the symbol Mg and atomic number 12. It is a shiny gray metal having a low density, low melting point and high chemical reactivity. Like the other alkaline earth metals (group 2 of the periodic ta ...
, and
zinc
Zinc is a chemical element with the symbol Zn and atomic number 30. Zinc is a slightly brittle metal at room temperature and has a shiny-greyish appearance when oxidation is removed. It is the first element in group 12 (IIB) of the periodi ...
, are also used to produce castings in foundries. In this process, parts of desired shapes and sizes can be formed.
Foundries are one of the largest contributors to the manufacturing recycling movement, melting and recasting millions of tons of scrap metal every year to create new durable goods. Moreover, many foundries use sand in their molding process. These foundries often use, recondition, and reuse sand, which is another form of recycling.
Process
In
metalworking
Metalworking is the process of shaping and reshaping metals to create useful objects, parts, assemblies, and large scale structures. As a term it covers a wide and diverse range of processes, skills, and tools for producing objects on every scale ...
,
casting
Casting is a manufacturing process in which a liquid material is usually poured into a mold, which contains a hollow cavity of the desired shape, and then allowed to solidify. The solidified part is also known as a ''casting'', which is ejected ...
involves pouring liquid metal into a
mold
A mold () or mould () is one of the structures certain fungus, fungi can form. The dust-like, colored appearance of molds is due to the formation of Spore#Fungi, spores containing Secondary metabolite#Fungal secondary metabolites, fungal seco ...
, which contains a hollow cavity of the desired shape, and then allowing it to cool and solidify. The solidified part is also known as a casting, which is ejected or broken out of the mold to complete the process. Casting is most often used for making complex shapes that would be difficult or uneconomical to make by other methods.
Melting

Melting is performed in a
furnace
A furnace is a structure in which heat is produced with the help of combustion.
Furnace may also refer to:
Appliances Buildings
* Furnace (central heating): a furnace , or a heater or boiler , used to generate heat for buildings
* Boiler, used t ...
. Virgin material, external scrap, internal scrap, and alloying elements are used to charge the furnace. Virgin material refers to commercially pure forms of the primary metal used to form a particular
alloy
An alloy is a mixture of chemical elements of which at least one is a metal. Unlike chemical compounds with metallic bases, an alloy will retain all the properties of a metal in the resulting material, such as electrical conductivity, ductility, ...
. Alloying elements are either pure forms of an alloying element, like electrolytic
nickel
Nickel is a chemical element with symbol Ni and atomic number 28. It is a silvery-white lustrous metal with a slight golden tinge. Nickel is a hard and ductile transition metal. Pure nickel is chemically reactive but large pieces are slow to ...
, or alloys of limited composition, such as
ferroalloy
Ferroalloy refers to various alloys of iron with a high proportion of one or more other elements such as manganese (Mn), aluminium (Al), or silicon (Si). They are used in the production of steels and alloys. The alloys impart distinctive qualitie ...
s or master alloys. External scrap is material from other forming processes such as
punching
Punching is a forming process that uses a punch press to force a tool, called a ''punch'', through the workpiece to create a hole via shearing. Punching is applicable to a wide variety of materials that come in sheet form, including sheet meta ...
,
forging
Forging is a manufacturing process involving the shaping of metal using localized compressive forces. The blows are delivered with a hammer (often a power hammer) or a die. Forging is often classified according to the temperature at which i ...
, or
machining
Machining is a process in which a material (often metal) is cut to a desired final shape and size by a controlled material-removal process. The processes that have this common theme are collectively called subtractive manufacturing, which utilizes ...
. Internal scrap consists of
gates
Gates is the plural of gate, a point of entry to a space which is enclosed by walls. It may also refer to:
People
* Gates (surname), various people with the last name
* Gates Brown (1939-2013), American Major League Baseball player
* Gates McFadde ...
,
risers, defective castings, and other extraneous metal oddments produced within the facility.
The process includes melting the charge, refining the melt, adjusting the melt chemistry and tapping into a transport vessel.
