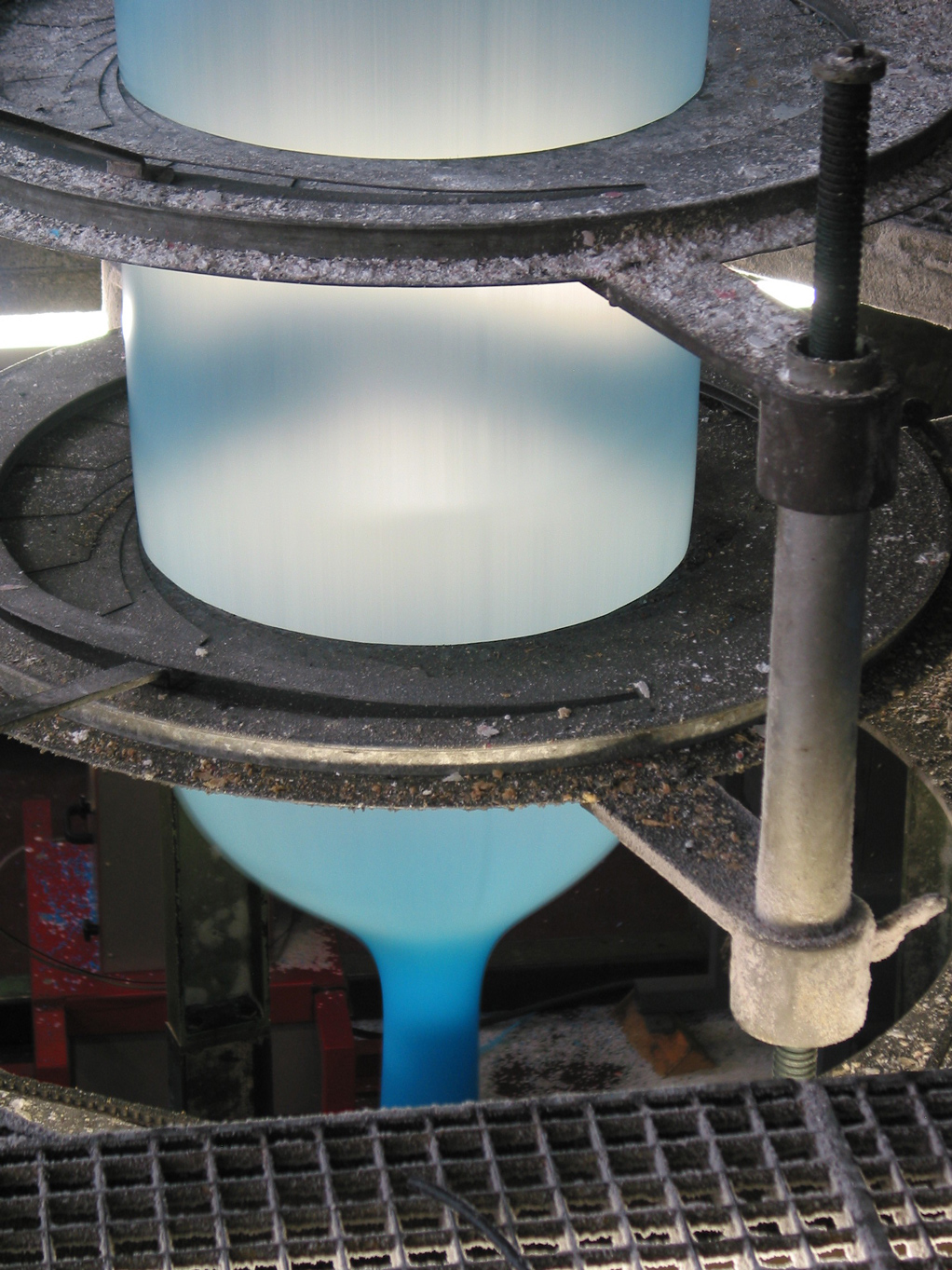
A film blowing machine involves one process used to make
plastic film
Plastic film is a thin continuous polymeric material. Thicker plastic material is often called a "sheet". These thin plastic membranes are used to separate areas or volumes, to hold items, to act as barriers, or as printable surfaces.
Plas ...
. Extruded tubular processing is most often used with
polyethylene
Polyethylene or polythene (abbreviated PE; IUPAC name polyethene or poly(methylene)) is the most commonly produced plastic. It is a polymer, primarily used for packaging ( plastic bags, plastic films, geomembranes and containers including bo ...
films but can be used with other polymers.
The film may be
laminating
Lamination is the technique/process of manufacturing a Raw material, material in multiple layers, so that the composite material achieves improved strength of materials, strength, stability, sound insulation, visual appearance, appearance, or ...
film,
shrink film
Shrink may refer to:
Common meanings
* Miniaturization
*Shrink, a slang term for:
** a psychiatrist
** a psychoanalyst
** a psychologist
Arts, entertainment, and media
* ''Shrink'' (album), album by German indie rock/electronica group The Notw ...
,
agricultural
Agriculture or farming is the practice of cultivating Plant, plants and livestock. Agriculture was the key development in the rise of Sedentism, sedentary human civilization, whereby farming of Domestication, domesticated species created food ...
covering film,
bags or film for
textile
Textile is an umbrella term that includes various fiber-based materials, including fibers, yarns, filaments, threads, different fabric types, etc. At first, the word "textiles" only referred to woven fabrics. However, weaving is not the ...
s and
clothing
Clothing (also known as clothes, apparel, and attire) are items worn on the body. Typically, clothing is made of fabrics or textiles, but over time it has included garments made from animal skin and other thin sheets of materials and natural ...
, and other packaging materials.
