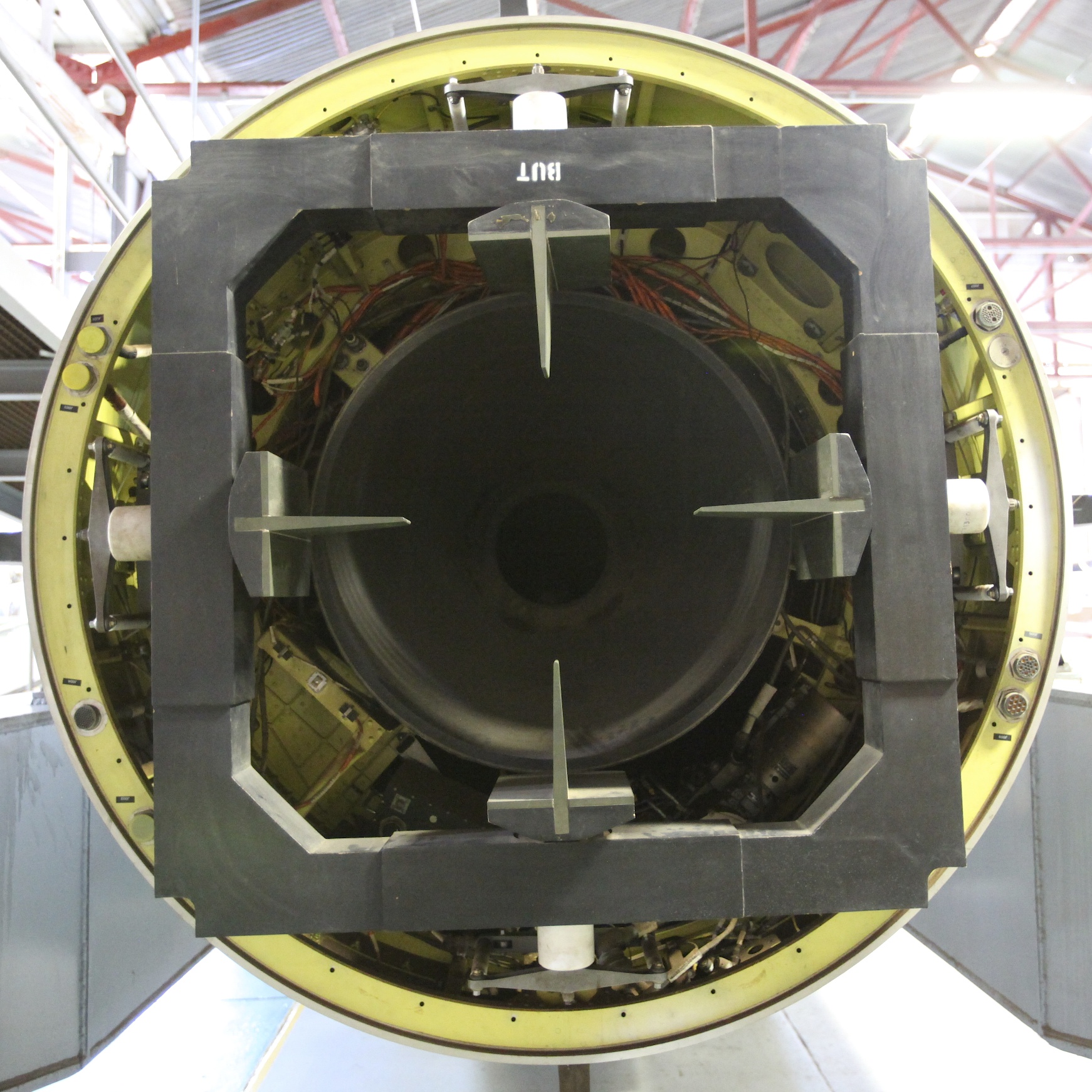
A rocket engine nozzle is a
propelling nozzle
A propelling nozzle is a nozzle that converts the internal energy of a working gas into propulsive force; it is the nozzle, which forms a jet, that separates a gas turbine, or gas generator, from a jet engine.
