
A free-turbine turboshaft is a form of
turboshaft
A turboshaft engine is a form of gas turbine that is optimized to produce shaftpower rather than jet thrust. In concept, turboshaft engines are very similar to turbojets, with additional turbine expansion to extract heat energy from the exhaust ...
or
turboprop
A turboprop is a turbine engine that drives an aircraft propeller.
A turboprop consists of an intake, reduction gearbox, compressor, combustor, turbine, and a propelling nozzle. Air enters the intake and is compressed by the compressor. ...
gas turbine engine
A gas turbine, also called a combustion turbine, is a type of continuous flow internal combustion engine. The main parts common to all gas turbine engines form the power-producing part (known as the gas generator or core) and are, in the direct ...
where the power is extracted from the exhaust stream of a gas turbine by an independent turbine, downstream of the gas turbine. The power turbine is not mechanically connected to the turbines that drive the compressors, hence the term "free", referring to the independence of the power output shaft (or spool). This is opposed to the power being extracted from the turbine/compressor shaft via a gearbox.
The advantage of the free turbine is that the two turbines can operate at different speeds and that these speeds can vary relative to each other. This is particularly advantageous for varying loads, such as turboprop engines.
Design
A free-turbine turboshaft ingests air through an intake. The air passes through a compressor and into a
combustor
A combustor is a component or area of a gas turbine, ramjet, or scramjet engine where combustion takes place. It is also known as a burner, combustion chamber or flame holder. In a gas turbine engine, the ''combustor'' or combustion chamber is f ...
where fuel is mixed with the compressed air and ignited. The combustion gases are expanded through a compressor-driving turbine, and then through a "free" power turbine before being exhausted to the atmosphere. The compressor and its turbine are connected by a common shaft which, together with the combustor, is known as a gas generator, which is modelled using the
Brayton Cycle
The Brayton cycle is a thermodynamic cycle that describes the operation of certain heat engines that have air or some other gas as their working fluid. The original Brayton engines used a piston compressor and piston expander, but modern gas tu ...
. The (free) power turbine is on a separate shaft.
Turboshaft engines are sometimes characterized by the number of spools. This refers to the number of compressor-and-turbine assemblies in the gas generator stage and does not include the free power turbine assembly. As an example, the
General Electric T64
The General Electric T64 is a free-turbine turboshaft engine that was originally developed for use on helicopters, but which was later used on fixed-wing aircraft as well. General Electric introduced the engine in 1964. The original engine desig ...
is a single-spool design that uses a 14-stage axial compressor; the independent power shaft is coaxial with the gas generator shaft.
Risk of overspeed
One particular failure scenario, a gearbox failure, showed a free-turbine arrangement to be more at risk than a single-shaft turboprop. It could suffer a turbine
overspeed
Overspeed is a condition in which an engine is allowed or forced to turn beyond its design limit. The consequences of running an engine too fast vary by engine type and model and depend upon several factors, the most important of which are the du ...
to destruction after losing its connection to the propeller load. (In a single-shaft arrangement with a similar gearbox failure the turbine would still have most of its load from the compressor). Such a failure resulted in the 1954 accident of the second prototype
Bristol Britannia
The Bristol Type 175 Britannia is a retired British medium-to-long-range airliner built by the Bristol Aeroplane Company in 1952 to fly across the Commonwealth. During development two prototypes were lost and the turboprop engines proved ...
, G-ALRX, which was forced to land in the
Severn Estuary
The Severn Estuary ( cy, Aber Hafren) is the estuary of the River Severn, flowing into the Bristol Channel between South West England and South Wales. Its high tidal range, approximately , means that it has been at the centre of discussions in t ...
. A failure in the
Bristol Proteus
The Bristol Proteus was the Bristol Engine Company's first mass-produced gas turbine engine design, a turboprop that delivered just over 4,000 hp (3,000 kW). The Proteus was a reverse-flow gas turbine. Because the second turbine dro ...
propeller reduction gearbox led to an overspeed and release of the power turbine of NÂș3 engine. It cut through the oil tank and started a fire that threatened the integrity of the
wing spar
In a fixed-wing aircraft, the spar is often the main structural member of the wing, running spanwise at right angles (or thereabouts depending on wing sweep) to the fuselage. The spar carries flight loads and the weight of the wings while on t ...
. The pilot, Bill Pegg, made a forced landing on the estuary mud.
The Proteus gears were redesigned and an emergency fuel shut-off device was fitted to prevent a similar reoccurrence. Writing in 1994, Gunston
found it remarkable that protection was not common on free-turbine engines. However, certification regulations allow other methods for preventing excessive overspeed such as disc rubbing and blade interference.