Technical information
Parts include: screw and barrel,
motor
An engine or motor is a machine designed to convert one or more forms of energy into mechanical energy.
Available energy sources include potential energy (e.g. energy of the Earth's gravitational field as exploited in hydroelectric power g ...
,
inverter
A power inverter, inverter or invertor is a power electronic device or circuitry that changes direct current (DC) to alternating current (AC). The resulting AC frequency obtained depends on the particular device employed. Inverters do the opp ...
, heaters,
die
Die, as a verb, refers to death, the cessation of life.
Die may also refer to:
Games
* Die, singular of dice, small throwable objects used for producing random numbers
Manufacturing
* Die (integrated circuit), a rectangular piece of a semicondu ...
head, winder, and tower. The main motor may have
frequency control of motor speed to improve speed regulation and save electricity. The screw and material barrel may be made from a
nitrogen-treated chromium
Chromium is a chemical element with the symbol Cr and atomic number 24. It is the first element in group 6. It is a steely-grey, lustrous, hard, and brittle transition metal.
Chromium metal is valued for its high corrosion resistance and hardne ...
-
molybdenum
Molybdenum is a chemical element with the symbol Mo and atomic number 42 which is located in period 5 and group 6. The name is from Neo-Latin ''molybdaenum'', which is based on Ancient Greek ', meaning lead, since its ores were confused with lea ...
-
aluminum
Aluminium (aluminum in American and Canadian English) is a chemical element with the symbol Al and atomic number 13. Aluminium has a density lower than those of other common metals, at approximately one third that of steel. It has ...
alloy
An alloy is a mixture of chemical elements of which at least one is a metal. Unlike chemical compounds with metallic bases, an alloy will retain all the properties of a metal in the resulting material, such as electrical conductivity, ductility, ...
.
Process
At the beginning of the process, the
polymer
A polymer (; Greek '' poly-'', "many" + ''-mer'', "part")
is a substance or material consisting of very large molecules called macromolecules, composed of many repeating subunits. Due to their broad spectrum of properties, both synthetic a ...
comes in the form of a pellet. it is heated and melted into a
viscous liquid
In condensed matter physics and physical chemistry, the terms viscous liquid, supercooled liquid, and glassforming liquid are often used interchangeably to designate liquids that are at the same time highly viscous (see Viscosity of amorphous ma ...
between rotating screws and barrels of the
extruder
Extrusion is a process used to create objects of a fixed cross-sectional profile by pushing material through a die of the desired cross-section. Its two main advantages over other manufacturing processes are its ability to create very complex ...
. This allows for the polymer to be fed through a die that shapes it in the form of a tube. This tube is then carefully inflated, so there is no risk of tearing, into a bubble by injecting it with air. The bubble is simultaneously being cooled in its interior, via a cooling system, and on the exterior surface, through the use of an air ring, to solidify the material. A set of collapsing frames or guides are then used to collapse the bubble into two, more defined, layers within closer proximity. Now that the layers are close, a series of nip rollers flatten the layers together to form a two-layered plastic film that is then wound onto a cylindrical roll for packaging purposes. This process may vary depending upon the
specifications
A specification often refers to a set of documented requirements to be satisfied by a material, design, product, or service. A specification is often a type of technical standard.
There are different types of technical or engineering specificati ...
and models of the machines.
Bubble instabilities
In the case that the bubble formed from air injection is not handled with caution, the bubble may become unstable and deform in a number of different ways.
* Draw resonance exists when the film
velocity
Velocity is the directional speed of an object in motion as an indication of its rate of change in position as observed from a particular frame of reference and as measured by a particular standard of time (e.g. northbound). Velocity is a ...
at which solidification occurs is much higher than the velocity of the melted liquid as it exits the die. This causes the melt to stretch too quickly and the bubble diameter starts to vary along its surface. One way to fix this situation is to increase the speed of the melt through the die.
* Helical instability is noticeable when one side of the bubble is cooled more than the other due to the air ring. The bubble then starts to form a helical shape as it reaches the collapsing frames. This can be avoided by either lowering the melt temperature or increasing extruder output.
* Freezeline height instability results in a variation of the thickness of the bubble. This is caused by extruder motor amps and back pressure. To prevent this variation in thickness, improvements upon the feeding and melting of the material must be implemented.
* Heavy-Bubble instability - Heavy-Bubble instability refers to the bubble sagging towards the bottom. When this occurs it means that it is not being cooled enough. Lowering the freezeline height or lowering the melt temperature will assist the bubble in its cooling face causing less sag.
* Bubble flutter appears below the freezeline when cool air impinges on the surface of the bubble. A higher freezline height, a lower melt temperature, and a narrower die gap can solve this problem.
* Bubble breathing occurs when the volume of the air in the bubble keeps changing periodically. This causes a variation in film thickness. Some solutions include controlling the cooling system and sensors, a reduction of melt temperatures, or decreasing extruder output.
* Bubble tear appears as a tear in the bubble, which happens when the force needed to draw up the bubble into the nip rollers is higher than the
tensile strength
Ultimate tensile strength (UTS), often shortened to tensile strength (TS), ultimate strength, or F_\text within equations, is the maximum stress that a material can withstand while being stretched or pulled before breaking. In brittle materials t ...
of the melted film. A simple solution to this is to reduce extruder output or increase the die and melt temperature.
References
Books and general references
* Hawkins, William E, The Plastic Film and Foil Web Handling Guide CRC Press 2003
*Jenkins, W. A., and Osborn, K. R. Plastic Films: Technology and Packaging Applications, CRC Press 1992
* Yam, K. L., "Encyclopedia of Packaging Technology", John Wiley & Sons, 2009, {{ISBN, 978-0-470-08704-6
Packaging machinery
Industrial equipment