Propelling nozzles accelerate the av ...
(usually of the
de Laval
Karl Gustaf Patrik de Laval (; 9 May 1845 – 2 February 1913) was a Swedish engineer and inventor who made important contributions to the design of steam turbines and centrifugal separation machinery for dairy.
Life
Gustaf de Laval was born a ...
type) used in a
rocket engine
A rocket engine uses stored rocket propellants as the reaction mass for forming a high-speed propulsive jet of fluid, usually high-temperature gas. Rocket engines are reaction engines, producing thrust by ejecting mass rearward, in accordanc ...
to expand and accelerate
combustion
Combustion, or burning, is a high-temperature exothermic redox chemical reaction between a fuel (the reductant) and an oxidant, usually atmospheric oxygen, that produces oxidized, often gaseous products, in a mixture termed as smoke. Combusti ...
products to high
supersonic
Supersonic speed is the speed of an object that exceeds the speed of sound ( Mach 1). For objects traveling in dry air of a temperature of 20 °C (68 °F) at sea level, this speed is approximately . Speeds greater than five times ...
velocities.
Simply: propellants pressurized by either
pump
A pump is a device that moves fluids (liquids or gases), or sometimes slurries, by mechanical action, typically converted from electrical energy into hydraulic energy. Pumps can be classified into three major groups according to the method they u ...
s or high pressure
ullage gas to anywhere between two to several hundred
atmospheres are injected into a combustion chamber to burn, and the combustion chamber leads into a nozzle which converts the energy contained in
high pressure, high temperature combustion products into kinetic energy by accelerating the gas to high velocity and near-ambient pressure.
History
Simple
bell-shaped nozzles were developed in the 1500s. The de Laval nozzle was originally developed in the 19th century by
Gustaf de Laval
Karl Gustaf Patrik de Laval (; 9 May 1845 – 2 February 1913) was a Swedish engineer and inventor who made important contributions to the design of steam turbines and centrifugal separation machinery for dairy.
Life
Gustaf de Laval was born at ...
for use in
steam turbine
A steam turbine is a machine that extracts thermal energy from pressurized steam and uses it to do mechanical work on a rotating output shaft. Its modern manifestation was invented by Charles Parsons in 1884. Fabrication of a modern steam turbin ...
s. It was first used in an early rocket engine developed by
Robert Goddard
Robert Hutchings Goddard (October 5, 1882 – August 10, 1945) was an American engineer, professor, physicist, and inventor who is credited with creating and building the world's first liquid-fueled rocket. Goddard successfully laun ...
, one of the fathers of modern rocketry. It has since been used in almost all rocket engines, including
Walter Thiel
Walter Thiel (3 March 1910, Breslau – 17 August 1943, Karlshagen, near Peenemünde) was a German rocket scientist.
Thiel provided the decisive ideas for the A4 (V-2) rocket engine and his research enabled rockets to head towards space.
Lif ...
's implementation, which made possible Germany's
V-2
The V-2 (german: Vergeltungswaffe 2, lit=Retaliation Weapon 2), with the technical name ''Aggregat 4'' (A-4), was the world’s first long-range guided ballistic missile. The missile, powered by a liquid-propellant rocket engine, was develope ...
rocket.
Atmospheric use
The optimal size of a rocket engine nozzle is achieved when the exit pressure equals ambient (atmospheric) pressure, which decreases with increasing altitude. The reason for this is as follows: using a quasi-one-dimensional approximation of the flow, if ambient pressure is higher than the exit pressure, it decreases the net thrust produced by the rocket, which can be seen through a force-balance analysis. If ambient pressure is lower, while the force balance indicates that the thrust will increase, the isentropic Mach relations show that the area ratio of the nozzle could have been greater, which would result in a higher exit velocity of the propellant, increasing thrust. For rockets traveling from the Earth to orbit, a simple nozzle design is only optimal at one altitude, losing efficiency and wasting fuel at other altitudes.