Applications
Most turboshaft and turboprop engines now use free turbines. This includes those for static power generation, as marine propulsion and particularly for helicopters.
Helicopters
Helicopter
A helicopter is a type of rotorcraft in which lift and thrust are supplied by horizontally spinning rotors. This allows the helicopter to take off and land vertically, to hover, and to fly forward, backward and laterally. These attribu ...
s are a major market for turboshaft engines. When turboshaft engines became available in the 1950s, they were rapidly adopted for both new designs and as replacements for piston engines. They offered more power and far better power to weight ratios. Piston helicopters of this period had barely adequate performance; the switch to a turbine engine could both reduce several hundred pounds of engine weight, for the
Napier Gazelle
The Napier Gazelle is a turboshaft helicopter engine that was manufactured by D. Napier & Son in the mid-1950s. In 1961 production was nominally transferred to a joint venture with Rolls-Royce called Napier Aero Engines Limited."ENGLISH ELEC ...
of the
Westland Wessex
The Westland Wessex is a British-built turbine-powered development of the Sikorsky H-34 (in US service known as Choctaw). It was developed and produced under licence by Westland Aircraft (later Westland Helicopters). One of the main changes ...
,
and also allow considerably more payload weight. For the
Westland Whirlwind Westland or Westlands may refer to:
Places
*Westlands, an affluent neighbourhood in the city of Nairobi, Kenya
* Westlands, Staffordshire, a suburban area and ward in Newcastle-under-Lyme
*Westland, a peninsula of the Shetland Mainland near Vaila, ...
, this converted the inadequate piston-engined HAS.7 to the
de Havilland Gnome
The Rolls-Royce Gnome is a British turboshaft engine originally developed by the de Havilland Engine Company as a licence-built General Electric T58, an American mid-1950s design. The Gnome came to Rolls-Royce after their takeover of Bristol S ...
turbine-powered HAR.9. As one of the first anti-submarine helicopters, the HAS.7 had been so weight restricted that it could carry either a search sonar ''or'' a torpedo, but not both.
The free-turbine engine was found to be particularly suitable. It does not need a clutch, as the gas generator may be started while the output shaft remains stationary. For the Wessex, this was used to give a particularly fast take-off from a cold start. By locking the main rotor (and the power turbine) with the rotor brake, the engine could be started and then, with the gas generator at a speed of 10,500 rpm, the brake released allowing the power turbine to accelerate and bring the rotor to its operating speed from stationary in just 15 seconds and a time from engine start to take-off of only 30 seconds.
A further advantage of the free turbine design was the ease with which a counter-rotating engine could be designed and manufactured, simply by reversing the power turbine alone.
This allowed handed engines to be made in pairs when needed. It also allowed contra-rotating engines, where the gas generator core and power turbine revolved in opposite directions, reducing the overall moment of inertia. For the helicopter engine replacement market, this ability allowed previous engines of either direction to be replaced simply.
Some turboshaft engines' omni-angle freedom of their installation angle also allowed installation into existing helicopter designs, no matter how the previous engines had been arranged.
In time though, the move towards axial LP compressors and so smaller diameter engines encouraged a move to the now-standard layout of one or two engines set side-by-side, horizontally above the cabin.
