
A flapwheel and the related flap disk is an abrasive disk, used for metal finishing. Unlike the simpler flat disks, made from a circular flat sheet of a
coated abrasive
upright=1.35, Sheets of sandpaper with different grit sizes (40 (coarse), 80, 150, 240, 600 (fine)).
Sandpaper and glasspaper are names used for a type of coated abrasive that consists of sheets of paper or cloth with abrasive material glued to ...
, a flapwheel is made of multiple overlapping small pieces or 'flaps', bonded to a central hub.
Advantages
The advantages of a flapwheel over a traditional disk are twofold:
* The separate flaps each attack the workpiece surface at a slightly different angle, and this varies slightly with tool angle. This avoids the common problem with flat sheets, where they produce repeated identical scratches.
* Abrasive wear is distributed more evenly across the flaps, and through the length of each flap. Flaps wear from their outer ends and the sheet carrier cuts back as the abrasive coating is worn away. The wheel remains useful even as the flaps erode. Compared to flat sheets, that are discarded after only a small area of the abrasive is truly worn-out, this is a much more efficient use of the abrasive material.
Development
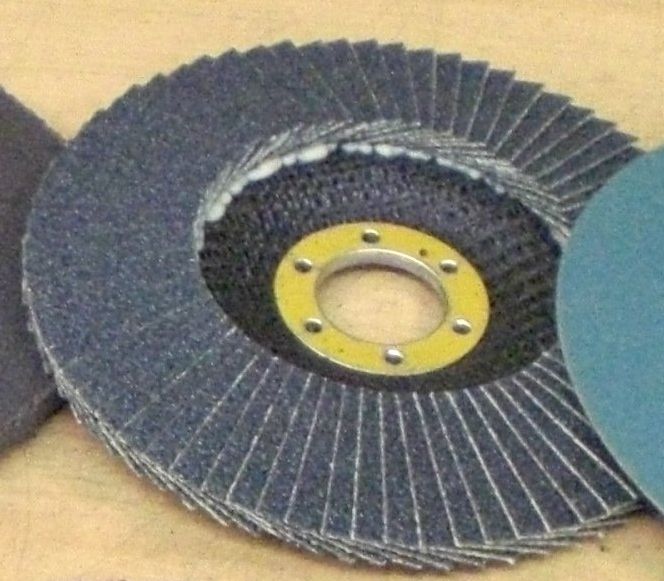
They appeared in the 1950s and their use was encouraged by developments in
gas turbine
A gas turbine, also called a combustion turbine, is a type of continuous flow internal combustion engine. The main parts common to all gas turbine engines form the power-producing part (known as the gas generator or core) and are, in the directi ...
s. These demanded an increased production of fine
investment casting
Investment casting is an industrial process based on lost-wax casting, one of the oldest known metal-forming techniques. The term "lost-wax casting" can also refer to modern investment casting processes.
Investment casting has been used in vari ...
s that required careful polishing. In particular, the high centrifugal stresses these experienced in service required a finishing technique that did not give rise to oriented scratches that could act as
stress risers.
The first flapwheels were made from cut sheets of abrasive, stacked into a multi-layered flat disk. These gained the advantage of long life from their materials, but their geometry was still flat and so they tended to produce surface flats if not carefully handled.
Early flapwheels were large diameter and intended for use on fixed
buffing machine
Polishing and buffing are finishing processes for smoothing a workpiece's surface using an abrasive and a work wheel or a leather strop. Technically, ''polishing'' refers to processes that uses an abrasive that is glued to the work wheel, while ...
s. They were used for deburring and polishing of castings, often instead of wire wheels. These cut faster, with less burnishing and surface contamination from the bristles.
Portable flapwheels were made by bonding radial flaps of abrasive into a hub fitted with a spindle shank.
Flap Wheel Abrasives
/ref> These were intended for use with electric drill
A drill is a tool used for making round holes or driving fasteners. It is fitted with a bit, either a drill or driverchuck. Hand-operated types are dramatically decreasing in popularity and cordless battery-powered ones proliferating due to ...
s and were limited to a maximum speed of around 1,000 rpm.
With developments in abrasive coating, the sheet material could withstand greater forces and speeds. This allowed the production of flapwheels for use with high speed angle grinder
An angle grinder, also known as a side grinder or disc grinder, is a handheld power tool used for grinding (abrasive cutting) and polishing. Although developed originally as tools for rigid abrasive discs, the availability of an interchangeable ...
s.[Angle grinders typically run at speeds around 10,000 rpm.] These disks were different in format: flatter, like the original rigid angle grinder disks, and with the flaps arranged in a densely overlapped layout rather than radial. The extra lifetime this gave to the disk allowed their use for stock removal and metal shaping, not just finishing and polishing.
The flexibility of a flapwheel is an advantage for smoothing curved work and avoids the production of facets, as was a problem for rigid disks. This was taken further advantage of with the development of foam-bonded flapwheels. These use fewer flaps, spaced apart by a flexible foam spacer. This makes them even more flexible, thus more suited for producing a smooth finish to curved surfaces.
References
{{Reflist
Coated abrasives