Just past the throat, the pressure of the gas is higher than ambient pressure and needs to be lowered between the throat and the nozzle exit by expansion. If the pressure of the exhaust leaving the nozzle exit is still above ambient pressure, then a nozzle is said to be ''underexpanded''; if the exhaust is below ambient pressure, then it is ''overexpanded''.
Slight overexpansion causes a slight reduction in efficiency, but otherwise does little harm. However, if the exit pressure is less than approximately 40% that of ambient, then "flow separation" occurs. This can cause exhaust instabilities that can cause damage to the nozzle, control difficulties of the vehicle or the engine, and in more extreme cases, destruction of the engine.
In some cases, it is desirable for reliability and safety reasons to ignite a rocket engine on the ground that will be used all the way to orbit. For optimal
liftoff
Liftoff, lift-off, or lift off may refer to:
Technology
* Lift-off (microtechnology), a fabrication technique
* Flame lift-off, a separation of flame from burner device
* Takeoff, the first moment of flight of an aerospace vehicle
* Reduction o ...
performance, the pressure of the gases exiting nozzle should be at sea-level pressure when the rocket is near sea level (at takeoff). However, a nozzle designed for sea-level operation will quickly lose efficiency at higher altitudes. In a
multi-stage
A multistage rocket or step rocket is a launch vehicle that uses two or more rocket ''stages'', each of which contains its own engines and propellant. A ''tandem'' or ''serial'' stage is mounted on top of another stage; a ''parallel'' stage is ...
design, the second stage rocket engine is primarily designed for use at high altitudes, only providing additional thrust after the first-stage engine performs the initial liftoff. In this case, designers will usually opt for an overexpanded nozzle (at sea level) design for the second stage, making it more efficient at higher altitudes, where the ambient pressure is lower. This was the technique employed on the
Space Shuttle
The Space Shuttle is a retired, partially reusable low Earth orbital spacecraft system operated from 1981 to 2011 by the U.S. National Aeronautics and Space Administration (NASA) as part of the Space Shuttle program. Its official program na ...
's overexpanded (at sea level)
main engines (SSMEs), which spent most of their powered trajectory in near-vacuum, while the shuttle's two sea-level efficient
solid rocket boosters provided the majority of the initial liftoff thrust. In the vacuum of space virtually all nozzles are underexpanded because to fully expand the gas’s the nozzle would have to be infinitely long, as a result engineers have to choose a design which will take advantage of the extra expansion (thrust and efficiency) whilst also not adding excessive weight and compromising the vehicle’s performance.
Vacuum use
For nozzles that are used in vacuum or at very high altitude, it is impossible to match ambient pressure; rather, nozzles with larger area ratio are usually more efficient. However, a very long nozzle has significant mass, a drawback in and of itself. A length that optimises overall vehicle performance typically has to be found. Additionally, as the temperature of the gas in the nozzle decreases, some components of the exhaust gases (such as water vapour from the combustion process) may condense or even freeze. This is highly undesirable and needs to be avoided.
Magnetic nozzle A magnetic nozzle is a convergent-divergent magnetic field that guides, expands and accelerates a plasma jet into vacuum for the purpose of space propulsion. The magnetic field in a magnetic nozzle plays a similar role to the convergent-divergent ...
s have been proposed for some types of propulsion (for example,
Variable Specific Impulse Magnetoplasma Rocket
The Variable Specific Impulse Magnetoplasma Rocket (VASIMR) is an electrothermal thruster under development for possible use in spacecraft propulsion. It uses radio waves to ionize and heat an inert propellant, forming a plasma, then a magnetic ...