Aircraft
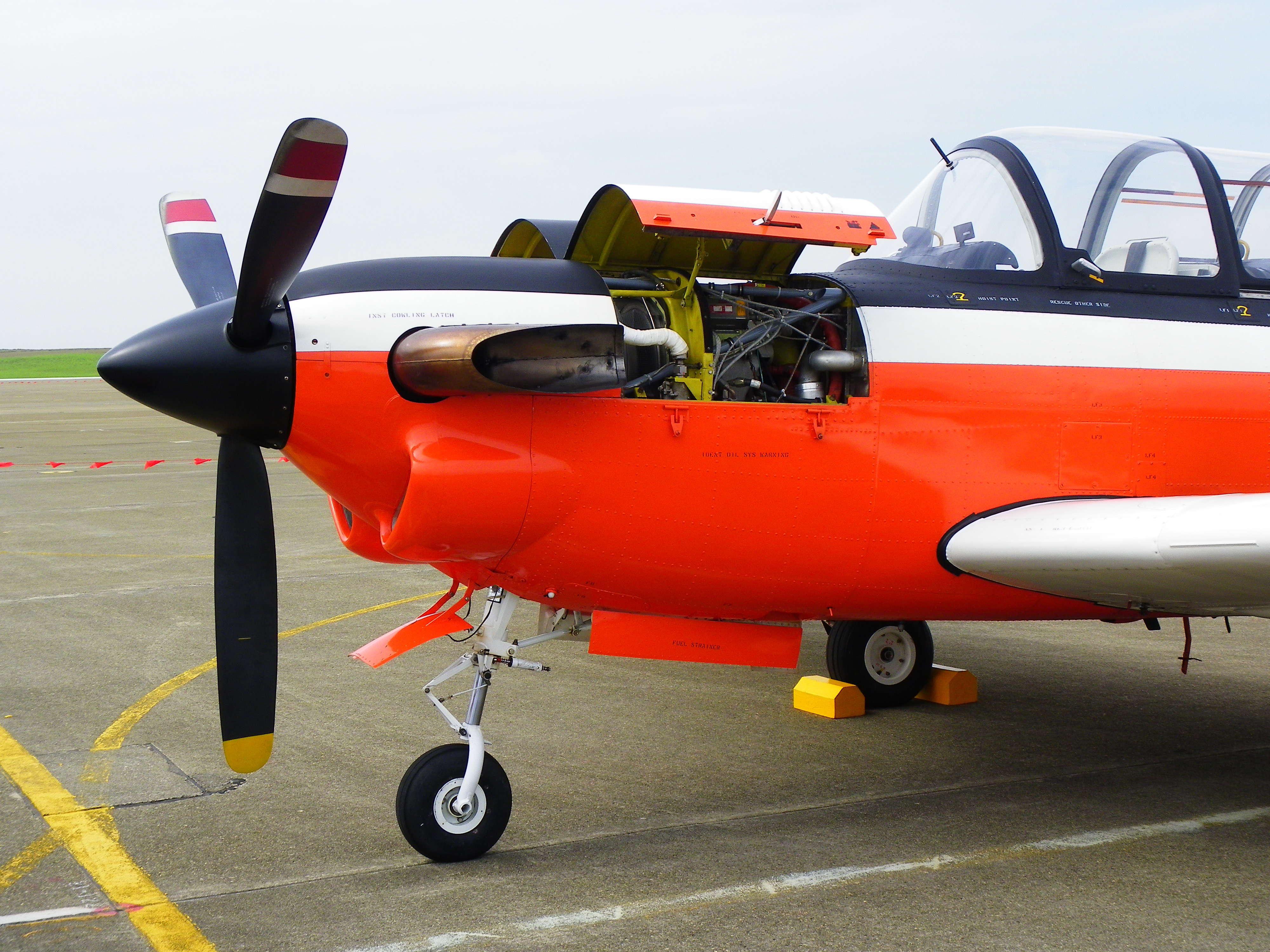
Turboprop aircraft are still powered by a range of free- and non-free turbine engines. Larger engines have mostly retained the non-free design, although many are two-shaft designs where the 'power' turbine drives the propeller and the low-pressure compressor while the high-pressure compressor has its own turbine.
Some large turboprop engines, such as the original
Bristol Proteus
The Bristol Proteus was the Bristol Engine Company's first mass-produced gas turbine engine design, a turboprop that delivered just over 4,000 hp (3,000 kW). The Proteus was a reverse-flow gas turbine. Because the second turbine dro ...
and the modern
TP400 have free turbines. The TP400 is a three-shaft design, with two compressor turbines and a separate power turbine. Where the turbine is at the rear of the engine, a turboprop engine requires a long drive shaft forwards to the
propeller reduction gearbox. Such long shafts can be a difficult design problem and must carefully control any shaft vibration.
For small turboprop engines, the free-turbine design has come to dominate and these designs are also mostly reversed overall, with their air inlet and compressor to the rear, feeding forwards to hot section and power turbine at the front. This places the turbine output close to the propeller gearbox, avoiding the need for a long driveshaft. Such engines are often recognisable externally, as they use external 'elbow' exhausts ahead of the main engine. A particularly common example of this is the
PT6
The Pratt & Whitney Canada PT6 is a turboprop aircraft engine produced by Pratt & Whitney Canada.
Its design was started in 1958, it first ran in February 1960, first flew on 30 May 1961, entered service in 1964 and has been continuously up ...
engine, of which over 50,000 have been produced.
