A turbomolecular pump is a type of
vacuum pump
A vacuum pump is a device that draws gas molecules from a sealed volume in order to leave behind a partial vacuum. The job of a vacuum pump is to generate a relative vacuum within a capacity. The first vacuum pump was invented in 1650 by Otto ...
, superficially similar to a
turbopump
A turbopump is a propellant pump with two main components: a rotodynamic pump and a driving gas turbine, usually both mounted on the same shaft, or sometimes geared together. They were initially developed in Germany in the early 1940s. The purpo ...
, used to obtain and maintain high
vacuum
A vacuum is a space devoid of matter. The word is derived from the Latin adjective ''vacuus'' for "vacant" or " void". An approximation to such vacuum is a region with a gaseous pressure much less than atmospheric pressure. Physicists often di ...
.
These pumps work on the principle that gas molecules can be given
momentum in a desired direction by repeated collision with a moving solid surface. In a turbomolecular pump, a rapidly spinning
fan rotor 'hits' gas molecules from the inlet of the pump towards the exhaust in order to create or maintain a vacuum.
Operating principles
Most turbomolecular pumps employ multiple stages, each consisting of a quickly rotating
rotor blade
A helicopter main rotor or rotor system is the combination of several rotary wings (rotor blades) with a control system, that generates the aerodynamic lift force that supports the weight of the helicopter, and the thrust that counteracts aerody ...
and stationary
stator blade pair. The system is an
axial compressor that puts energy into the gas, rather than a
turbine
A turbine ( or ) (from the Greek , ''tyrbē'', or Latin ''turbo'', meaning vortex) is a rotary mechanical device that extracts energy from a fluid flow and converts it into useful work. The work produced by a turbine can be used for generating ...
, which takes energy out of a moving fluid to create rotary power, thus "turbomolecular pump" is a misnomer. Gas captured by the upper stages is pushed into the lower stages and successively compressed to the level of the fore-vacuum (backing pump) pressure.
As the
gas
Gas is one of the four fundamental states of matter (the others being solid, liquid, and plasma).
A pure gas may be made up of individual atoms (e.g. a noble gas like neon), elemental molecules made from one type of atom (e.g. oxygen), or ...
molecules enter through the inlet, the rotor, which has a number of angled blades, hits the molecules. Thus the mechanical energy of the blades is transferred to the gas molecules. With this newly acquired momentum, the gas molecules enter into the gas transfer holes in the stator. This leads them to the next stage where they again collide with the rotor surface, and this process is continued, finally leading them outwards through the exhaust.
Because of the relative motion of rotor and stator, molecules preferentially hit the lower side of the blades. Because the blade surface looks down, most of the scattered molecules will leave it downwards. The surface is rough, so no reflection will occur. A blade needs to be thick and stable enough for high pressure operation and as thin as possible and slightly bent for maximum compression. For high compression ratios the throat between adjacent rotor blades (as shown in the image) is pointing as much as possible in the forward direction. For high flow rates the blades are at 45° and reach close to the axis.
Because the compression of each stage is ≈10, each stage closer to the outlet is considerably smaller than the preceding inlet stages. This has two consequences. The geometric progression tells us that infinite stages could ideally fit into a finite axial length. The finite length in this case is the full height of the housing as the
bearings, the motor, and controller and some of the coolers can be installed inside on the axis. Radially, to grasp as much of the thin gas at the entrance, the inlet-side rotors would ideally have a larger
radius
In classical geometry, a radius ( : radii) of a circle or sphere is any of the line segments from its center to its perimeter, and in more modern usage, it is also their length. The name comes from the latin ''radius'', meaning ray but also the ...
, and correspondingly higher centrifugal force; ideal blades would get exponentially thinner towards their tips and carbon fibers should reinforce the aluminium blades. However, because the average speed of a blade affects pumping so much this is done by increasing the root
diameter
In geometry, a diameter of a circle is any straight line segment that passes through the center of the circle and whose endpoints lie on the circle. It can also be defined as the longest chord of the circle. Both definitions are also valid fo ...
rather than the tip diameter where practical.
The performance of a turbomolecular pump is strongly related to the frequency of the rotor. As rpm increases, the rotor blades deflect more. To increase speed and reduce the deformation, stiffer materials and different blade designs have been suggested.