, VASIMR), in which the flow of
plasma or ions are directed by
magnetic field
A magnetic field is a vector field that describes the magnetic influence on moving electric charges, electric currents, and magnetic materials. A moving charge in a magnetic field experiences a force perpendicular to its own velocity and to ...
s instead of walls made of solid materials. These can be advantageous, since a magnetic field itself cannot melt, and the plasma temperatures can reach millions of
kelvin
The kelvin, symbol K, is the primary unit of temperature in the International System of Units (SI), used alongside its prefixed forms and the degree Celsius. It is named after the Belfast-born and University of Glasgow-based engineer and phys ...
s. However, there are often thermal design challenges presented by the coils themselves, particularly if superconducting coils are used to form the throat and expansion fields.
de Laval nozzle in 1 dimension

The analysis of gas flow through de Laval nozzles involves a number of concepts and simplifying assumptions:
* The combustion gas is assumed to be an
ideal gas
An ideal gas is a theoretical gas composed of many randomly moving point particles that are not subject to interparticle interactions. The ideal gas concept is useful because it obeys the ideal gas law, a simplified equation of state, and is a ...
.
* The gas flow is
isentropic
In thermodynamics, an isentropic process is an idealized thermodynamic process that is both adiabatic and reversible. The work transfers of the system are frictionless, and there is no net transfer of heat or matter. Such an idealized process ...
; i.e., at constant
entropy
Entropy is a scientific concept, as well as a measurable physical property, that is most commonly associated with a state of disorder, randomness, or uncertainty. The term and the concept are used in diverse fields, from classical thermodynam ...
, as the result of the assumption of non-viscous fluid, and
adiabatic process.
* The gas flow rate is constant (i.e., steady) during the period of the
propellant burn.
* The gas flow is non-turbulent and axisymmetric from gas inlet to exhaust gas exit (i.e., along the nozzle's axis of symmetry).
* The flow is
compressible
In thermodynamics and fluid mechanics, the compressibility (also known as the coefficient of compressibility or, if the temperature is held constant, the isothermal compressibility) is a measure of the instantaneous relative volume change of a f ...
as the fluid is a gas.
As the combustion gas enters the rocket nozzle, it is traveling at
subsonic velocities. As the throat constricts, the gas is forced to accelerate until at the nozzle throat, where the cross-sectional area is the least, the linear velocity becomes
sonic. From the throat the cross-sectional area then increases, the gas expands and the linear velocity becomes progressively more
supersonic
Supersonic speed is the speed of an object that exceeds the speed of sound ( Mach 1). For objects traveling in dry air of a temperature of 20 °C (68 °F) at sea level, this speed is approximately . Speeds greater than five times ...
.
The linear velocity of the exiting exhaust gases can be calculated using the following equation
[Richard Nakka's Equation 12]
/ref>
/ref>
:
where:
:
Some typical values of the exhaust gas velocity ''v''e for rocket engines burning various propellants are:
* 1.7 to 2.9 km/s (3800 to 6500 mi/h) for liquid monopropellant
Monopropellants are propellants consisting of chemicals that release energy through exothermic chemical decomposition. The molecular bond energy of the monopropellant is released usually through use of a catalyst. This can be contrasted with bipro ...
s
* 2.9 to 4.5 km/s (6500 to 10100 mi/h) for liquid bipropellant
The highest specific impulse chemical rockets use liquid propellants (liquid-propellant rockets). They can consist of a single chemical (a monopropellant) or a mix of two chemicals, called bipropellants. Bipropellants can further be divided into ...
s
* 2.1 to 3.2 km/s (4700 to 7200 mi/h) for solid propellant
A propellant (or propellent) is a mass that is expelled or expanded in such a way as to create a thrust or other motive force in accordance with Newton's third law of motion, and "propel" a vehicle, projectile, or fluid payload. In vehicles, the e ...
s
As a note of interest, ''v''e is sometimes referred to as the ''ideal exhaust gas velocity'' because it based on the assumption that the exhaust gas behaves as an ideal gas.