Pusher propfans

An attractively simple configuration making use of the free turbine is the
propfan
A propfan, also called an open rotor engine, or unducted fan (as opposed to a ducted fan), is a type of aircraft engine related in concept to both the turboprop and turbofan, but distinct from both. The design is intended to offer the speed an ...
engine, with a rear-mounted
unducted fan
A propfan, also called an open rotor engine, or unducted fan (as opposed to a ducted fan), is a type of aircraft engine related in concept to both the turboprop and turbofan, but distinct from both. The design is intended to offer the speed an ...
in
pusher configuration
In an aircraft with a pusher configuration (as opposed to a tractor configuration), the propeller(s) are mounted behind their respective engine(s). Since a pusher propeller is mounted behind the engine, the drive shaft is in compression in nor ...
, rather than the more familiar tractor layout. The first such engine was the very early and promising
Metropolitan-Vickers F.3 of 1942 with a ducted fan, followed by the unducted and much lighter
F.5. Development of these engines stopped abruptly owing to corporate takeovers, rather than technical reasons. Rolls-Royce continued with design studies for such engines into the 1980s,
as did
GE, but they have yet to appear as commercial engines.
The advantage of the pusher propfan with a free power turbine is its simplicity. The prop blades are attached directly to the outside of the rotating turbine disc. No gearboxes or drive shafts are required. The short length of the rotating components also reduces vibration. The static structure of the engine over this length is a large diameter tube within the turbine. In most designs, two
contra-rotating
Contra-rotating, also referred to as coaxial contra-rotating, is a technique whereby parts of a mechanism rotate in opposite directions about a common axis, usually to minimise the effect of torque. Examples include some aircraft propellers, res ...
rings of turbine and propeller are used. Intermeshed contra-rotating turbines can act as the
guide vanes for each other, removing the need for static vanes.
Land and sea

The
M1 Abrams
The M1 Abrams is a third-generation American main battle tank designed by Chrysler Defense (now General Dynamics Land Systems) and named for General Creighton Abrams. Conceived for modern armored ground warfare and now one of the heaviest ta ...
main battle tank
A main battle tank (MBT), also known as a battle tank or universal tank, is a tank that fills the role of armor-protected direct fire and maneuver in many modern armies. Cold War-era development of more powerful engines, better suspension sys ...
is powered by a
Honeywell AGT1500
The Honeywell AGT1500 is a gas turbine engine. It is the main powerplant of the M1 Abrams series of tanks. The engine was originally designed and produced by the Lycoming Turbine Engine Division in the Stratford Army Engine Plant. In 1995, prod ...
(formerly
Textron
Textron Inc. is an American industrial conglomerate based in Providence, Rhode Island. Textron's subsidiaries include Arctic Cat, Bell Textron, Textron Aviation (which itself includes the Beechcraft, and Cessna brands), and Lycoming Engines. ...
Lycoming) two-spool gas turbine engine. A commercial derivative has been designed as the TF15 for marine and railroad applications, and a flight-rated version, the PLT27, was also developed but lost a major contract to the
GE T700
The General Electric T700 and CT7 are a family of turboshaft and turboprop engines in the class.
Design and development
In 1967, General Electric began work on a new turboshaft engine demonstrator designated the "GE12" in response to US Army i ...
turboshaft.
Turboshaft engines were used to power several
gas turbine locomotive
A gas turbine locomotive is a type of railway locomotive in which the prime mover is a gas turbine. Several types of gas turbine locomotive have been developed, differing mainly in the means by which mechanical power is conveyed to the driving w ...
s, most notably using the
Turbomeca
Safran Helicopter Engines, previously known as Turbomeca, is a French manufacturer of low- and medium-power gas turbine turboshaft engines for helicopters. The company also produces gas turbine engines for aircraft and missiles, as well as turbin ...
Turmo in
Turbotrain
The Turbotrain was any of several French high-speed rail, high-speed, gas turbine trains. The earliest Turbotrain entered service in 1967, for use on France's SNCF intercity lines. There were four versions in total, with the last exiting service ...
(France) and
Turboliner
The Turboliners were a family of gas turbine trainsets built for Amtrak in the 1970s. They were among the first new equipment purchased by Amtrak to update its fleet with faster, more modern trains. The first batch, known as RTG, were built by ...
(United States) service.
See also
*
Free-piston engine
A free-piston engine is a linear, 'crankless' internal combustion engine, in which the piston motion is not controlled by a crankshaft but determined by the interaction of forces from the combustion chamber gases, a rebound device (e.g., a piston i ...
*
Turbo-compound engine
A turbo-compound engine is a reciprocating engine that employs a turbine to recover energy from the exhaust gases. Instead of using that energy to drive a turbocharger as found in many high-power aircraft engines, the energy is instead sent to ...
References
{{Aircraft gas turbine engine components
Gas turbines
Aircraft engines