Refining
{{Unreferenced, date=December 2009
Refining (also perhaps called by the mathematical term affining) is the process of purification of a (1) substance or a (2) form. The term is usually used of a natural resource that is almost in a usable form, b ...
is done to remove harmful gases and elements from the molten metal to avoid casting defects. Material is added during the melting process to bring the final chemistry within a specific range specified by industry and/or internal standards. Certain
fluxes may be used to separate the metal from slag and/or dross and degassers are used to remove dissolved gas from metals that readily dissolve in gasses. During the tap, final chemistry adjustments are made.
Furnace
Several specialised furnaces are used to heat the metal. Furnaces are refractory-lined vessels that contain the material to be melted and provide the energy to melt it. Modern furnace types include
electric arc furnace
An electric arc furnace (EAF) is a furnace that heats material by means of an electric arc.
Industrial arc furnaces range in size from small units of approximately one-tonne capacity (used in foundries for producing cast iron products) up to ab ...
s (EAF),
induction furnace
An induction furnace is an electrical furnace in which the heat is applied by induction heating of metal.
Induction furnace capacities range from less than one kilogram to one hundred tons, and are used to melt iron and steel, copper, aluminum ...
s,
cupolas
In architecture, a cupola () is a relatively small, most often dome-like, tall structure on top of a building. Often used to provide a lookout or to admit light and air, it usually crowns a larger roof or dome.
The word derives, via Italian, from ...
,
reverberatory, and crucible furnaces. Furnace choice is dependent on the alloy system quantities produced. For ferrous materials EAFs, cupolas, and induction furnaces are commonly used. Reverberatory and crucible furnaces are common for producing aluminium, bronze, and brass castings.
Furnace design is a complex process, and the design can be optimized based on multiple factors. Furnaces in foundries can be any size, ranging from small ones used to melt precious metals to furnaces weighing several tons, designed to melt hundreds of pounds of scrap at one time. They are designed according to the type of metals that are to be melted. Furnaces must also be designed based on the fuel being used to produce the desired temperature. For low temperature melting point alloys, such as zinc or tin, melting furnaces may reach around . Electricity, propane, or natural gas are usually used to achieve these temperatures. For high melting point alloys such as steel or nickel-based alloys, the furnace must be designed for temperatures over . The fuel used to reach these high temperatures can be electricity (as employed in
electric arc furnace
An electric arc furnace (EAF) is a furnace that heats material by means of an electric arc.
Industrial arc furnaces range in size from small units of approximately one-tonne capacity (used in foundries for producing cast iron products) up to ab ...
s) or
coke.
The majority of foundries specialize in a particular metal and have furnaces dedicated to these metals. For example, an iron foundry (for cast iron) may use a
cupola
In architecture, a cupola () is a relatively small, most often dome-like, tall structure on top of a building. Often used to provide a lookout or to admit light and air, it usually crowns a larger roof or dome.
The word derives, via Italian, from ...
, induction furnace, or EAF, while a steel foundry will use an EAF or induction furnace.
Bronze
Bronze is an alloy consisting primarily of copper, commonly with about 12–12.5% tin and often with the addition of other metals (including aluminium, manganese, nickel, or zinc) and sometimes non-metals, such as phosphorus, or metalloids such ...
or
brass
Brass is an alloy of copper (Cu) and zinc (Zn), in proportions which can be varied to achieve different mechanical, electrical, and chemical properties. It is a substitutional alloy: atoms of the two constituents may replace each other with ...
foundries use crucible furnaces or induction furnaces. Most aluminium foundries use either electric resistance or gas heated
crucible
A crucible is a ceramic or metal container in which metals or other substances may be melted or subjected to very high temperatures. While crucibles were historically usually made from clay, they can be made from any material that withstands te ...
furnaces or reverberatory furnaces.
Degassing
Degassing is a process that may be required to reduce the amount of hydrogen present in a batch of molten metal. Gases can form in metal castings in one of two ways:
# by physical entrapment during the casting process or
# by chemical reaction in the cast material.
Hydrogen is a common contaminant for most cast metals. It forms as a result of material reactions or from water vapor or machine lubricants. If the hydrogen concentration in the melt is too high, the resulting casting will be porous; the hydrogen will exit the molten solution, leaving minuscule air pockets, as the metal cools and solidifies. Porosity often seriously deteriorates the mechanical properties of the metal.
An efficient way of removing hydrogen from the melt is to bubble a dry, insoluble gas through the melt by purging or agitation. When the bubbles go up in the melt, they catch the dissolved hydrogen and bring it to the surface. Chlorine, nitrogen, helium and argon are often used to degas non-ferrous metals. Carbon monoxide is typically used for iron and steel.