As an example calculation using the above equation, assume that the propellant combustion gases are: at an absolute pressure entering the nozzle of ''p'' = 7.0MPa and exit the rocket exhaust at an absolute pressure of ''p''e = 0.1MPa; at an absolute temperature of ''T'' = 3500K; with an isentropic expansion factor of γ = 1.22 and a molar mass of ''M'' = 22 kg/kmol. Using those values in the above equation yields an exhaust velocity ''v''e = 2802 m/s or 2.80 km/s which is consistent with above typical values.
The technical literature can be very confusing because many authors fail to explain whether they are using the universal gas law constant ''R'' which applies to any ideal gas
An ideal gas is a theoretical gas composed of many randomly moving point particles that are not subject to interparticle interactions. The ideal gas concept is useful because it obeys the ideal gas law, a simplified equation of state, and is a ...
or whether they are using the gas law constant ''R''s which only applies to a specific individual gas. The relationship between the two constants is ''R''s = ''R''/''M'', where ''R'' is the universal gas constant, and ''M'' is the molar mass of the gas.
Specific impulse
Thrust
Thrust is a reaction force described quantitatively by Newton's third law. When a system expels or accelerates mass in one direction, the accelerated mass will cause a force of equal magnitude but opposite direction to be applied to that syst ...
is the force that moves a rocket through the air or space. Thrust is generated by the propulsion
Propulsion is the generation of force by any combination of pushing or pulling to modify the translational motion of an object, which is typically a rigid body (or an articulated rigid body) but may also concern a fluid. The term is derived from ...
system of the rocket through the application of Newton's third law of motion: "For every action there is an equal and opposite reaction". A gas or working fluid is accelerated out the rear of the rocket engine nozzle, and the rocket is accelerated in the opposite direction. The thrust of a rocket engine nozzle can be defined as:[NASA: Rocket thrust]
/ref>
/ref>
:
the term in parenthesis is known as equivalent velocity,
:
The specific impulse is the ratio of the thrust produced to the weight flow of the propellants. It is a measure of the fuel efficiency of a rocket engine. In English Engineering units
Some fields of engineering in the United States use a system of measurement of physical quantities known as the English Engineering Units. Despite its name, the system is based on United States customary units of measure; it is not used in Englan ...
it can be obtained as[NASA:Rocket specific impulse]
/ref>
:
where:
:
For a perfectly expanded nozzle case, where , the formula becomes
:
In cases where this may not be so, since for a rocket nozzle is proportional to , it is possible to define a constant quantity that is the vacuum for any given engine thus:
:
and hence:
:
which is simply the vacuum thrust minus the force of the ambient atmospheric pressure acting over the exit plane.
Essentially then, for rocket nozzles, the ambient pressure acting on the engine cancels except over the exit plane of the rocket engine in a rearward direction, while the exhaust jet generates forward thrust.
Aerostatic back-pressure and optimal expansion
As the gas travels down the expansion part of the nozzle, the pressure and temperature decrease, while the speed of the gas increases.
The supersonic nature of the exhaust jet means that the pressure of the exhaust can be significantly different from ambient pressure – the outside air is unable to equalize the pressure upstream due to the very high jet velocity. Therefore, for supersonic nozzles, it is actually possible for the pressure of the gas exiting the nozzle to be significantly below or very greatly above ambient pressure.
If the exit pressure is too low, then the jet can separate from the nozzle. This is often unstable, and the jet will generally cause large off-axis thrusts and may mechanically damage the nozzle.
This separation generally occurs if the exit pressure drops below roughly 30–45% of ambient, but separation may be delayed to far lower pressures if the nozzle is designed to increase the pressure at the rim, as is achieved with the SSME (1–2 psi at 15 psi ambient).
In addition, as the rocket engine starts up or throttles, the chamber pressure varies, and this generates different levels of efficiency. At low chamber pressures the engine is almost inevitably going to be grossly over-expanded.