Turbomolecular pumps must operate at very high speeds, and the friction heat buildup imposes design limitations. Some turbomolecular pumps use
magnetic bearing
A magnetic bearing is a type of bearing that supports a load using magnetic levitation. Magnetic bearings support moving parts without physical contact. For instance, they are able to levitate a rotating shaft and permit relative motion with v ...
s to reduce
friction
Friction is the force resisting the relative motion of solid surfaces, fluid layers, and material elements sliding against each other. There are several types of friction:
*Dry friction is a force that opposes the relative lateral motion of ...
and oil contamination. Because the magnetic bearings and the temperature cycles allow for only a limited clearance between rotor and stator, the blades at the high pressure stages are somewhat degenerated into a single helical foil each. Laminar flow cannot be used for pumping, because laminar turbines stall when not used at the designed flow. The pump can be cooled down to improve the compression, but should not be so cold as to condense ice on the blades.
When a turbopump is stopped, the oil from the backing vacuum may backstream through the turbopump and contaminate the chamber. One way to prevent this is to introduce a laminar flow of
nitrogen
Nitrogen is the chemical element with the symbol N and atomic number 7. Nitrogen is a nonmetal and the lightest member of group 15 of the periodic table, often called the pnictogens. It is a common element in the universe, estimated at se ...
through the pump. The transition from vacuum to nitrogen and from a running to a still turbopump has to be synchronized precisely to avoid mechanical stress to the pump and overpressure at the exhaust. A thin membrane and a valve at the exhaust should be added to protect the turbopump from excessive back pressure (e.g. after a power failure or leaks in the backing vacuum).
The rotor is stabilized in all of its six
degrees of freedom. One degree is governed by the electric motor. Minimally, this degree must be stabilized electronically (or by a
diamagnetic
Diamagnetic materials are repelled by a magnetic field; an applied magnetic field creates an induced magnetic field in them in the opposite direction, causing a repulsive force. In contrast, paramagnetic and ferromagnetic materials are attracted ...
material, which is too unstable to be used in a precision pump bearing). Another way (ignoring losses in
magnetic cores at high frequencies) is to construct this bearing as an axis with a sphere at each end. These spheres are inside hollow static spheres. On the surface of each sphere is a checkerboard pattern of inwards and outwards going magnetic field lines. As the checkerboard
pattern
A pattern is a regularity in the world, in human-made design, or in abstract ideas. As such, the elements of a pattern repeat in a predictable manner. A geometric pattern is a kind of pattern formed of geometric shapes and typically repeated li ...
of the static spheres is rotated, the rotor rotates. In this construction no axis is made stable on the cost of making another axis unstable, but all axes are neutral and the electronic regulation is less stressed and will be more dynamically stable. Hall effect sensors can be used to sense the rotational position and the other degrees of freedom can be measured capacitively.
Maximum pressure
At atmospheric pressure, the
mean free path
In physics, mean free path is the average distance over which a moving particle (such as an atom, a molecule, or a photon) travels before substantially changing its direction or energy (or, in a specific context, other properties), typically as a ...
of air is about 70 nm. A turbomolecular pump can work only if those molecules hit by the moving blades reach the stationary blades before colliding with other molecules on their way. To achieve that, the gap between moving blades and stationary blades must be close to or less than the mean free path. From a practical construction standpoint, a feasible gap between the blade sets is on the order of 1 mm, so a turbopump will stall (no net pumping) if exhausted directly to the atmosphere. Since the mean free path is inversely proportional to pressure, a turbopump will pump when the exhaust pressure is less than about where the mean free path is about 0.7 mm.
Most turbopumps have a
Holweck pump A molecular drag pump is a type of vacuum pump that utilizes the drag of air molecules against a rotating surface. The most common sub-type is the ''Holweck pump'', which contains a rotating cylinder with spiral grooves which direct the gas from the ...
(or molecular drag pump) as their last stage to increase the maximum backing pressure (exhaust pressure) to about 1–10 mbar. Theoretically, a centrifugal pump, a side channel pump, or a
regenerative pump could be used to back to atmospheric pressure directly, but currently there is no commercially available turbopump that exhausts directly to atmosphere. In most cases, the exhaust is connected to a mechanical backing pump (usually called
roughing pump A roughing pump is any vacuum pump (typically mechanical) used to initially evacuate a vacuum system, as a first stage towards achieving high vacuum or ultra high vacuum. The term "roughing pump" derives from the vacuum range it works in, "rough v ...