There are various types of equipment that can measure the presence of hydrogen. Alternatively, the presence of hydrogen can be measured by determining the density of a metal sample.
In cases where porosity still remains present after the degassing process,
porosity sealing
Porosity sealing is done through the process of vacuum impregnation. Vacuum impregnation is a preferred OEM process that seals porosity and leak paths in metal castings, sintered metal parts and electrical castings that form during the casting or ...
can be accomplished through a process called
metal impregnating
Porosity sealing is done through the process of vacuum impregnation. Vacuum impregnation is a preferred OEM process that seals porosity and leak paths in metal castings, sintered metal parts and electrical castings that form during the casting or ...
.
Mold making
In the casting process, a
pattern
A pattern is a regularity in the world, in human-made design, or in abstract ideas. As such, the elements of a pattern repeat in a predictable manner. A geometric pattern is a kind of pattern formed of geometric shapes and typically repeated l ...
is made in the shape of the desired part. Simple designs can be made in a single piece or solid pattern. More complex designs are made in two parts, called split patterns. A split pattern has a top or upper section, called a cope, and a bottom or lower section called a drag. Both solid and split patterns can have
cores inserted to complete the final part shape. Cores are used to create hollow areas in the mold that would otherwise be impossible to achieve. Where the cope and drag separates is called the
parting line
A parting line, in industrial casting of molds, is the border line in which draft angles change direction. One can check the parting line in the mould or product which divides the two half, i.e; the core and the cavity of a molded part. It is so ...
.
When making a pattern it is best to taper the edges so that the pattern can be removed without breaking the mold. This is called
draft
Draft, The Draft, or Draught may refer to:
Watercraft dimensions
* Draft (hull), the distance from waterline to keel of a vessel
* Draft (sail), degree of curvature in a sail
* Air draft, distance from waterline to the highest point on a vessel ...
. The opposite of draft is an undercut where there is part of the pattern under the mold material, making it impossible to remove the pattern without damaging the mold.
The pattern is made of wax, wood, plastic, or metal. The molds are constructed by several different processes dependent upon the type of foundry, metal to be poured, quantity of parts to be produced, size of the casting, and complexity of the casting. These mold processes include:
*
Sand casting
Sand casting, also known as sand molded casting, is a metal casting process characterized by using sand as the mold material. The term "sand casting" can also refer to an object produced via the sand casting process. Sand castings are produced i ...
— Green or resin bonded sand mold.
*
Lost-foam casting
Lost-foam casting (LFC) is a type of evaporative-pattern casting process that is similar to investment casting except foam is used for the pattern instead of wax. This process takes advantage of the low boiling point of polymer foams to simplify ...
— Polystyrene pattern with a mixture of ceramic and sand mold.
*
Investment casting
Investment casting is an industrial process based on lost-wax casting, one of the oldest known metal-forming techniques. The term "lost-wax casting" can also refer to modern investment casting processes.
Investment casting has been used in vari ...
— Wax or similar sacrificial pattern with a ceramic mold.
*
Ceramic mold casting Ceramic mold casting, also known ambiguously as ceramic molding, is a group of metal casting processes that use ceramics as the mold material. It is a combination of plaster mold casting and investment casting. There are two types of ceramic mold ...
— Plaster mold.
*
V-process
Sand casting, also known as sand molded casting, is a metal casting process characterized by using sand as the mold material. The term "sand casting" can also refer to an object produced via the sand casting process. Sand castings are produced ...
casting — Vacuum with thermoformed plastic to form sand molds. No moisture, clay or resin required.
*
Die casting
Die casting is a metal casting process that is characterized by forcing molten metal under high pressure into a mold cavity. The mold cavity is created using two hardened tool steel dies which have been machined into shape and work similarly t ...
— Metal mold.
*
Billet (ingot) casting — Simple mold for producing ingots of metal, normally for use in other foundries.
*
Loam molding Loam molding was formerly used for making cast iron or bronze cannon and is still used for casting large bells.
Loam (pronounced 'loom') is a mixture of sand and clay with water, sometimes with horse dung (valuable for its straw content), animal ...