Optimal shape
The ratio of the area of the narrowest part of the nozzle to the exit plane area is mainly what determines how efficiently the expansion of the exhaust gases is converted into linear velocity, the exhaust velocity, and therefore the thrust
Thrust is a reaction force described quantitatively by Newton's third law. When a system expels or accelerates mass in one direction, the accelerated mass will cause a force of equal magnitude but opposite direction to be applied to that syst ...
of the rocket engine. The gas properties have an effect as well.
The shape of the nozzle also modestly affects how efficiently the expansion of the exhaust gases is converted into linear motion. The simplest nozzle shape has a ~15° cone half-angle, which is about 98% efficient. Smaller angles give very slightly higher efficiency, larger angles give lower efficiency.
More complex shapes of revolution are frequently used, such as bell nozzle
The bell-shaped or contour nozzle is probably the most commonly used shaped rocket engine nozzle. It has a high angle expansion section (20 to 50 degrees) right behind the nozzle throat; this is followed by a gradual reversal of nozzle contour slo ...
s or parabolic shapes. These give perhaps 1% higher efficiency than the cone nozzle and can be shorter and lighter. They are widely used on launch vehicles and other rockets where weight is at a premium. They are, of course, harder to fabricate, so are typically more costly.
There is also a theoretically optimal nozzle shape for maximal exhaust speed. However, a shorter bell shape is typically used, which gives better overall performance due to its much lower weight, shorter length, lower drag losses, and only very marginally lower exhaust speed.[PWR Engineering: Nozzle Design](_blank)
Other design aspects affect the efficiency of a rocket nozzle. The nozzle's throat should have a smooth radius. The internal angle that narrows to the throat also has an effect on the overall efficiency, but this is small. The exit angle of the nozzle needs to be as small as possible (about 12°) in order to minimize the chances of separation problems at low exit pressures.
Advanced designs
A number of more sophisticated designs have been proposed for altitude compensation and other uses.
Nozzles with an atmospheric boundary include:
* expansion-deflection nozzle,
* plug nozzle The plug nozzle is a type of nozzle which includes a centerbody or plug around which the working fluid flows. Plug nozzles have applications in aircraft, rockets, and numerous other fluid flow devices.
Hoses
Common garden hose trigger nozzles ar ...
,
* aerospike,[p. 84]
/ref>
* single-expansion ramp nozzle (SERN), a linear expansion nozzle, where the gas pressure transfers work only on one side and which could be described as a single-sided aerospike nozzle.
Each of these allows the supersonic flow to adapt to the ambient pressure by expanding or contracting, thereby changing the exit ratio so that it is at (or near) optimal exit pressure for the corresponding altitude. The plug and aerospike nozzles are very similar in that they are radial in-flow designs but plug nozzles feature a solid centerbody (sometimes truncated) and aerospike nozzles have a "base-bleed" of gases to simulate a solid center-body. ED nozzles are radial out-flow nozzles with the flow deflected by a center pintle.
Controlled flow-separation nozzles include:
* expanding nozzle
The expanding nozzle is a type of rocket nozzle that, unlike traditional designs, maintains its efficiency at a wide range of altitudes. It is a member of the class of altitude compensating nozzles, a class that also includes the plug nozzle and ...
,
* bell nozzles with a removable insert,
* stepped nozzles
A stepped nozzle (or dual-bell nozzle) is a de Laval rocket nozzle which has altitude compensating properties.
The characteristic of this kind of nozzle is that part of the way along the inside of the nozzle there is a straightening of the cur ...
, or dual-bell nozzles.Journal of Propulsion and Power Vol.18 No.1, "Experimental and Analytical Design Verification of the Dual-Bell Concept", Hagemann et al.
These are generally very similar to bell nozzles but include an insert or mechanism by which the exit area ratio can be increased as ambient pressure is reduced.
Dual-mode nozzles include:
* dual-expander nozzle,
* dual-throat nozzle.