) that produces a pressure low enough for the turbomolecular pump to work efficiently. Typically, this backing pressure is below 0.1 mbar and commonly about 0.01 mbar. The backing pressure is rarely below 10
−3 mbar (mean free path ≈ 70 mm) because the flow resistance of the vacuum pipe between the turbopump and the roughing pump becomes significant.
The turbomolecular pump can be a very versatile pump. It can generate many degrees of vacuum from intermediate vacuum (≈10
−2 Pa) up to
ultra-high vacuum
Ultra-high vacuum (UHV) is the vacuum regime characterised by pressures lower than about . UHV conditions are created by pumping the gas out of a UHV chamber. At these low pressures the mean free path of a gas molecule is greater than approximately ...
levels (≈10
−8 Pa).
Multiple turbomolecular pumps in a lab or manufacturing-plant can be connected by tubes to a small backing pump. Automatic valves and
diffusion pump
Diffusion pumps use a high speed jet of vapor to direct gas molecules in the pump throat down into the bottom of the pump and out the exhaust. They were the first type of high vacuum pumps operating in the regime of free molecular flow, where the ...
like injection into a large buffer-tube in front of the backing pump prevents any overpressure from one pump to stall another pump.
Practical considerations
Laws of
fluid dynamics do not provide good approximations for the behavior of individual, highly separated, non-interacting gas molecules, like those found in
high vacuum environments. The maximum compression varies linearly with circumferential rotor speed. In order to obtain extremely low pressures down to 1
micropascal
The pascal (symbol: Pa) is the unit of pressure in the International System of Units (SI), and is also used to quantify internal pressure, stress, Young's modulus, and ultimate tensile strength. The unit, named after Blaise Pascal, is defined as ...
, rotation rates of 20,000 to 90,000 revolutions per minute are often necessary. Unfortunately, the compression ratio varies exponentially with the square root of the molecular weight of the gas. Thus, heavy molecules are pumped much more efficiently than light
molecule
A molecule is a group of two or more atoms held together by attractive forces known as chemical bonds; depending on context, the term may or may not include ions which satisfy this criterion. In quantum physics, organic chemistry, and bioche ...
s. Most gases are heavy enough to be well pumped but it is difficult to pump
hydrogen
Hydrogen is the chemical element with the symbol H and atomic number 1. Hydrogen is the lightest element. At standard conditions hydrogen is a gas of diatomic molecules having the formula . It is colorless, odorless, tasteless, non-toxic ...
and
helium
Helium (from el, ἥλιος, helios, lit=sun) is a chemical element with the symbol He and atomic number 2. It is a colorless, odorless, tasteless, non-toxic, inert, monatomic gas and the first in the noble gas group in the periodic table. ...
efficiently.
An additional drawback stems from the high rotor speed of this type of pump: very
high grade bearings are required, which increase the cost.