- a built up mold used for casting large objects, such as
cannon
A cannon is a large- caliber gun classified as a type of artillery, which usually launches a projectile using explosive chemical propellant. Gunpowder ("black powder") was the primary propellant before the invention of smokeless powder ...
,
steam engine
A steam engine is a heat engine that performs mechanical work using steam as its working fluid. The steam engine uses the force produced by steam pressure to push a piston back and forth inside a cylinder. This pushing force can be trans ...
cylinders, and bells.
Pouring

In a foundry, molten metal is poured into
molds. Pouring can be accomplished with gravity, or it may be assisted with a vacuum or pressurized gas. Many modern foundries use robots or automatic pouring machines to pour molten metal. Traditionally, molds were poured by hand using
ladles.
Shakeout
The solidified metal component is then removed from its mold. Where the mold is sand based, this can be done by shaking or tumbling. This frees the casting from the sand, which is still attached to the metal runners and gates — which are the channels through which the molten metal traveled to reach the component itself.
Degating
Degating is the removal of the heads, runners, gates, and
risers from the casting. Runners, gates, and risers may be removed using
cutting torch
Principle of burn cutting
Oxy-fuel welding (commonly called oxyacetylene welding, oxy welding, or gas welding in the United States) and oxy-fuel cutting are processes that use fuel gases (or liquid fuels such as gasoline or petrol, diesel, ...
es,
bandsaw
A bandsaw (also written band saw) is a power saw with a long, sharp blade consisting of a continuous band of toothed metal stretched between two or more wheels to cut material. They are used principally in woodworking, metalworking, and lumb ...
s, or ceramic cutoff blades. For some metal types, and with some gating system designs, the sprue, runners, and gates can be removed by breaking them away from the casting with a sledge hammer or specially designed knockout machinery. Risers must usually be removed using a cutting method (see above) but some newer methods of riser removal use knockoff machinery with special designs incorporated into the riser neck geometry that allow the riser to break off at the right place.
The gating system required to produce castings in a mold yields leftover metal — including heads, risers, and sprue (sometimes collectively called sprue) — that can exceed 50% of the metal required to pour a full mold. Since this metal must be remelted as salvage, the yield of a particular gating configuration becomes an important economic consideration when designing various gating schemes, to minimize the cost of excess sprue, and thus overall melting costs.
Heat treating

Heat treating is a group of industrial and metalworking processes used to alter the physical, and sometimes chemical, properties of a material. The most common application is metallurgical. Heat treatments are also used in the manufacture of many other materials, such as glass. Heat treatment involves the use of heating or chilling, normally to extreme temperatures, to achieve a desired result such as hardening or softening of a material. Heat treatment techniques include
annealing,
case-hardening
Case-hardening or surface hardening is the process of hardening the surface of a metal object while allowing the metal deeper underneath to remain soft, thus forming a thin layer of harder metal at the surface. For iron or steel with low carbon ...
,
precipitation strengthening
Precipitation hardening, also called age hardening or particle hardening, is a heat treatment technique used to increase the yield strength of malleable materials, including most structural alloys of aluminium, magnesium, nickel, titanium, and so ...
,
tempering, and
quenching
In materials science, quenching is the rapid cooling of a workpiece in water, oil, polymer, air, or other fluids to obtain certain material properties. A type of heat treating, quenching prevents undesired low-temperature processes, such as pha ...
. Although the term "heat treatment" applies only to processes where the heating and cooling are done for the specific purpose of altering properties intentionally, heating and cooling often occur incidentally during other manufacturing processes such as hot forming or welding.
Surface cleaning
After degating and heat treating, sand or other molding media may remain adhered to the casting. To remove any mold remnants, the surface is cleaned using a blasting process. This means a granular media will be propelled against the surface of the casting to mechanically knock away the adhering sand. The media may be blown with compressed air, or may be hurled using a shot wheel. The cleaning media strikes the casting surface at high velocity to dislodge the mold remnants (for example, sand, slag) from the casting surface. Numerous materials may be used to clean cast surfaces, including steel, iron, other metal alloys, aluminium oxides, glass beads, walnut shells, baking powder, and many others. The blasting media is selected to develop the color and reflectance of the cast surface. Terms used to describe this process include cleaning, bead blasting, and
sand blasting
Sandblasting, sometimes known as abrasive blasting, is the operation of forcibly propelling a stream of abrasive material against a surface under high pressure to smooth a rough surface, roughen a smooth surface, shape a surface or remove su ...