These have either two throats or two thrust chambers (with corresponding throats). The central throat is of a standard design and is surrounded by an annular throat, which exhausts gases from the same (dual-throat) or a separate (dual-expander) thrust chamber. Both throats would, in either case, discharge into a bell nozzle. At higher altitudes, where the ambient pressure is lower, the central nozzle would be shut off, reducing the throat area and thereby increasing the nozzle area ratio. These designs require additional complexity, but an advantage of having two thrust chambers is that they can be configured to burn different propellants or different fuel mixture ratios. Similarly, Aerojet has also designed a nozzle called the "Thrust Augmented Nozzle",[Thrust Augmented Nozzle](_blank)
/ref>[THRUST AUGMENTED NOZZLE (TAN) the New Paradigm for Booster Rockets](_blank)
/ref> which injects propellant and oxidiser directly into the nozzle section for combustion, allowing larger area ratio nozzles to be used deeper in an atmosphere than they would without augmentation due to effects of flow separation. They would again allow multiple propellants to be used (such as RP-1), further increasing thrust.
Liquid injection thrust vectoring nozzles are another advanced design that allow pitch and yaw control from un-gimbaled nozzles. India's PSLV
The Polar Satellite Launch Vehicle (PSLV) is an expendable medium-lift launch vehicle designed and operated by the Indian Space Research Organisation (ISRO). It was developed to allow India to launch its Indian Remote Sensing (IRS) satellites ...
calls its design "Secondary Injection Thrust Vector Control System"; strontium perchlorate is injected through various fluid paths in the nozzle to achieve the desired control. Some ICBMs and boosters, such as the Titan IIIC
The Titan IIIC was an expendable launch system used by the United States Air Force from 1965 until 1982. It was the first Titan booster to feature large solid rocket motors and was planned to be used as a launcher for the Dyna-Soar, though the ...
and Minuteman II
The LGM-30 Minuteman is an American land-based intercontinental ballistic missile (ICBM) in service with the Air Force Global Strike Command. , the LGM-30G Minuteman III version is the only land-based ICBM in service in the United States and re ...
, use similar designs.
See also
*Choked flow
Choked flow is a compressible flow effect. The parameter that becomes "choked" or "limited" is the fluid velocity.
Choked flow is a fluid dynamic condition associated with the venturi effect. When a flowing fluid at a given pressure and temperatu ...
– when a gas velocity reaches the speed of sound in the gas as it flows through a restriction
*De Laval nozzle
A de Laval nozzle (or convergent-divergent nozzle, CD nozzle or con-di nozzle) is a tube which is pinched in the middle, making a carefully balanced, asymmetric hourglass shape. It is used to accelerate a compressible fluid to supersonic speeds ...
– a convergent-divergent nozzle designed to produce supersonic speeds
*Dual-thrust
In a dual-thrust solid propellant rocket engine, the propellant mass is composed of two different types (densities) of fuel. In the case of a tandem dual-thrust motor, the fuel nearest to the rocket nozzle burns fast, and the fuel further into the ...
rocket motors
*Giovanni Battista Venturi
Giovanni Battista Venturi (11 September 1746 – 10 September 1822) was an Italian physicist, savant, man of letters, diplomat and historian of science. He was the discoverer of the Venturi effect, which was described in 1797 in his ''Recherches E ...
*Jet engine
A jet engine is a type of reaction engine discharging a fast-moving jet of heated gas (usually air) that generates thrust by jet propulsion. While this broad definition can include rocket, Pump-jet, water jet, and hybrid propulsion, the term ...
– engines propelled by jets (including rockets)
*Multistage rocket
A multistage rocket or step rocket is a launch vehicle that uses two or more rocket ''stages'', each of which contains its own engines and propellant. A ''tandem'' or ''serial'' stage is mounted on top of another stage; a ''parallel'' stage i ...