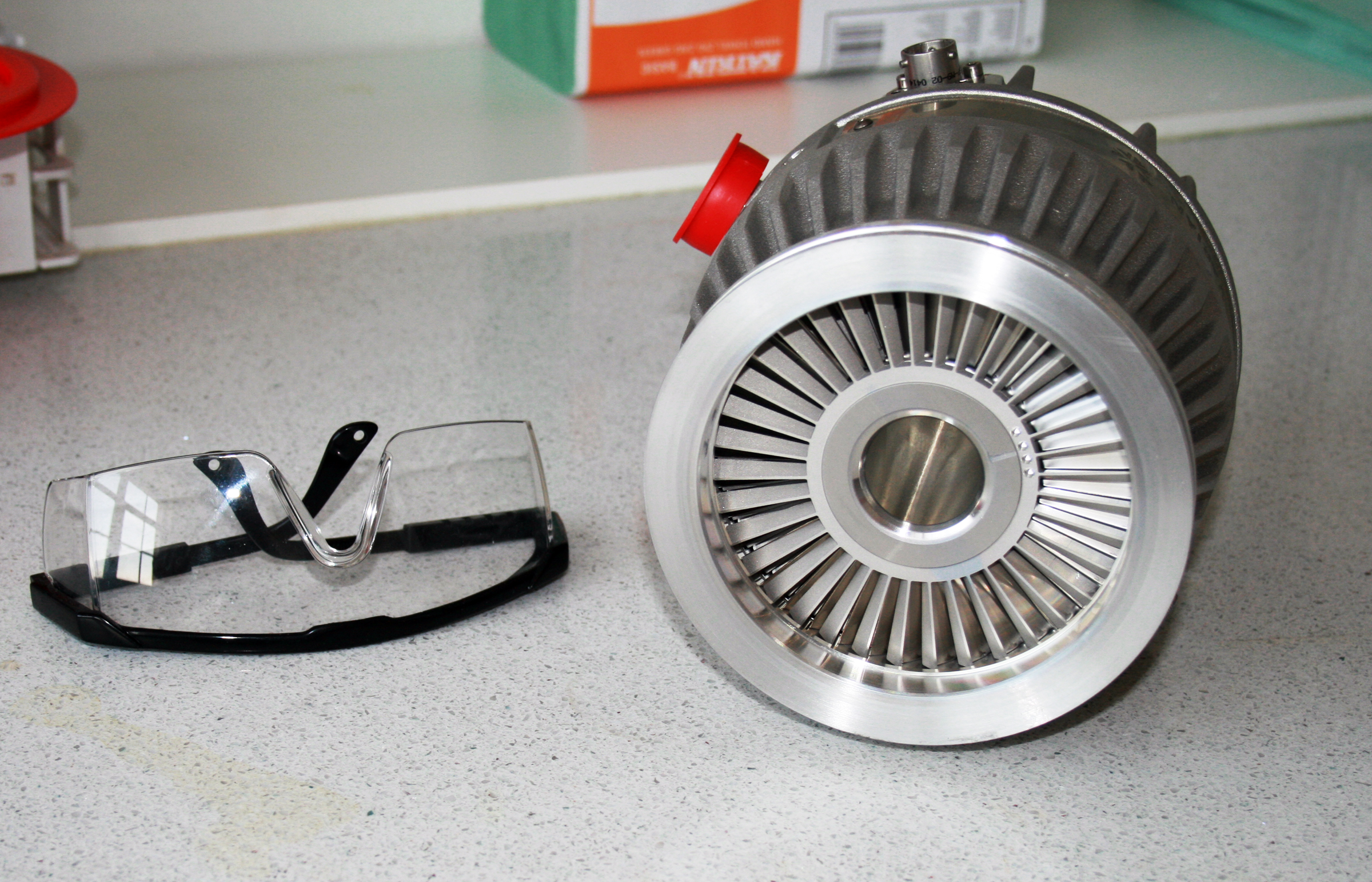
Because turbomolecular pumps only work in molecular flow conditions, a pure turbomolecular pump will require a very large backing pump to work effectively. Thus, many modern pumps have a molecular drag stage such as a
Holweck or Gaede mechanism near the exhaust to reduce the size of backing pump required.
Much of recent turbo pump development has been focused on improvement of the effectiveness of the drag stages. As gas is removed from a pumped space, the lighter gases hydrogen and helium become a larger proportion of the remaining gas load. In recent years it has been demonstrated that the precise design of the surface geometry of the drag stages can have a marked effect on pumping of these light gases, improving compression ratios by up to two orders of magnitude for given pumping volume. As a result, it is possible to use much smaller backing pumps than would be required by pure turbomolecular pumps and/or design more compact turbomolecular pumps.
History
The turbomolecular pump was invented in 1958 by W. Becker, based on the older molecular drag pumps developed by
Wolfgang Gaede in 1913,
Fernand Holweck
Fernand Holweck (21 July 1890 – 24 December 1941) was a French physicist who made important contributions in the fields of vacuum technology, electromagnetic radiation and gravitation. He is also remembered for his personal sacrifice in the c ...
in 1923 and
Manne Siegbahn
Karl Manne Georg Siegbahn FRS(For) HFRSE (3 December 1886 – 26 September 1978) was a Swedish physicist who was awarded the Nobel Prize in Physics in 1924 "for his discoveries and research in the field of X-ray spectroscopy".
Biography
Siegbahn ...
in 1944.
References
External links
Some practical guidelines
{{DEFAULTSORT:Turbomolecular Pump
Vacuum pumps