.
Shot peening
Shot peening is a cold working process used to produce a compressive residual stress layer and modify the mechanical properties of metals and composites. It entails striking a surface with shot (round metallic, glass, or ceramic particles) with ...
may be used to further work-harden and finish the surface.
Finishing
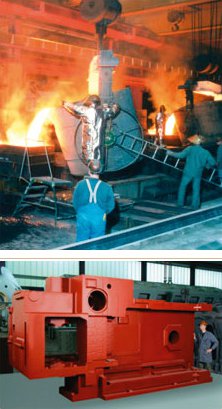
The final step in the process of casting usually involves grinding, sanding, or
machining
Machining is a process in which a material (often metal) is cut to a desired final shape and size by a controlled material-removal process. The processes that have this common theme are collectively called subtractive manufacturing, which utilizes ...
the component in order to achieve the desired dimensional accuracies, physical shape, and surface finish.
Removing the remaining gate material, called a gate stub, is usually done using a
grinder or
sander
A sander is a power tool used to smooth surfaces by abrasion with sandpaper. Sanders have a means to attach the sandpaper and a mechanism to move it rapidly contained within a housing with means to hand-hold it or fix it to a workbench. Woodwo ...
. These processes are used because their material removal rates are slow enough to control the amount of material being removed. These steps are done prior to any final machining.
After grinding, any surfaces that require tight dimensional control are machined. Many castings are machined in
CNC
Numerical control (also computer numerical control, and commonly called CNC) is the automated control of machining tools (such as drills, lathes, mills, grinders, routers and 3D printers) by means of a computer. A CNC machine processes a ...
milling
Milling may refer to:
* Milling (minting), forming narrow ridges around the edge of a coin
* Milling (grinding), breaking solid materials into smaller pieces by grinding, crushing, or cutting in a mill
* Milling (machining), a process of using rota ...
centers. The reason for this is that these processes have better dimensional capability and repeatability than many casting processes. However, it is not uncommon today for castings to be used without machining.
A few foundries provide other services before shipping cast products to their customers. It is common to paint castings to prevent corrosion and improve visual appeal. Some foundries assemble castings into complete machines or sub-assemblies. Other foundries
weld multiple castings or wrought metals together to form a finished product.
More and more, finishing processes are being performed by robotic machines, which eliminate the need for a human to physically grind or break parting lines, gating material, or feeders. Machines can reduce risk of injury to workers and lower costs for consumables — while also increasing productivity. They also limit the potential for human error and increase repeatability in the quality of grinding.
See also
*
Aluminium alloy inclusions An inclusion is a solid particle in liquid aluminium alloy. It is usually non-metallic and can be of different nature depending on its source.
Problems related to inclusions
Inclusions can create problems in the casting when they are large and in t ...
*
Bellfounding
Bellfounding is the casting and tuning of large bronze bells in a foundry for use such as in churches, clock towers and public buildings, either to signify the time or an event, or as a musical carillon or chime. Large bells are made by casting ...
*
Core (manufacturing) A core is a device used in casting and molding (process), moulding processes to produce internal cavities and wikt:reentrant, reentrant angles (an interior angle that is greater than 180°). The core is normally a disposable item that is destroyed t ...
*
Foundry sand testing
Foundry sand testing is a process used to determine if the foundry sand has the correct properties for a certain casting process. The sand is used to make moulds and cores via a pattern. In a sand casting foundry there are broadly two reasons f ...
*
Ironworks
An ironworks or iron works is an industrial plant where iron is smelted and where heavy iron and steel products are made. The term is both singular and plural, i.e. the singular of ''ironworks'' is ''ironworks''.
Ironworks succeeded bloomeri ...
*
Smelting
Smelting is a process of applying heat to ore, to extract a base metal. It is a form of extractive metallurgy. It is used to extract many metals from their ores, including silver, iron, copper, and other base metals. Smelting uses heat and a ch ...
References
External links
American Foundry SocietyCanadian Foundry AssociationThe Institute of Indian FoundrymenPhotographic documentation of the founding processSteel Founders' Society of AmericaWorld Foundry Organization
{{Authority control
Metalworking
Firing techniques
Industrial buildings