*NK-33
The NK-33 and NK-43 are rocket engines designed and built in the late 1960s and early 1970s by the Kuznetsov Design Bureau. The NK designation is derived from the initials of chief designer Nikolay Kuznetsov. The NK-33 was among the most powerf ...
– Russian rocket engine
*Pulse jet engine
300px, Diagram of a pulsejet
A pulsejet engine (or pulse jet) is a type of jet engine in which combustion occurs in pulses. A pulsejet engine can be made with few or no moving parts, and is capable of running statically (i.e. it does not need ...
*Pulsed rocket motor
A pulsed rocket motor is typically defined as a multiple pulse solid-fuel rocket motor. This design overcomes the limitation of solid propellant motors being unable to be easily shut down and reignited. The pulse rocket motor allows the motor to b ...
*Reaction Engines Skylon
Skylon is a series of concept designs for a reusable single-stage-to-orbit spaceplane by the British company Reaction Engines Limited (Reaction), using SABRE (rocket engine), SABRE, a combined-cycle, Air breathing engines, air-breathing rocket ...
– a single-stage-to-orbit spaceplane powered by hybrid air-breathing/internal-oxygen engine (Reaction Engines SABRE
SABRE (Synergetic Air Breathing Rocket Engine) is a concept under development by Reaction Engines Limited for a hypersonic precooled hybrid air-breathing rocket engine. The engine is being designed to achieve single-stage-to-orbit capability, ...
)
*Rocket
A rocket (from it, rocchetto, , bobbin/spool) is a vehicle that uses jet propulsion to accelerate without using the surrounding air. A rocket engine produces thrust by reaction to exhaust expelled at high speed. Rocket engines work entirely fr ...
– rocket vehicles
*Rocket engines
A rocket engine uses stored rocket propellants as the reaction mass for forming a high-speed propulsive jet of fluid, usually high-temperature gas. Rocket engines are reaction engines, producing thrust by ejecting mass rearward, in accordanc ...
– used to propel rocket vehicles
* SERN, Single-expansion ramp nozzle – a non-axisymmetric aerospike
*Shock diamond
Shock diamonds (also known as Mach diamonds or thrust diamonds) are a formation of standing wave patterns that appear in the supersonic exhaust plume of an aerospace propulsion system, such as a supersonic jet engine, rocket, ramjet, or scramjet ...
s – the visible bands formed in the exhaust of rocket engines
*Solid-fuel rocket
A solid-propellant rocket or solid rocket is a rocket with a rocket engine that uses solid propellants ( fuel/oxidizer). The earliest rockets were solid-fuel rockets powered by gunpowder; they were used in warfare by the Arabs, Chinese, Persian ...
*Spacecraft propulsion
Spacecraft propulsion is any method used to accelerate spacecraft and artificial satellites. In-space propulsion exclusively deals with propulsion systems used in the vacuum of space and should not be confused with space launch or atmospheric e ...
*Specific impulse
Specific impulse (usually abbreviated ) is a measure of how efficiently a reaction mass engine (a rocket using propellant or a jet engine using fuel) creates thrust. For engines whose reaction mass is only the fuel they carry, specific impulse i ...
– a measure of exhaust speed
* Staged combustion cycle (rocket) – a type of rocket engine
*Venturi effect
The Venturi effect is the reduction in fluid pressure that results when a fluid flows through a constricted section (or choke) of a pipe. The Venturi effect is named after its discoverer, the 18th century Italian physicist, Giovanni Battista V ...
References
External links
Exhaust gas velocity calculator
NASA Space Vehicle Design Criteria, Liquid Rocket Engine Nozzles
NASA's "Beginners' Guide to Rockets"
The Aerospike Engine
Richard Nakka's Experimental Rocketry Web Site
Free Design Tool for Liquid Rocket Engine Thermodynamic Analysis
{{Machine configurations, state=uncollapsed
Nozzles
Rocket propulsion
Pyrotechnics